o La producción de estos elementos pretensados debe ser realizada con equipos adecuados y diseñados específicamente para este fin, en bancos de pretensado de línea larga, usando para la conformación de la placa máquinas extrusoras o moldeadoras. El ancho nominal estándar es de 1.200 mm y el rango de espesores puede variar entre 80 y 300 mm, siendo posible la fabricación de hasta 500 mm. Los aligeramientos o alvéolos varían en forma, tamaño y número dependiendo del equipo usado en su manufactura.
o Los bancos de prefabricación varían entre 100 y 200 m de longitud. Los fondos de las camas pueden ser de diversos materiales, aunque se recomienda que sean de acero para mejorar el acabado de la parte inferior de la placa e incorporar sistemas de curado con calor que aceleren el proceso de endurecimiento del concreto. Posteriormente las placas son cortadas de acuerdo con la modulación especifica de cada proyecto.
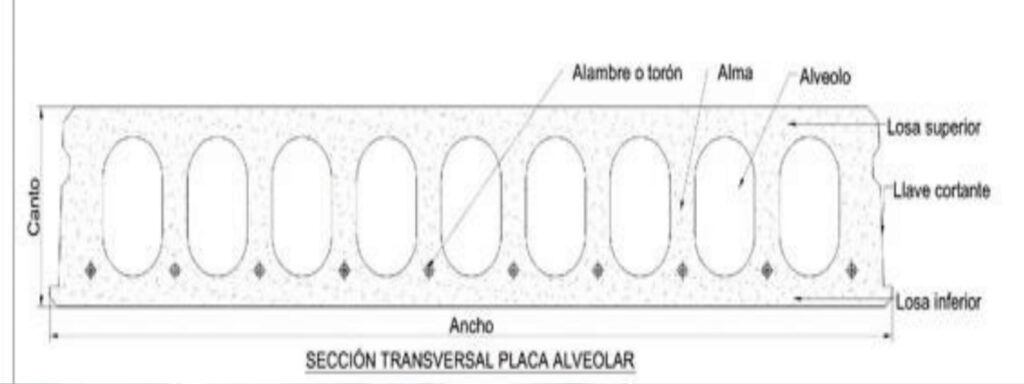
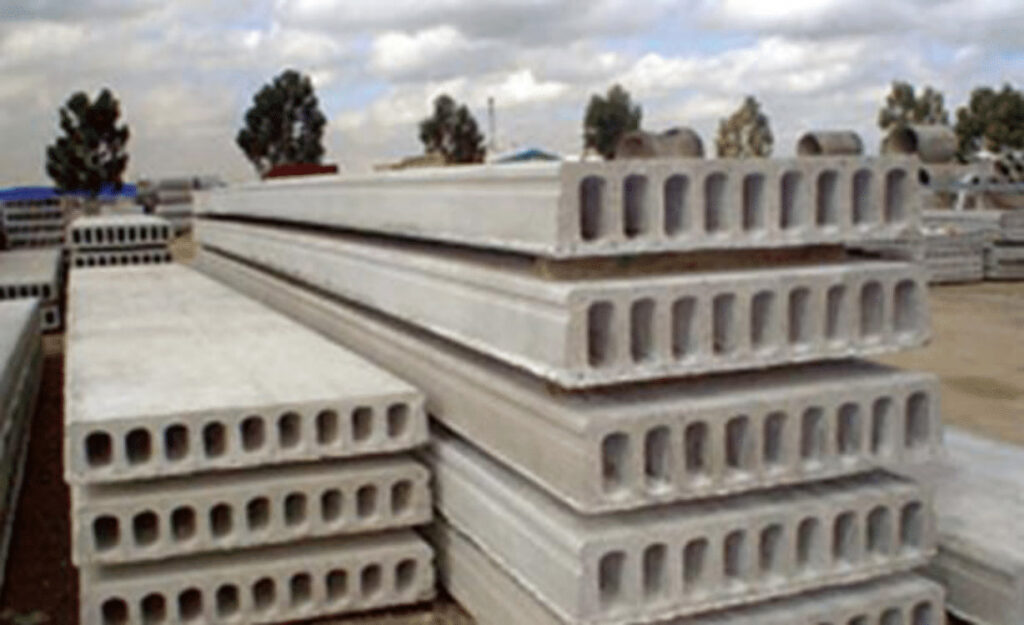
SECCIÓN TRANSVERSAL
FABRICACIÓN
o El proceso productivo de las placas alveolares inicia con la preparación de la pista (línea de producción sobre la cual se funden las placas). Esta se limpia y se le aplica un desencofrante que evita que se le adhiera el concreto; luego se procede a la extensión de los alambres o torones definidos en diseño entre bancadas (extremos de la pista) donde son anclados pasivamente mediante piezas especiales con cuñas; se cortan los alambres o torones y se sujetan al gato hidráulico que tira de ellos traccionándolos hasta la tensión de diseño y se acuñan en la cabeza de anclaje activo, que forma parte de la bancada correspondiente. La bancada desde la cual se traccionan las armaduras recibe el nombre de “activa”, mientras que la opuesta es la “bancada pasiva”, ambas vinculadas a través de la losa de compresión que completa la infraestructura resistente de cada pista de producción.
o Una vez que las armaduras se encuentran pretensadas entre ambas bancadas, se sitúa la máquina moldeadora sobre los carriles de la pista. Al tiempo que la máquina avanza, asegura la posición de la armadura mediante el “guía – hilos” situado en su parte delantera, y va depositando el concreto con la forma y dimensiones que corresponda a la placa alveolar que se esté fabricando.
o La mezcla de concreto debe tener una consistencia muy seca, de modo que mantenga la forma y dimensiones definidas, por lo que debe ser enérgicamente vibrado por la máquina para que envuelva perfectamente los refuerzos y rellene totalmente los moldes deslizantes.
o Terminada esta fase, se cubre la pista con una lona para retener la humedad y evitar cambios bruscos de temperatura durante el proceso de curado del concreto. Una vez se alcanza la resistencia requerida (entre 10 y 12 horas para pistas con calefacción y entre 36 y 48 horas a temperatura ambiente), se procede a distensionar los alambres o torones de refuerzo.
o Posteriormente, las placas alveolares son cortadas a la medida – de acuerdo con la modulación particular de cada proyecto – mediante máquinas cortadoras equipadas con un disco diamantado.
o Finalizado el corte y la marca, las placas se extraen y se trasladan al patio para almacenamiento y posterior despacho.
o Para asegurar la calidad del producto debe elaborarse un plan de ensayos sobre los materiales utilizados en el concreto y acero de refuerzo. Igualmente, a las placas alveolares terminadas se les debe hacer pruebas de resistencia a flexión, cortante y deformación bajo carga.
Descripción
- Coordinación modular
- Despiece de refuerzos
- Especificaciones
- Detalle de conectores entre muros
- Detalle de conectores muro – placa
- Detalle de viga intermedia
- Detalle refuerzo horizontal
- Normas técnicas
Descripción
- Base en afirmado e instalaciones hidráulicas
- Instalación de acero de refuerzo, cimentación y dovelas
- Placa fundida y curado con riego de agua
- Trazado y forme mampostería estructural
- Modulación horizontal dovelas
- Modulación horizontal redes
- Modulación vertical plomado boquilleras
- Colocación de unidades de mampostería usando boquilleras
- Modulación vertical plomado de hilos
- Refuerzo vertical, conectores entre muros
- Colocación de unidades de mampostería usando “Madrino o Punto”
- Detalle templado de hilo
- Corte con pulidora
- Cortadora industrial
- Emboquillado
- Estriado y emboquillado
- Limpieza de celdas para fundir dovelas
- Fundida de dovelas
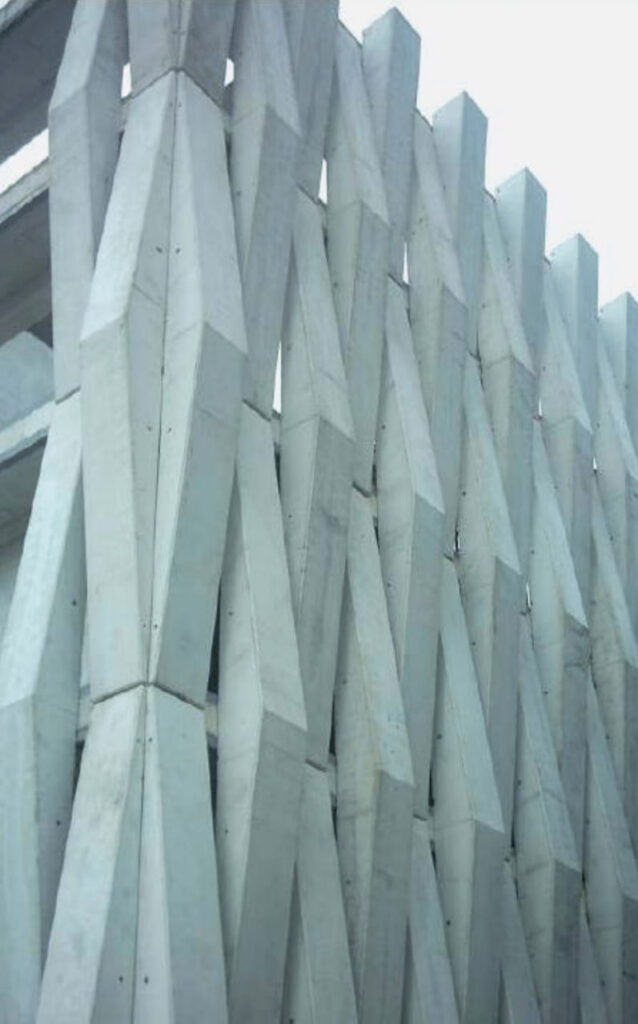
“Fachada prefabricada”
En concreto liviano
o Dado que los elementos prefabricados no tienen funciones estructurales, se requirió el diseño de anclajes metálicos soldados, que mostrarán buen comportamiento ante solicitaciones sísmicas.
o En el proceso de diseño se tienen en cuenta los requerimientos de carga por desencofre izado y montaje de los elementos prefabricados, encontrando que la condición crítica corresponde al izaje.
o Para el diseño y construcción de los elementos de fachada se uso concreto liviano (aligerado con poliestireno expandido y con el uso de aditivos que permiten una distribución uniforme en la mezcla) el peso se reduce entre un 25 y un 50% del peso normal, además se uso concreto de alta resistencia inicial, lo que permitió reducir la resistencia de diseño de 28 a 21 mpa.
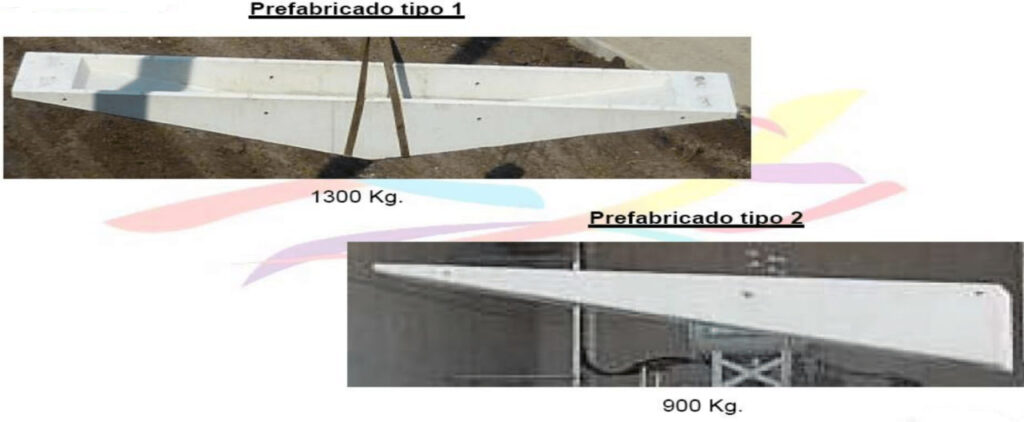
Para obtener excelentes resultados estéticos se tuvo en cuenta:
o Formaletas con ángulos adecuados para el desencofrado.
o Diseño de elementos de izado que evitaron el uso de ganchos metálicos embebidos en el elemento.
o Diseño de elementos para manipular, transportar e izar los elementos, evitando daños por golpes y roces.
Refuerzo en Acero
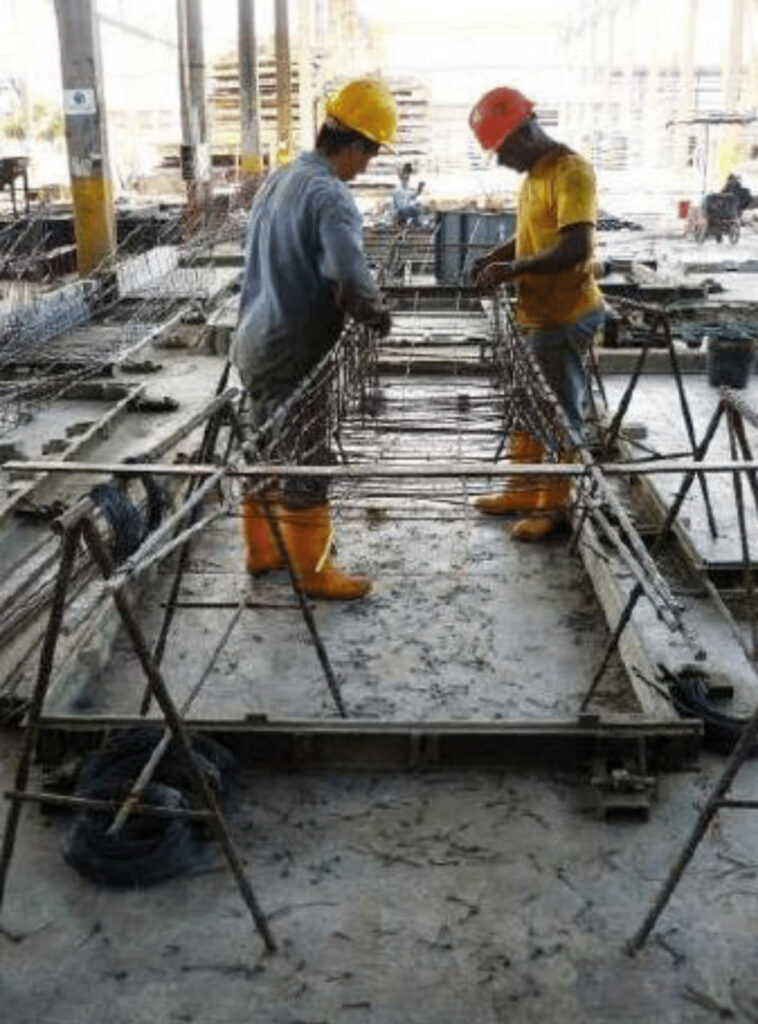
Patio de Almacenamiento
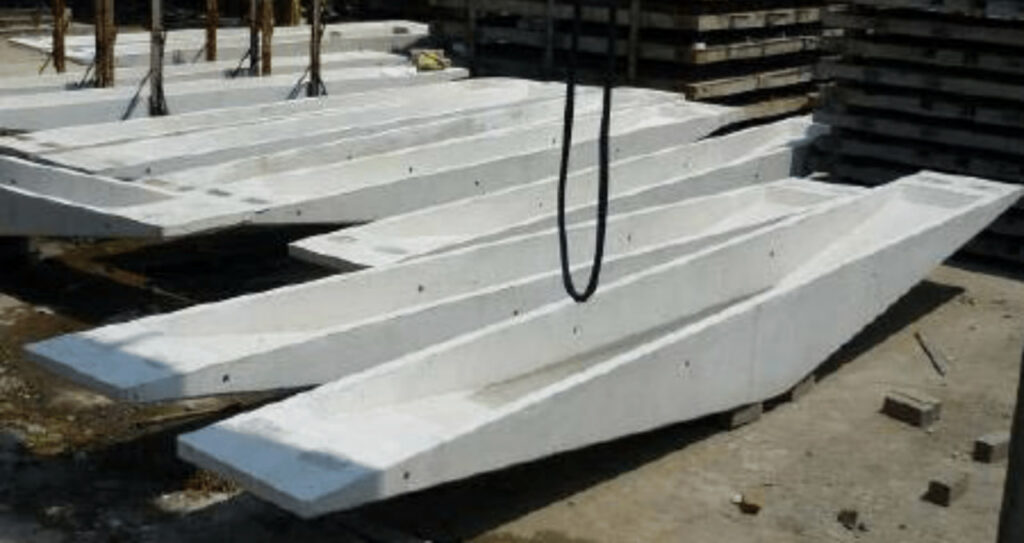
USO DE CONCRETOS CLAROS
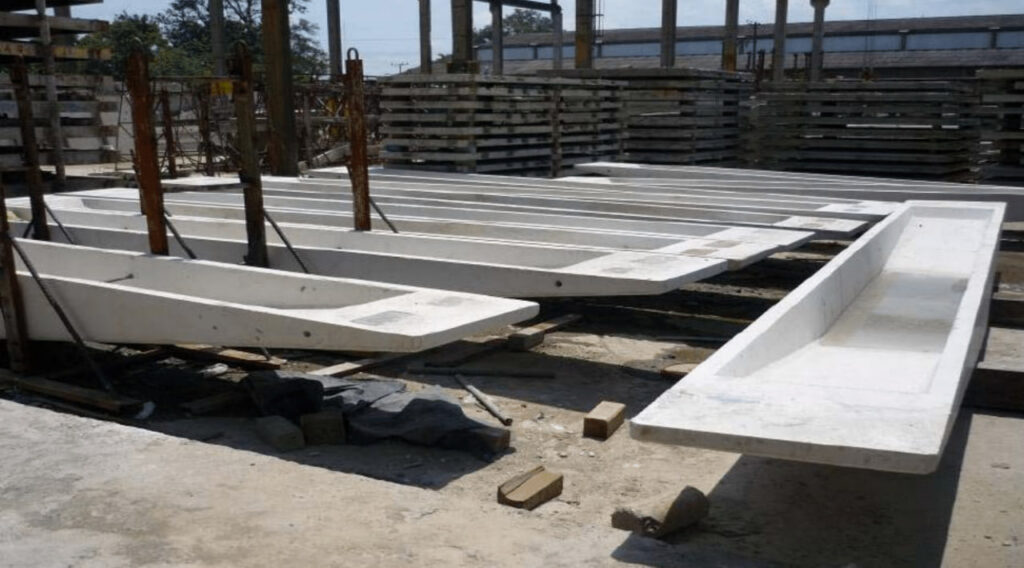
IZAJE DE ELEMENTOS
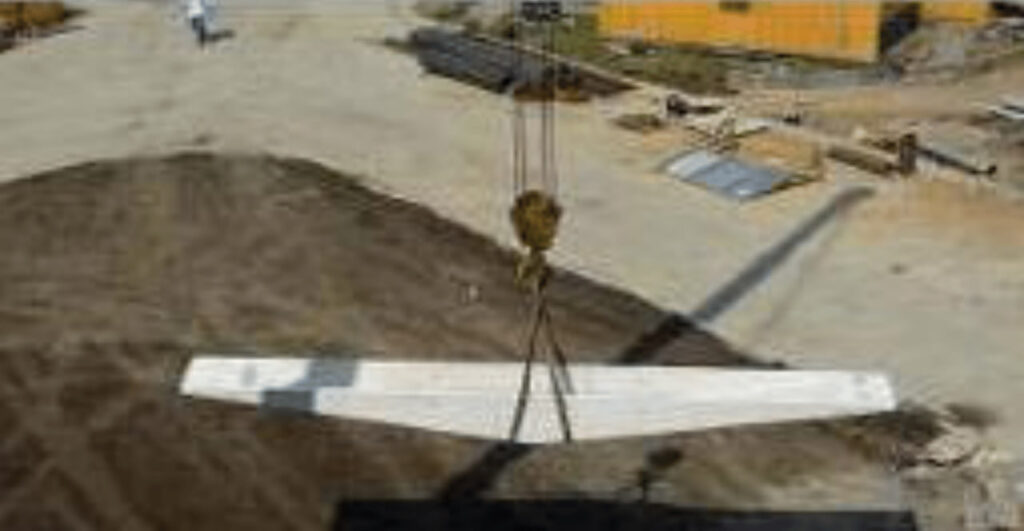
Mega Press
Descripción del proceso
- Patio de materiales
- Acero de refuerzo
- Curado con riego de agua
- Transporte y entrega en obra
- Perforación guía para la hinca
- Enhebrado de primer pilote y alistado para la hinca
- Inicio del proceso de hincado
- Avance proceso de hincado
- Pilote hincado
- Colocación del siguiente pilote a hincar
- Equipo hidráulico para hincado de micropilotes
Pilotes hasta de 5 Metros de longitud hincados con martillo de maza simple
Pasos del proceso constructivo
Paso No. 1:
– Logística y planeación, alistado del terreno y replanteo.
Paso No. 2:
– Elección y organización de equipos.
Paso No. 3:
– Emplazamiento de equipos excavación, alistado de acero de refuerzo.
Paso No. 4:
– Fabricación armaduras de refuerzo y separadores para garantizar recubrimientos.
Paso No. 5:
– Preparación de lodo bentónico para estabilizar las excavaciones.
Paso No. 6:
– Excavación mecánica
– Uso de grúa auxiliar para labores de limpieza.
Paso No. 7:
– Izado e instalación de acero de refuerzo.
Paso No. 8:
– Colocación del concreto
– Tubo Tremie para colocación del concreto.
Paso No. 9:
– Aseo del sitio de trabajo.
– Avance organizado de actividades.
Paso No. 10:
– Excavación mecánica sótano.
Paso No. 11:
– Descabece de pilotes, excavación manual cabezales de cimentación y vigas de amarre.
Apuntalamiento usando las placas de entrepiso de sótanos
El método constructivo que ha dado buenos resultados para limitar los movimiento de la pantalla y arriostrarla definitivamente es el que se ha denominado “construcción simultanea descendente y ascendente de estructuras de edificios”, método muy conveniente cuando se requiere dar carga al terreno, ya sea para evitar el llamado rebote o para eliminar la posibilidad de una falla fondo, y por lo cual es más usado en proyectos de zonas de suelos blandos.
El método requiere ejecutar, al mismo tiempo que la pantalla, perforaciones de gran diámetro o Caisson (1.00 a 1.50 m), en las que se alojan las columnas definitivas de las plantas de sótano, buscando los pilotes de cimentación previamente ejecutados. A continuación se acomete la construcción de las losas de los sótanos, quedando la pantalla arriostrada en todo momento, y se puede comenzar la superestructura incluso antes de terminar la infraestructura de sótanos.
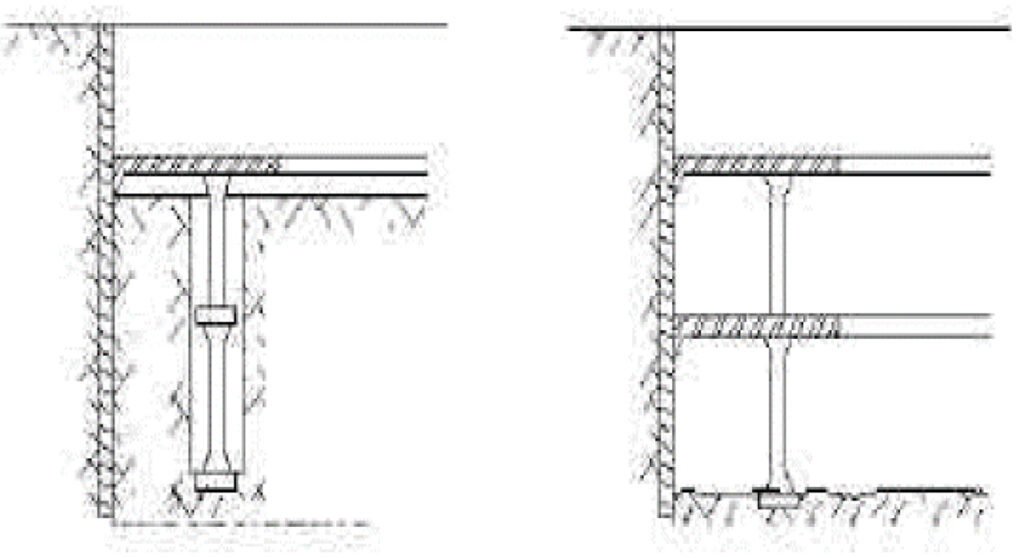
- En el primer paso se ejecutan Caisson de aproximación construyendo el dado y la columna
- Seguidamente se ejecuta la losa del sótano y el primer piso, para luego mientras se eleva la torre se excava el sótano 2.
Excavación inicial
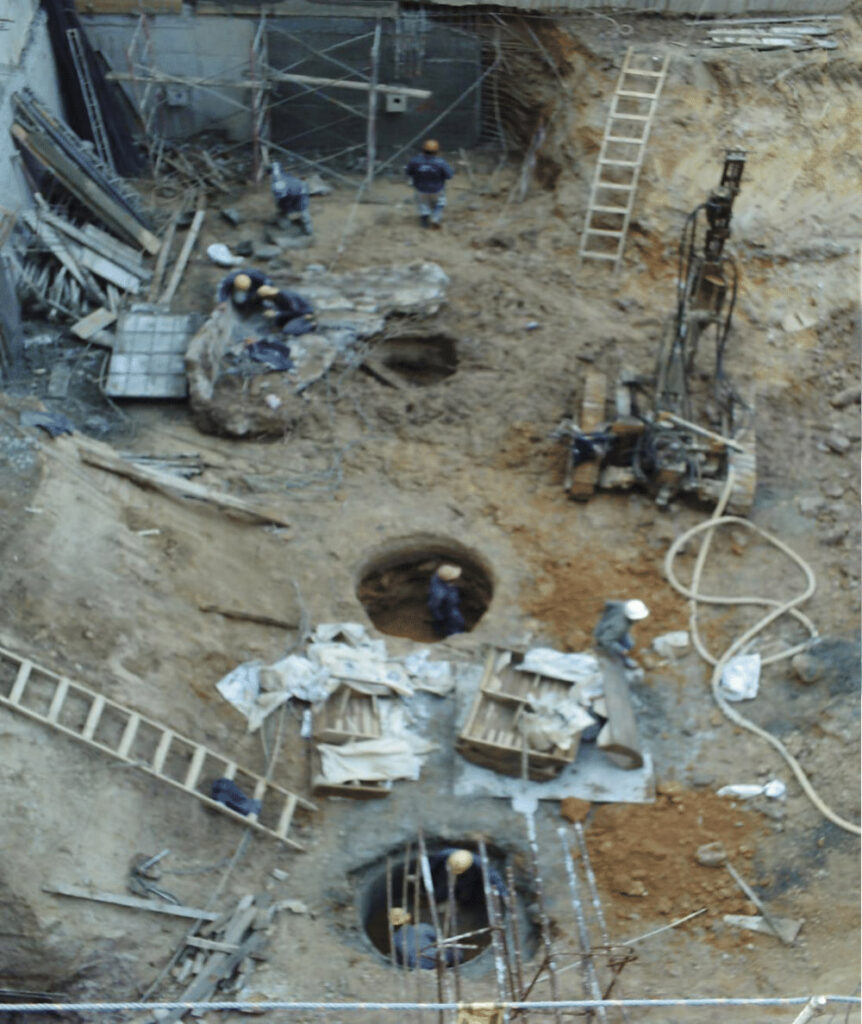
Caisson de aproximación
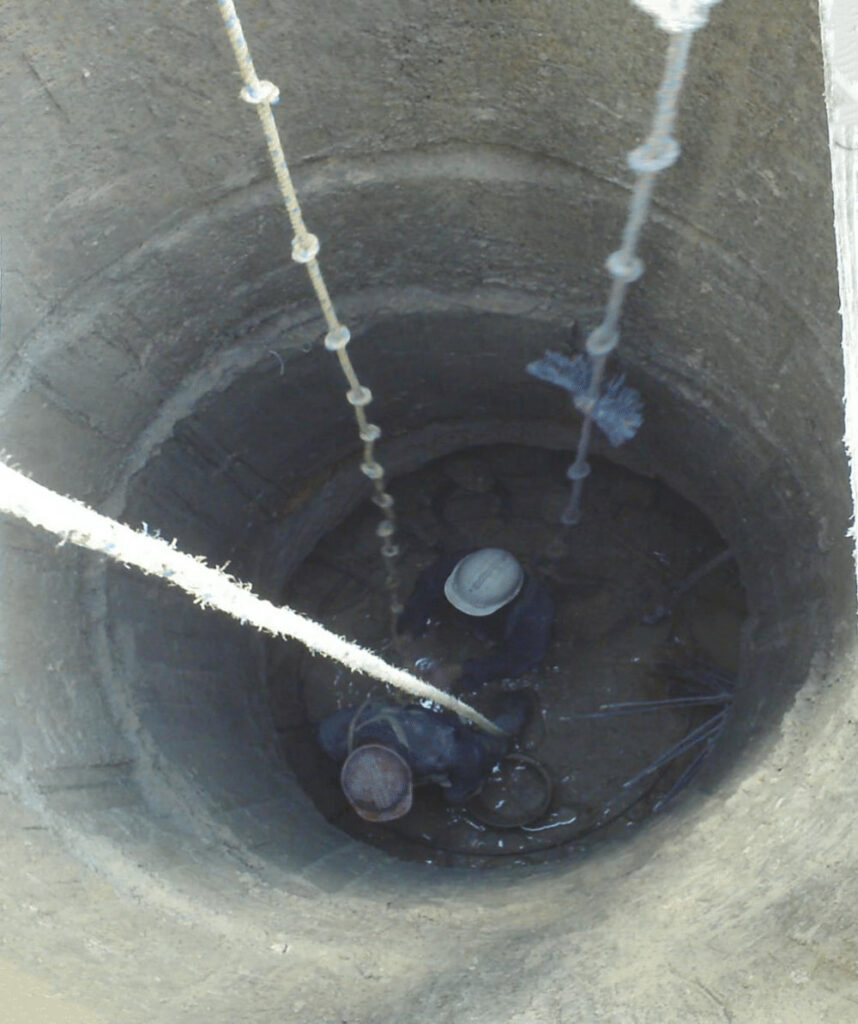
Descabece del pilote y prolongación del acero para columna
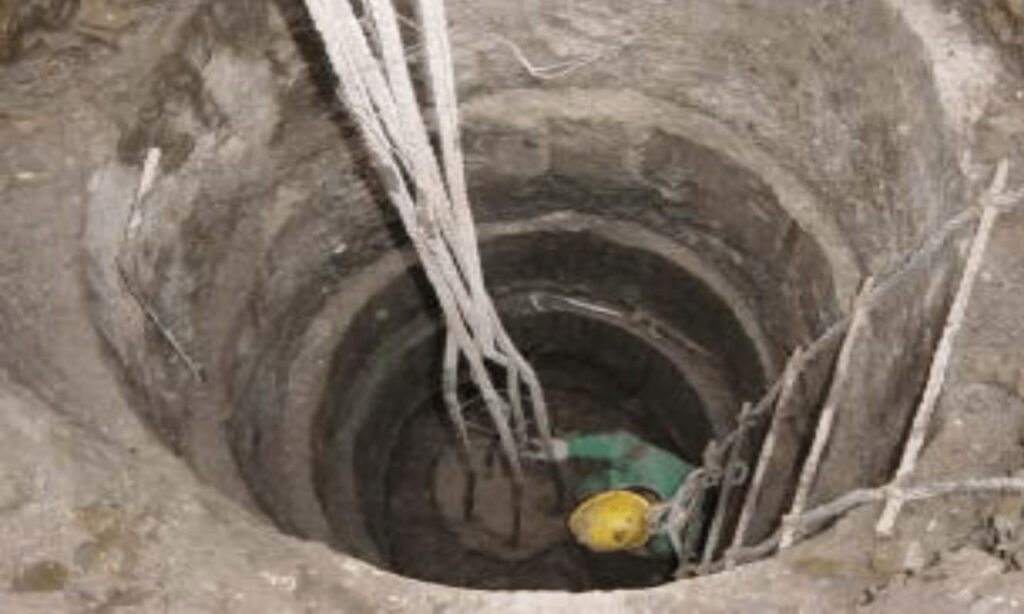
Fundida del dado de cimentación
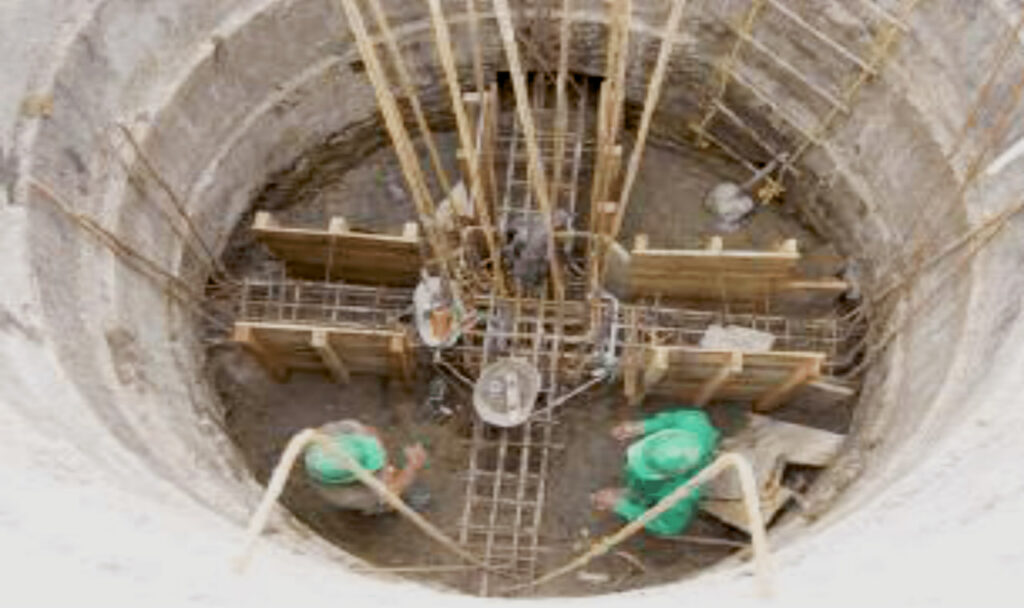
Fundida de la columna hasta la cota de la placa de sótano 2
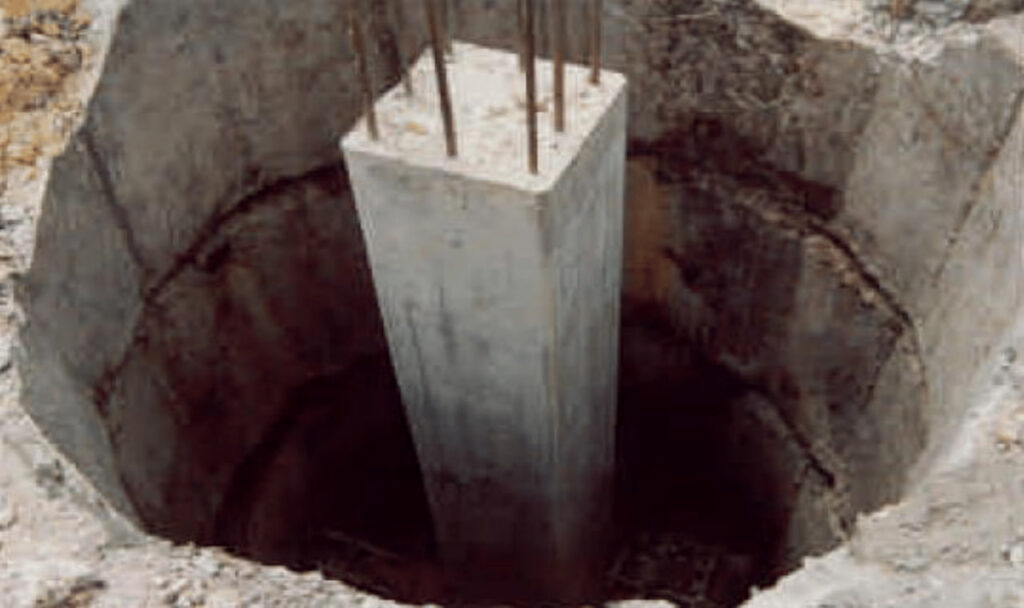
Aquí se presenta barrete lateral desde la cimentación a placa de sótano 2
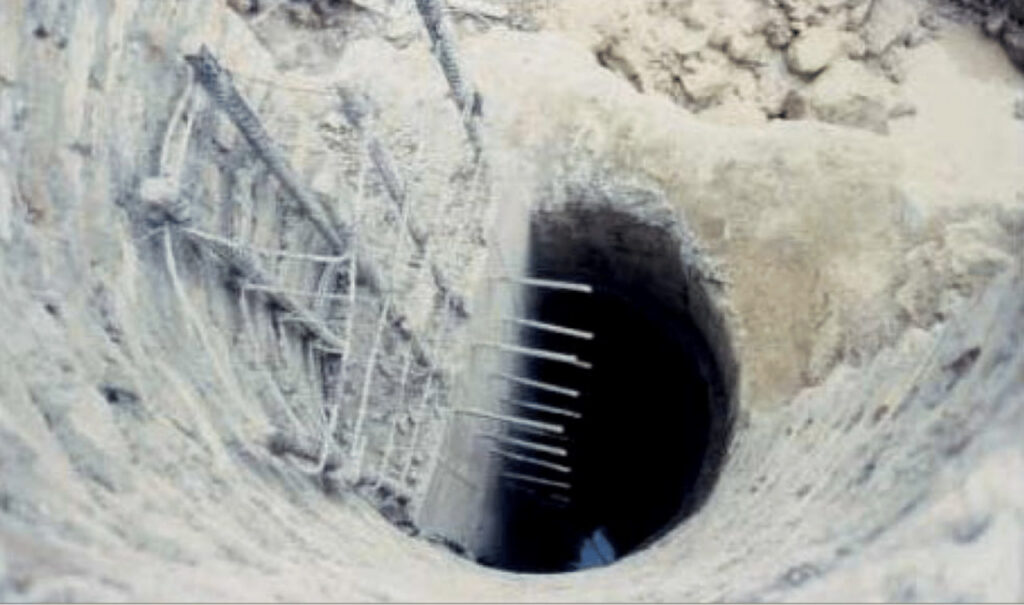
Vista de pantalla embebida en el Caisson
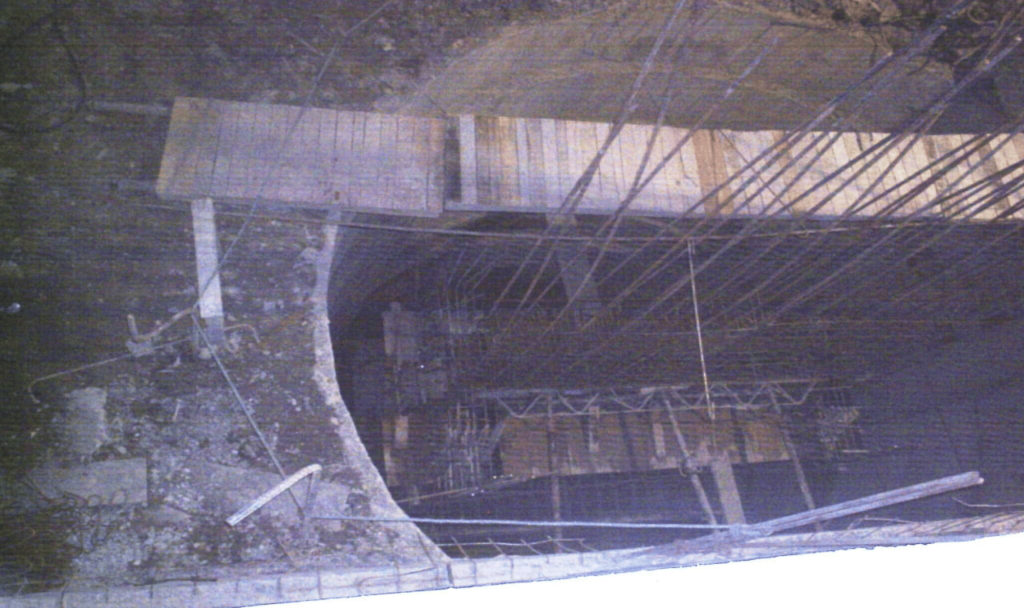
Vista de pantalla dentro del Caisson y la viga de sótano 2 apoyada en pilote temporal
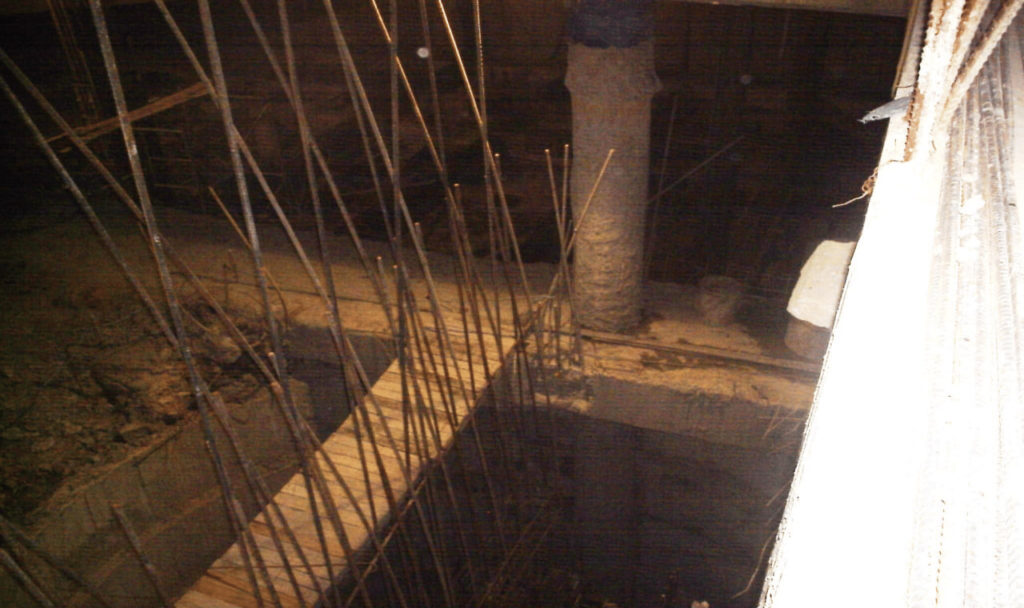
Mientras la superestructura sube en el sótano 2 se realizan las excavaciones, lo que garantiza la estabilidad de las vías aledañas.
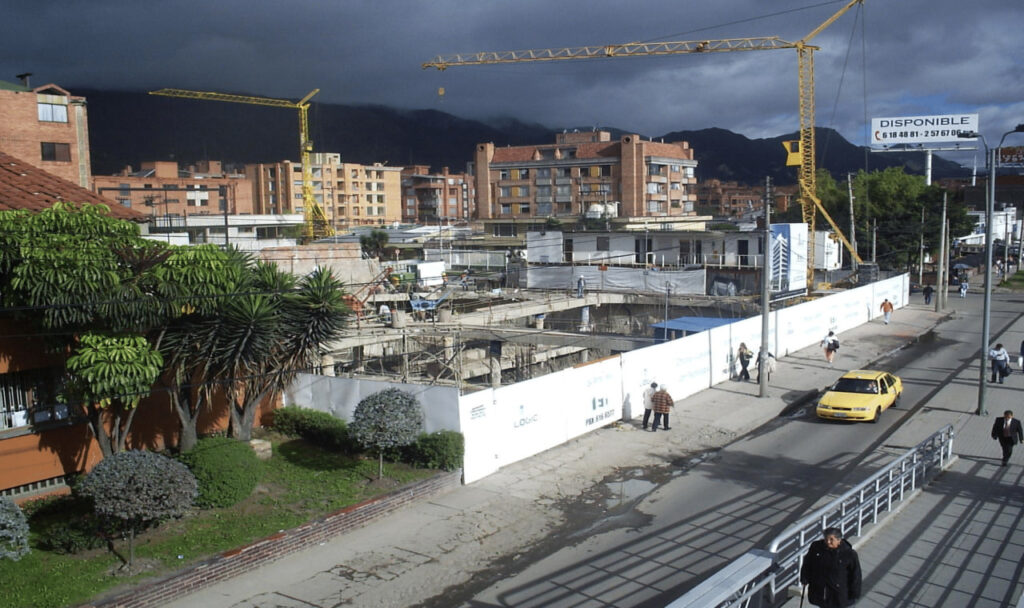
Armado de la placa de sótano 2 y juego de columnas de sótano 2 a primer piso ( ya se ve funcionando el arriostramiento que ejerce la placa sobre la pantalla)
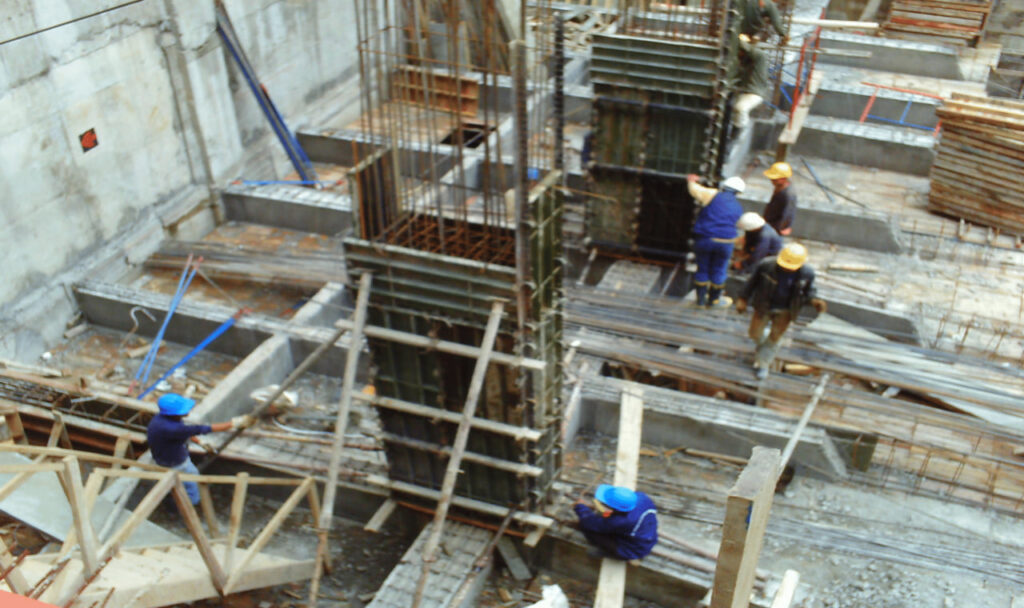
Debe prever un sitio de acceso para equipos y retiro de material de excavación
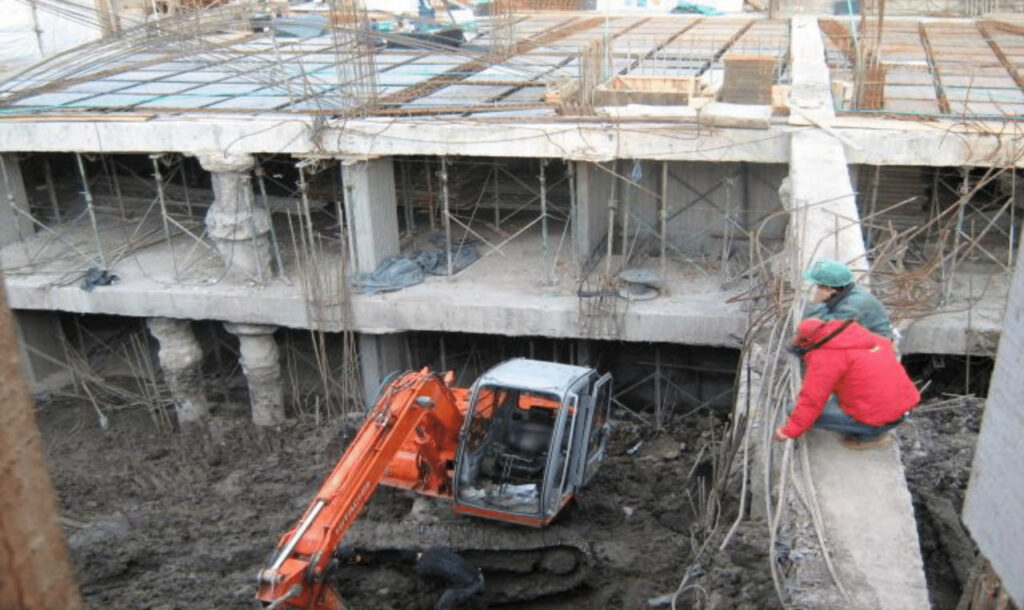
Mientras la superestructura va subiendo en el sótano 2, se realizan las excavaciones.
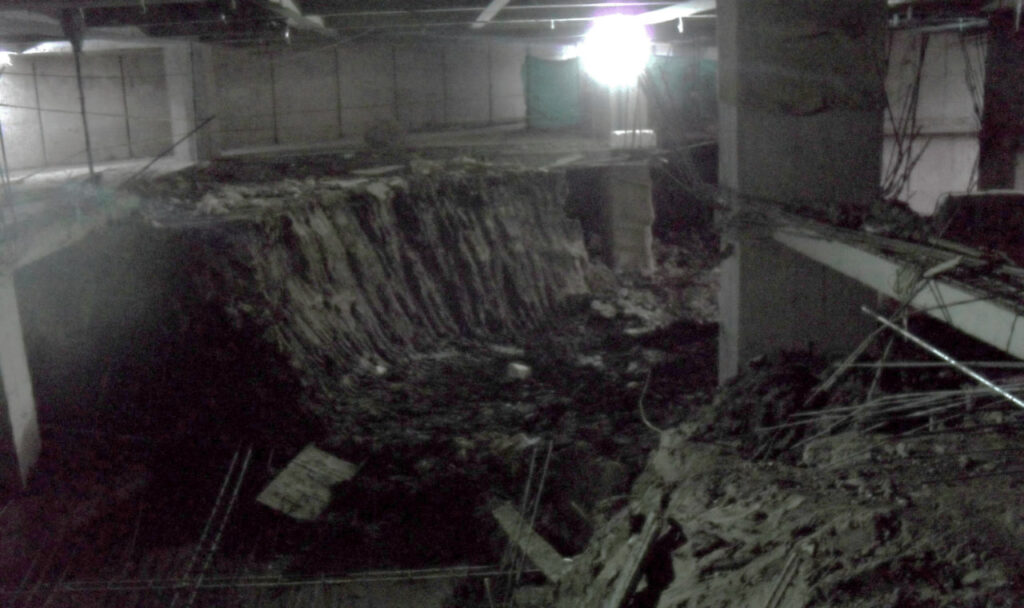
El sistema permite ganar tiempo de ejecución al realizar actividades de forma paralela y resulta más seguro desde el punto de vista geotécnico.
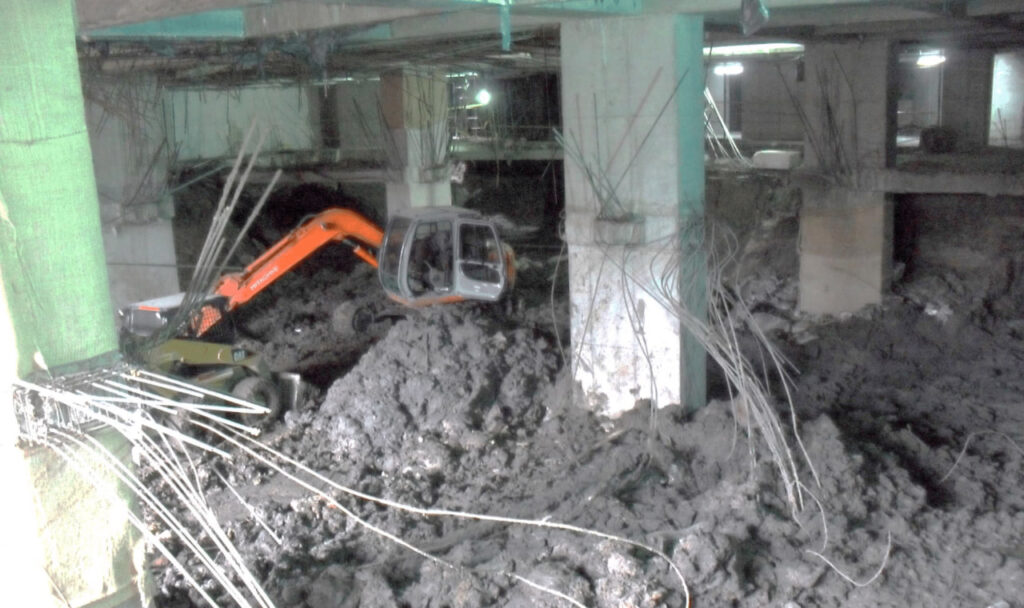
Puede verse aquí el alistado para fundida de un tramo de cimentación.
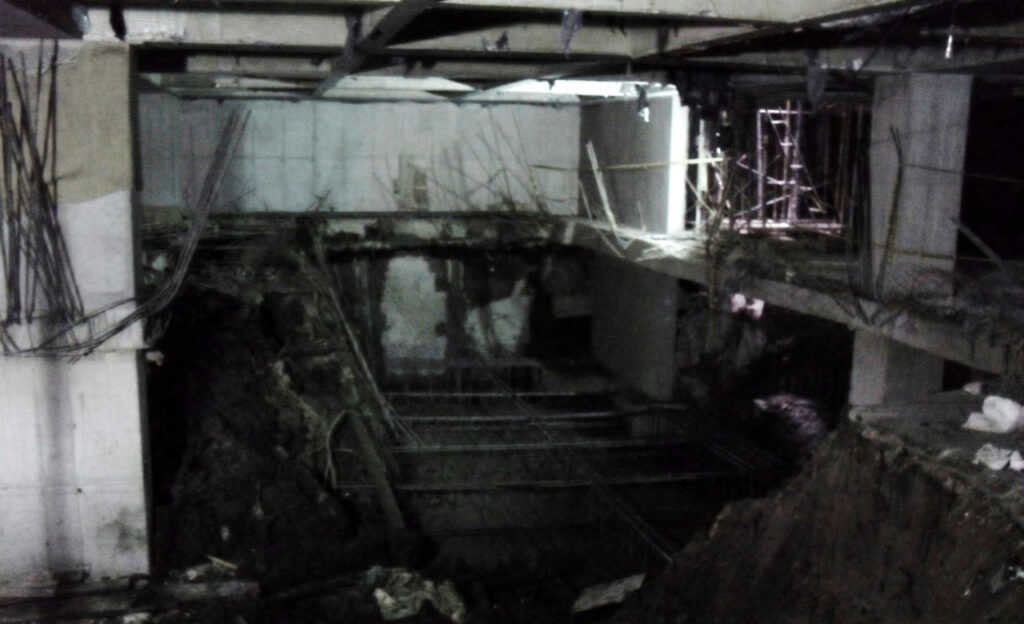
Es importante verificar la limpieza del acero y fundir concreto de limpieza previo amarre de acero.
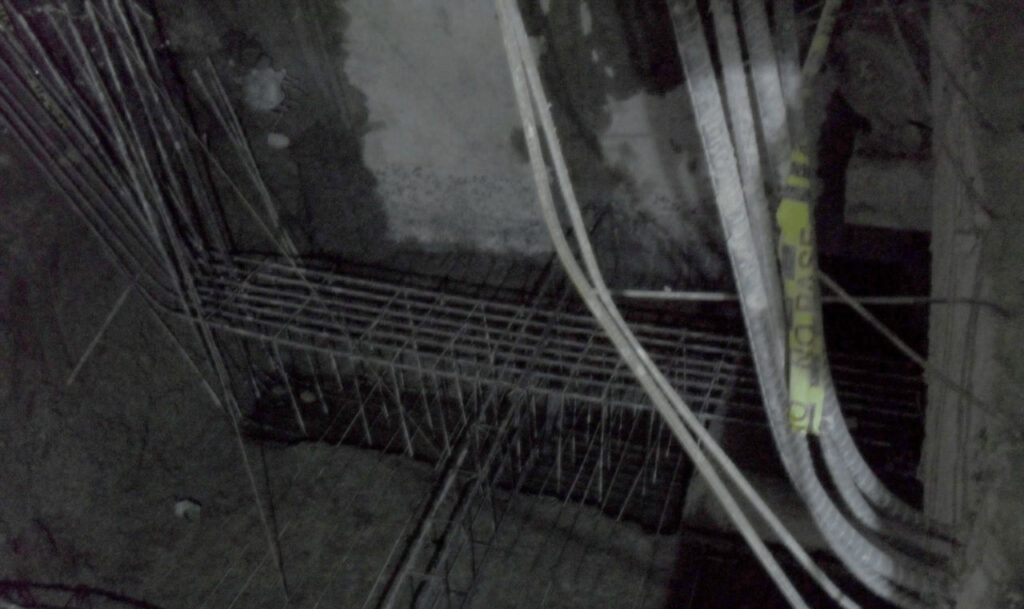
Armado, encofrado y fundida de vigas de cimentación (nótese que el acero de la placa de subpresión se amarra con el refuerzo superior de las vigas, trabajando en conjunto)
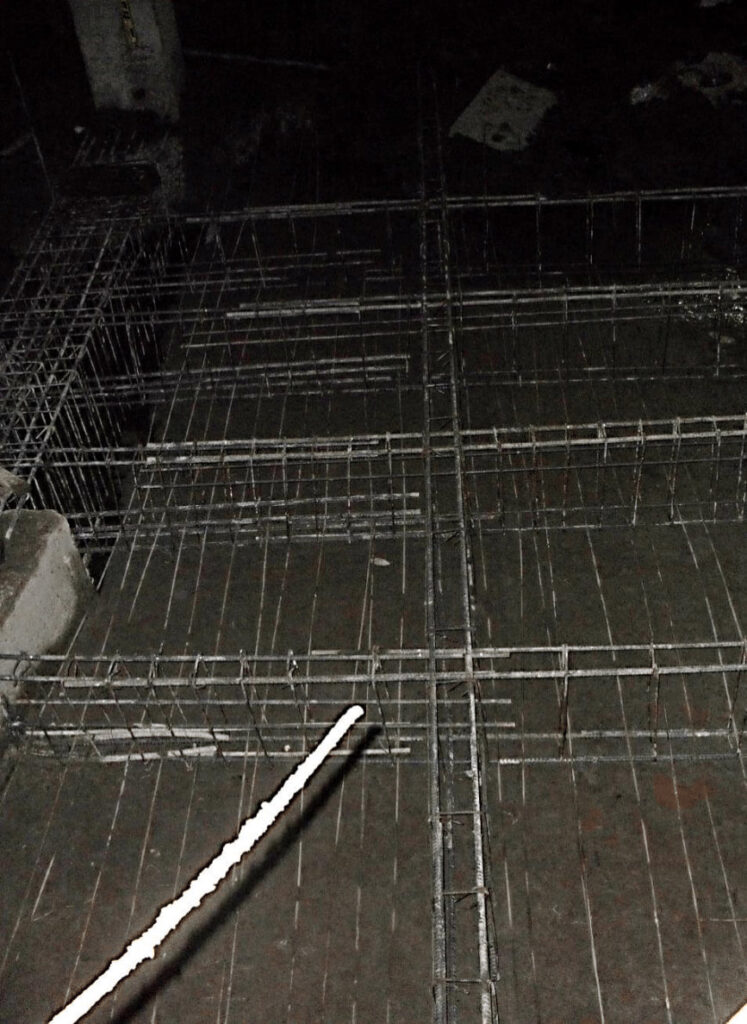
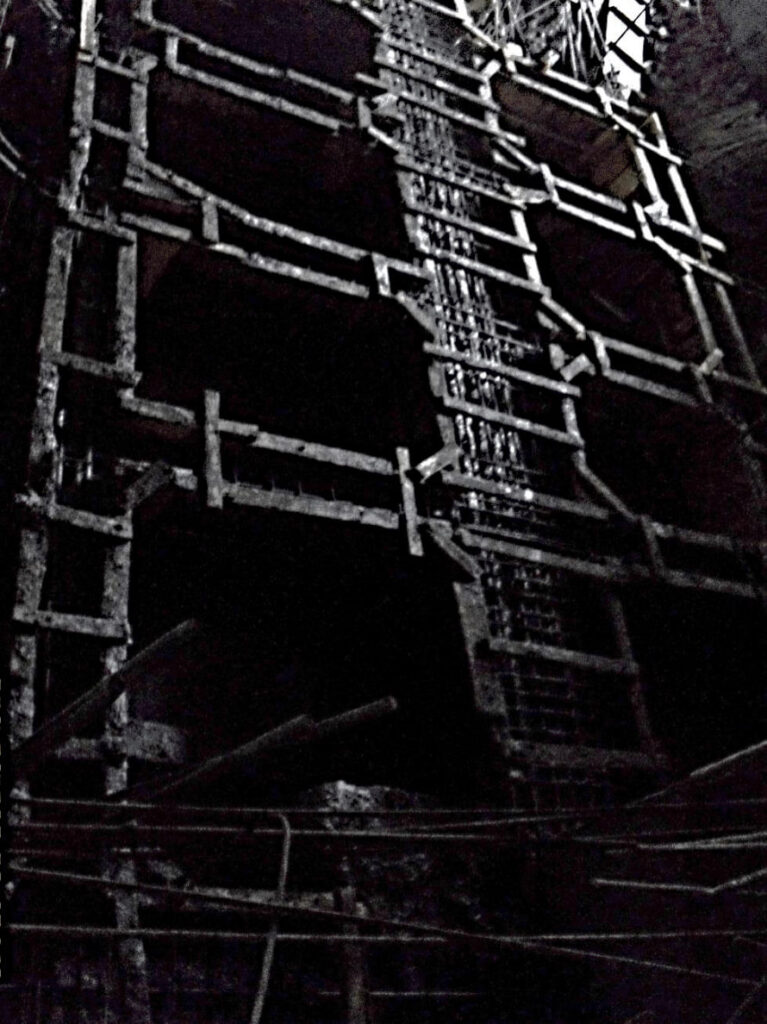
3. El sistema resulta bastante seguro, dado que los esfuerzos sobre las pantallas se ven compensados por la placa de sótano 2
4. Las excavaciones pueden realizarse al mismo tiempo que la superestructura, ahorrando tiempo y costos financieros.
Armado de la placa de sótano 2 y juego de columnas de sótano 2 a primer piso.
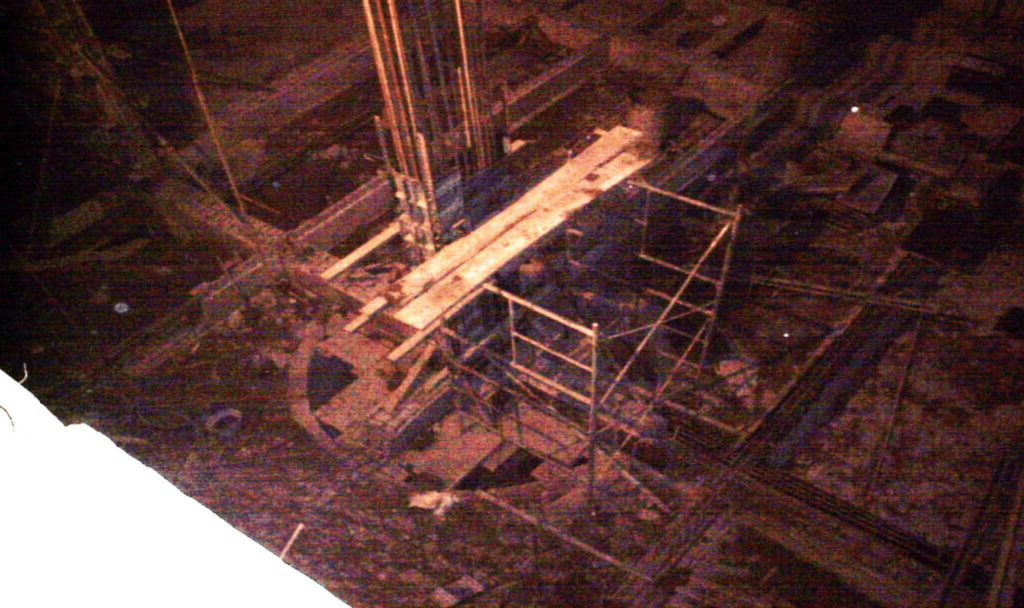
Descripción del Proceso Cerros de Suba
- Replanteo
- Organización en planta
- Señalización
- Excavación superficial
- Retiro de material excavación
- Acceso con molinete
- Excavación
- Perfilado
- Anillos en concreto
- Borde del último anillo
- Acero de refuerzo
- Embudo
- Fundida del Caisson
- Cota final de fundida
Descripción del Proceso Bosques del Márquez
- Avance ejecución
- Excavación por terrazas para avanzar simultáneamente en muro anclado e iniciar Caisson.
- Organización en planta
- Vista en planta
- Excavación con equipo mecánico
- Encofrado anillos
- Centro Caisson
- Armado encofrado
- Centrado encofrado
- Alistado para fundir
- Anillo fundido
- Avance excavaciones
- Imprevistos climáticos
- Campana o pata de elefante
- Izado de armadura con torre grúa
- Acero de refuerzo
- Fundida Caisson
- Vibrado de concreto
- Lavado acero de refuerzo
Cisson gran diámetro
Proyectos realizados
1. Excavación y replanteo Caisson gran diámetro
2. Caisson de 5 M de diámetro – Universidad de Los Andes
3. Caisson huecos rellenos de material granular compacto de 7.5 M de profundidad y diámetro de 2.6 M – Fabrica Nacional de Chocolates en la ciudad de Medellín.
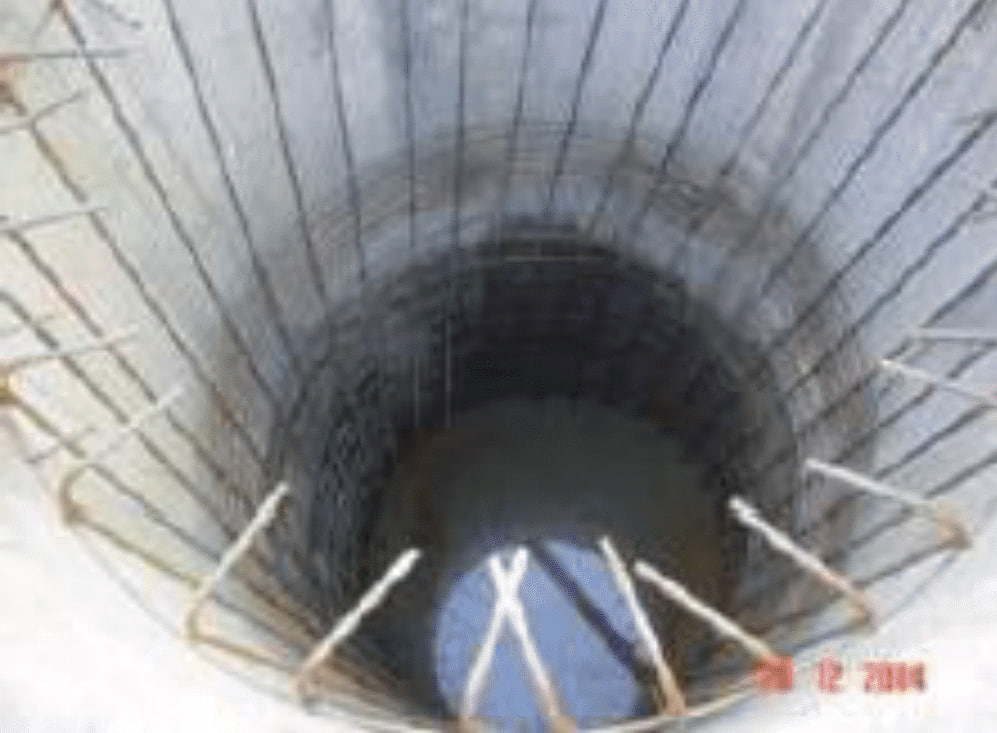
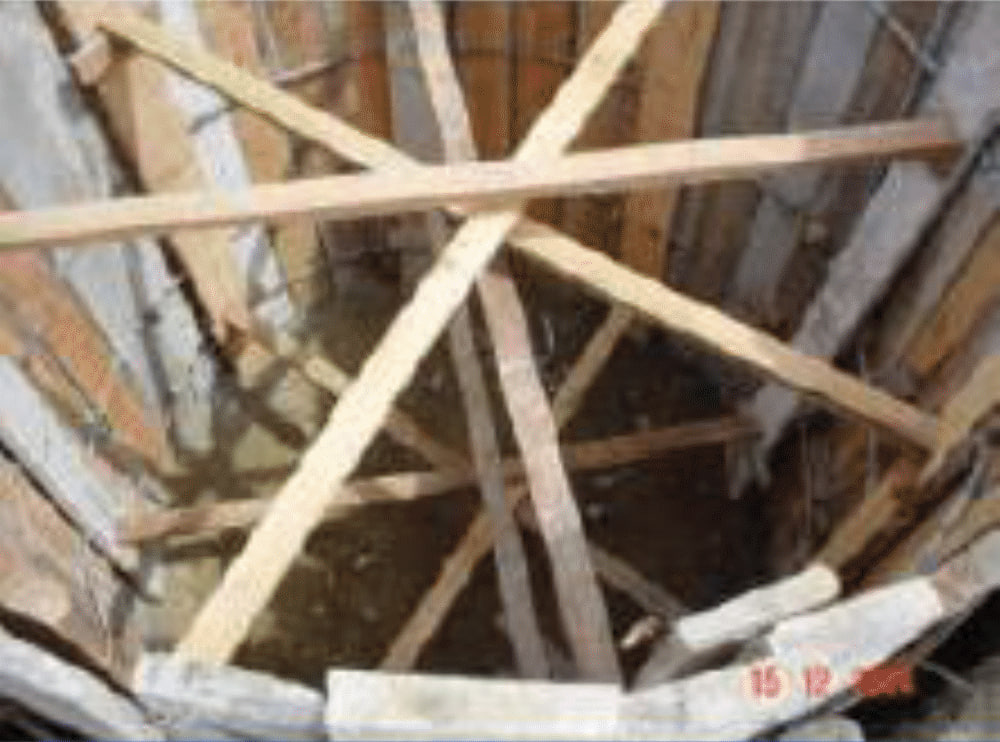
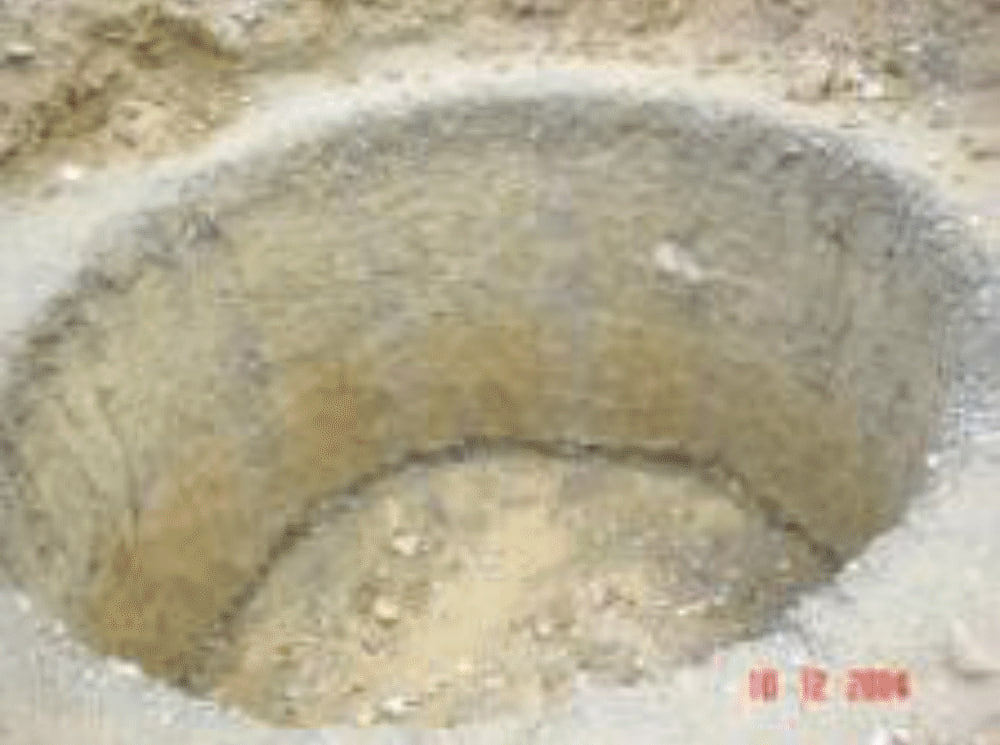
Particularidades para vivienda Sopó:
- Dado que la mitad de la cimentación se encuentra en un relleno realizado en malas condiciones de compactación y ubicadas sobre la ladera, se descarta el uso de pilotes ya que el pilotador no puede garantizar el debido empotramiento que se requiere
- La recomendación de cimiento con Caisson es coincidente entre geotecnista y estructural, por tanto el constructor deberá acatar la recomendación, y caso contrario asumirá las responsabilidades pertinentes.