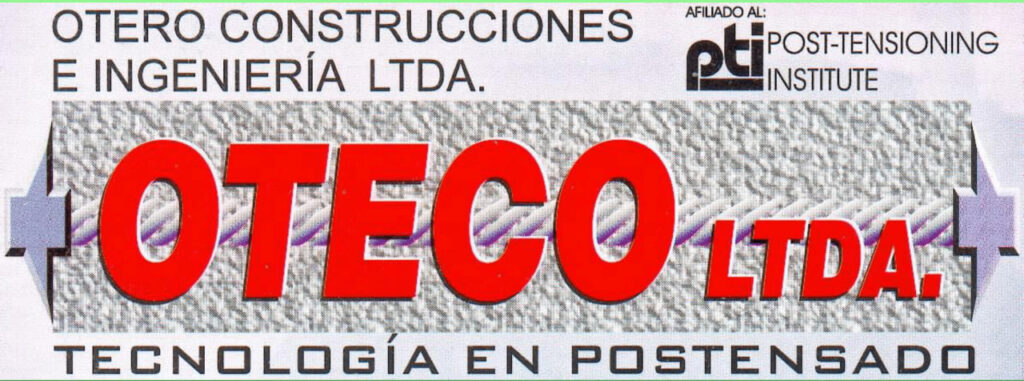
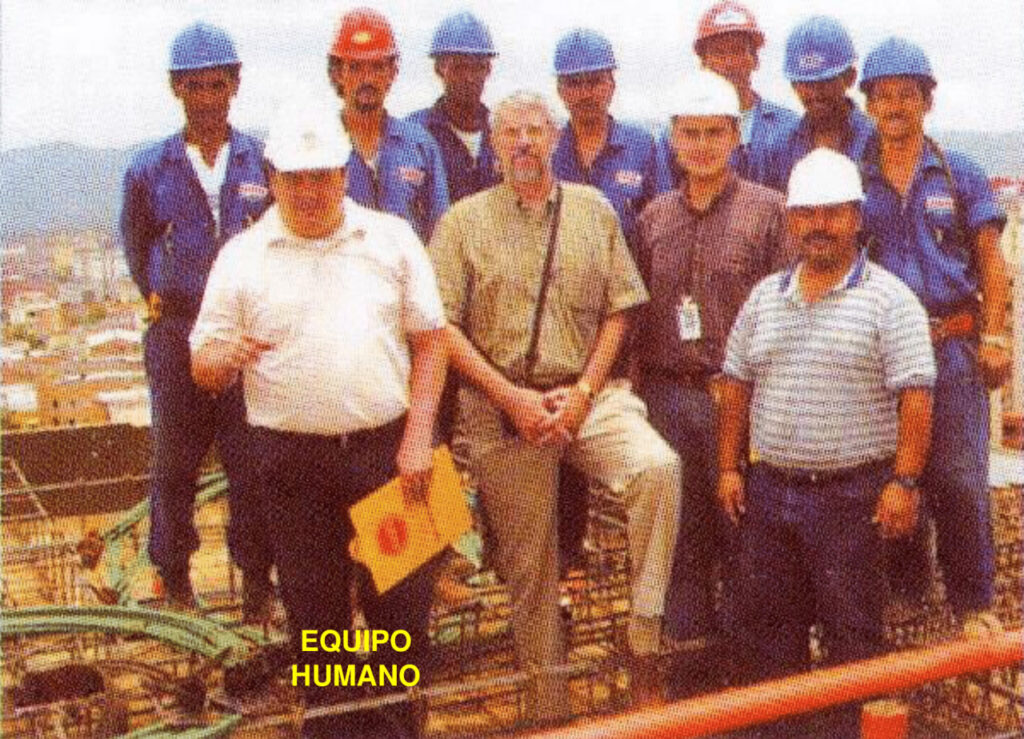
PLACAS POSTENSADAS EDIFICIO CALLE 100 CON AVENIDA 19
Santa Fe de Bogotá
Descripción del proceso
- Izado materiales
- Amarre acero, vigas y viguetas
- Detalles encofrado
- Vista general de la placa
- Distanciadores
- Líneas de vida
- Salva vidas
- Alistado torones y anclajes
- Anclajes
- Anclajes activos
- Instalación de los torones
- Alturas y trayectoria de los cables
- Anclajes pasivos
- Anclajes activos y pasivos
- Vista general de las vigas antes de fundir
- Nudo estructural
- Colocación del concreto por métodos tradicionales
- Desencofrado
- Gato para el tensado
- Tensado
- Medida de elongación
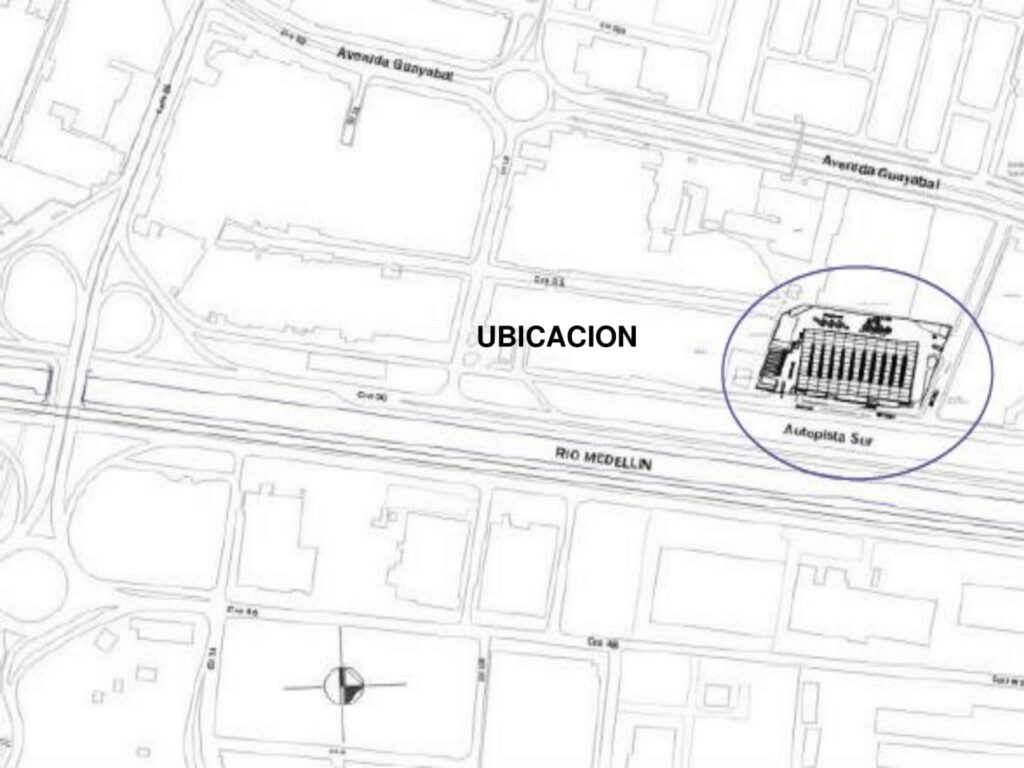
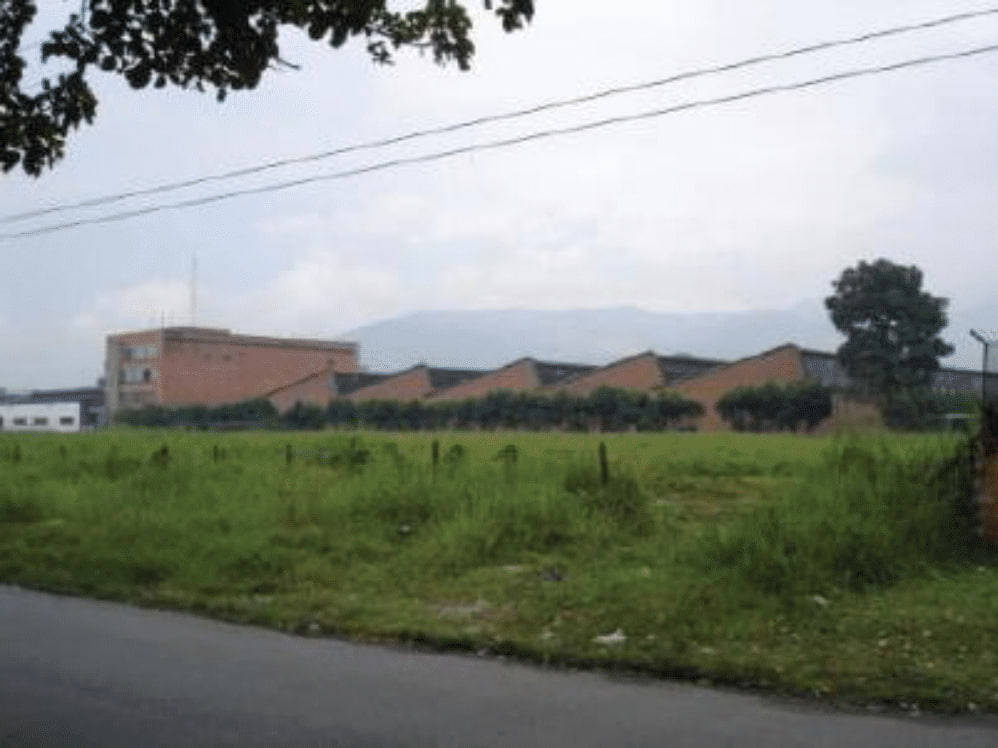
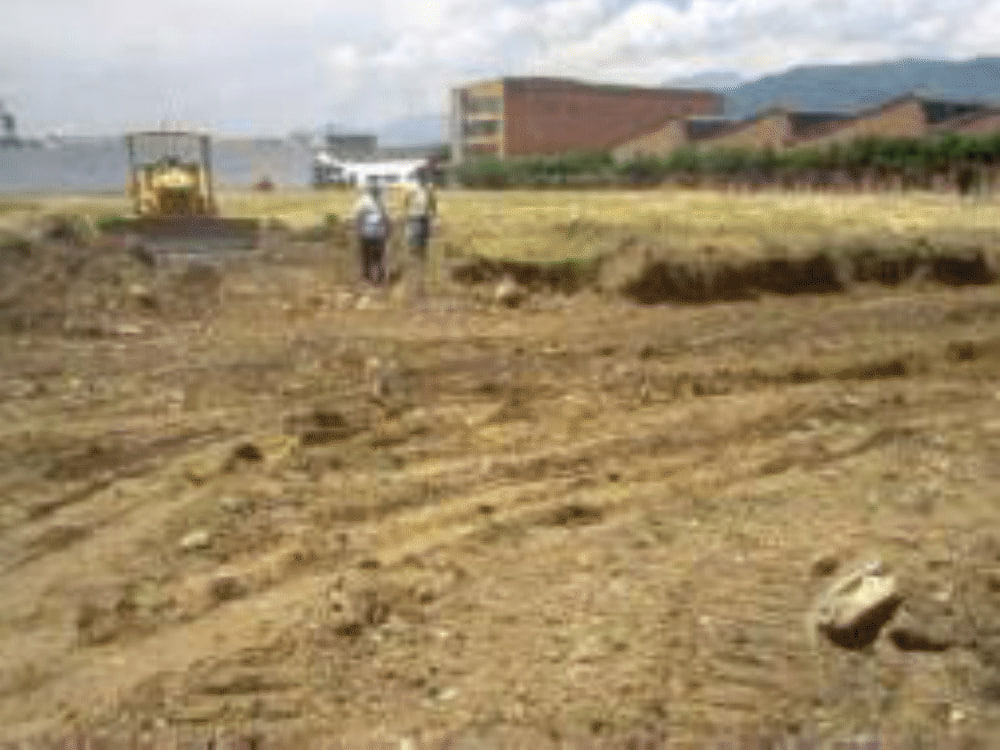
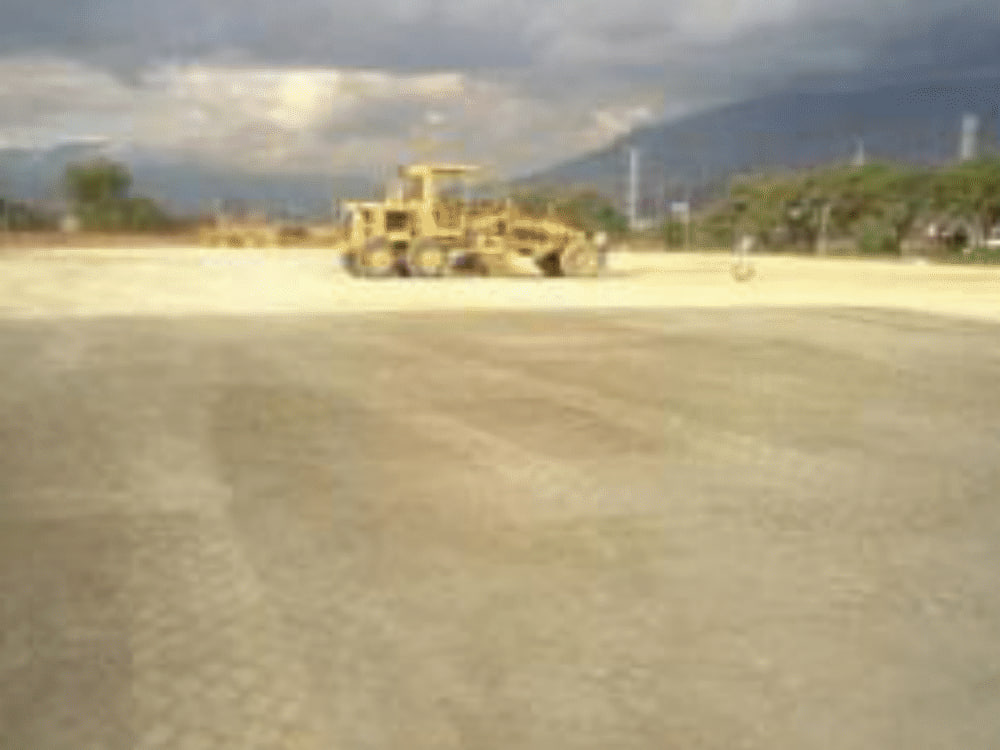
o Vista general del lote
o Excavación y rellenos en material granular compactado
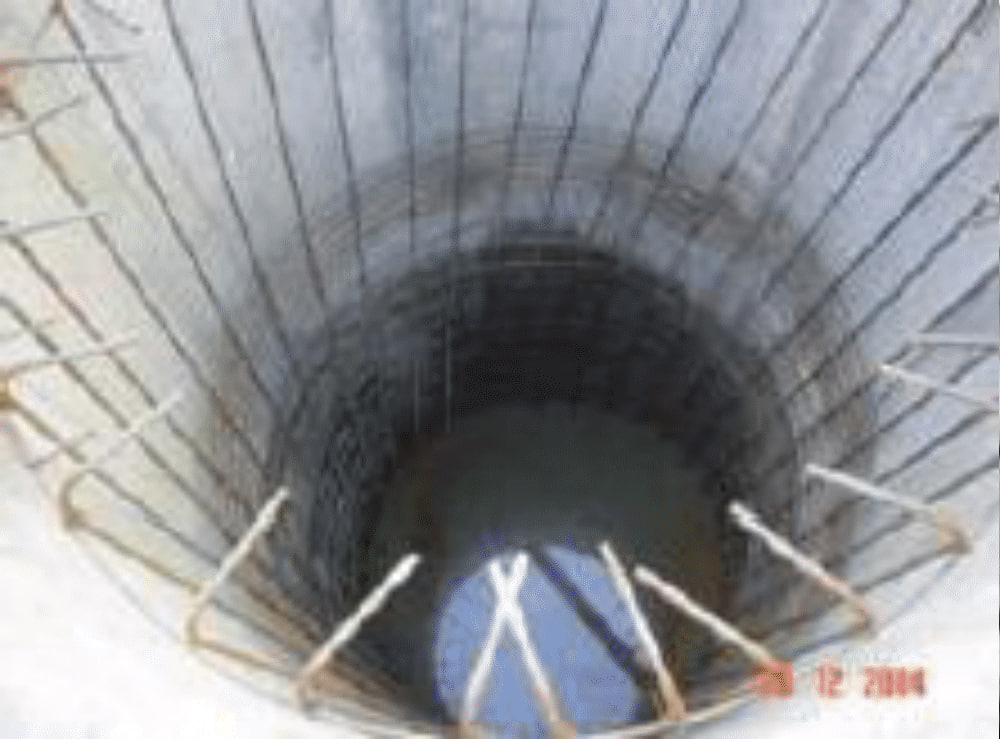
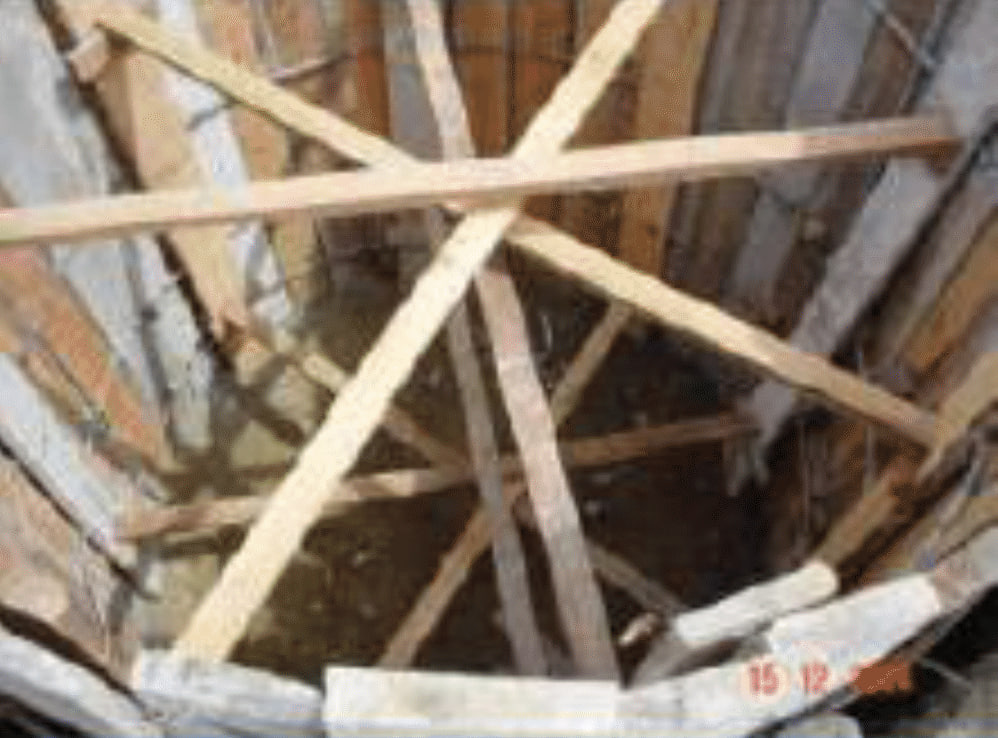
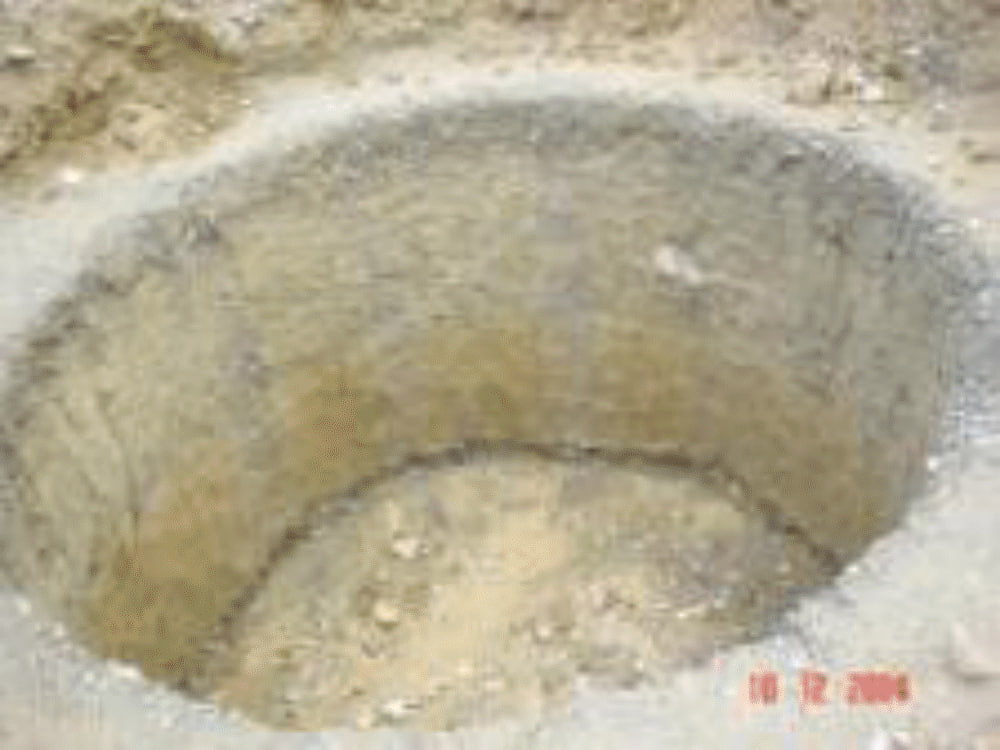
o Caisson huecos rellenos de material granular compacto de 7.5 M de profundidad y diámetro de 2.6 M.
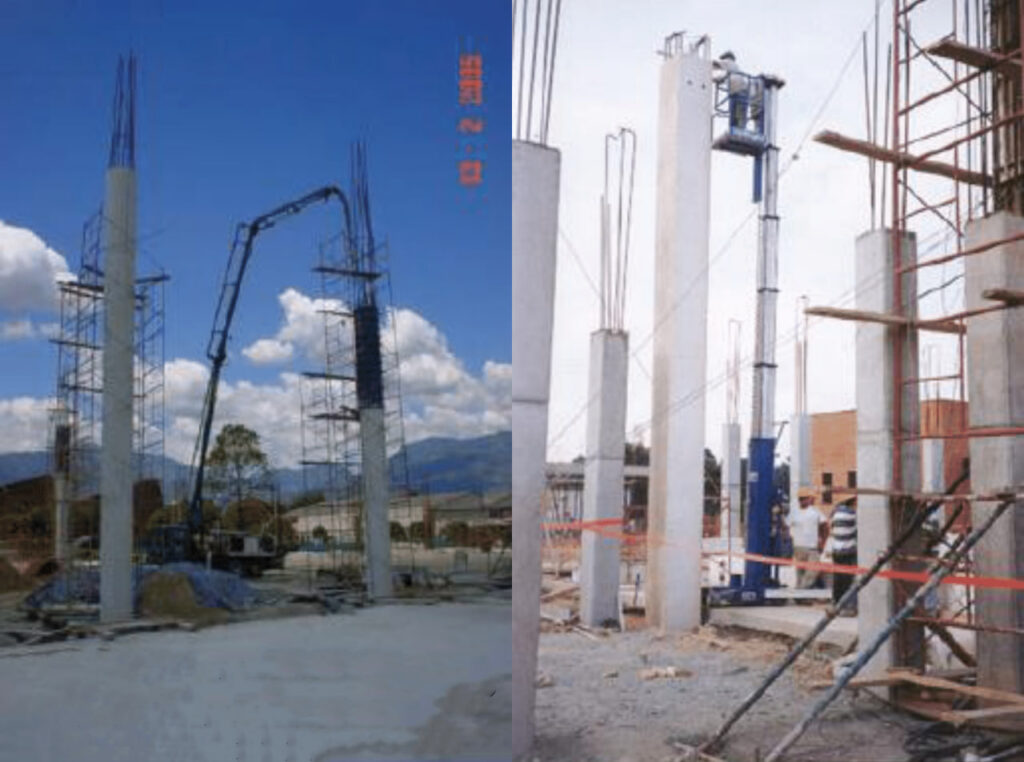
o Columnas en concreto blanco de 0.9 M de diámetro y alturas de 9.96 y 12.06 M fundidas en tramos de 3.2 M.
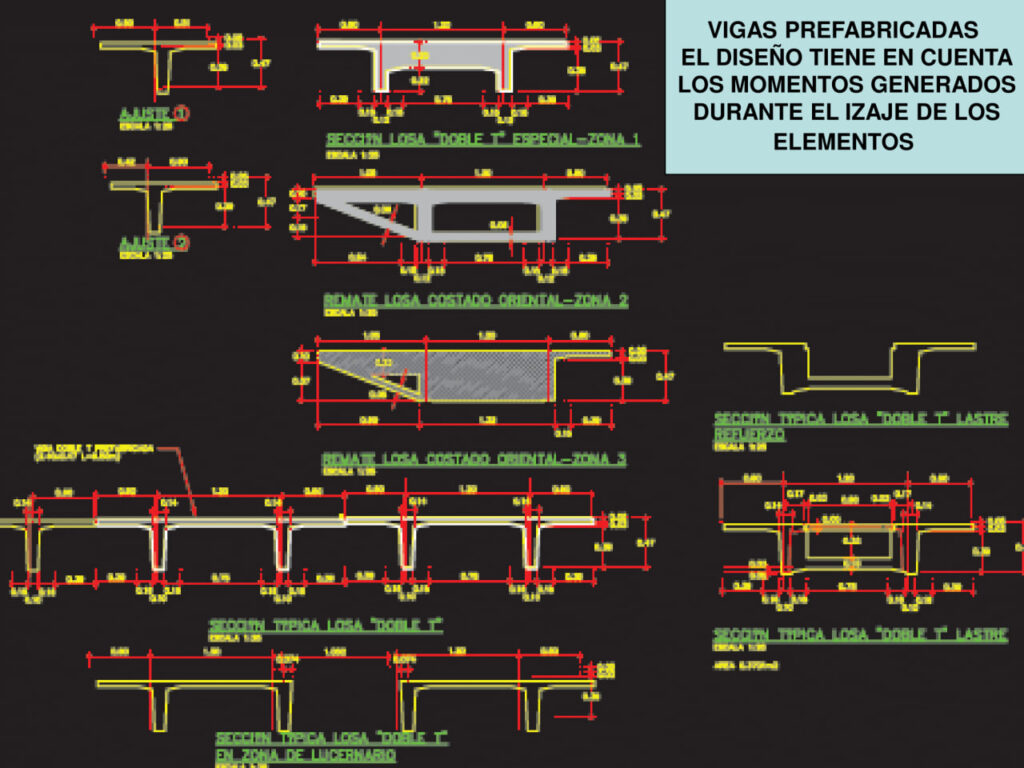
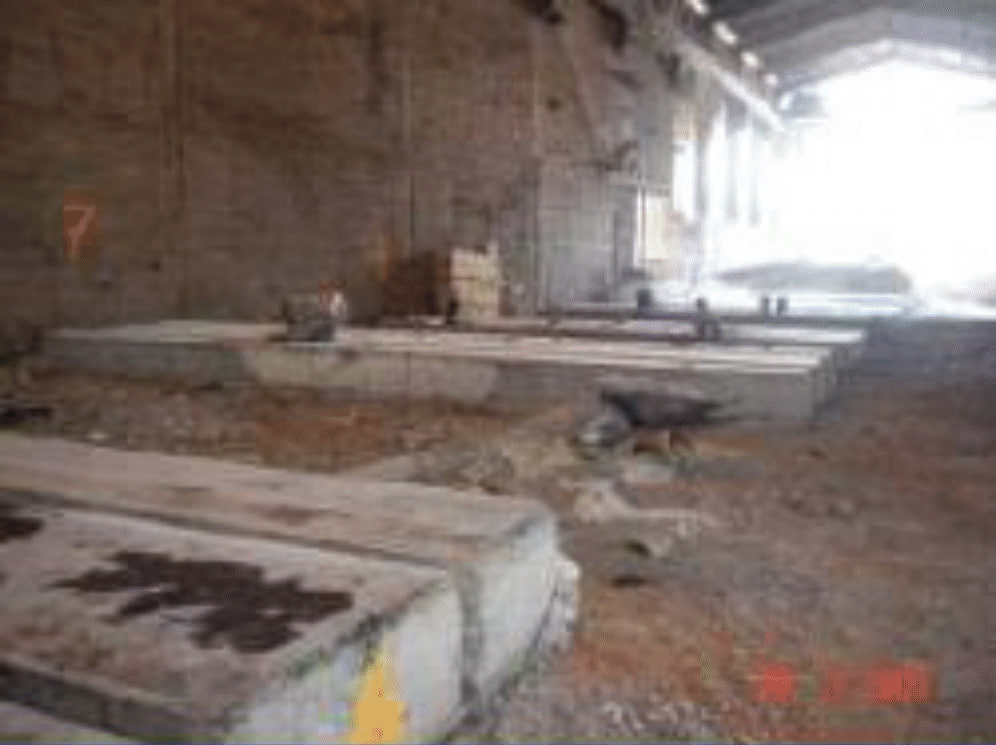
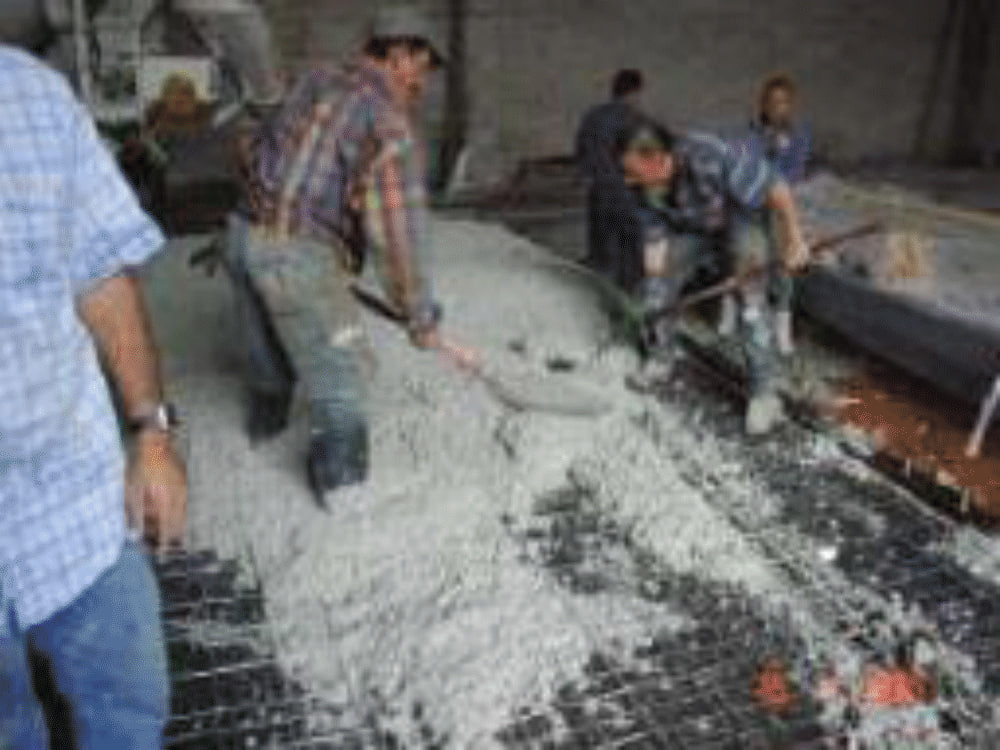
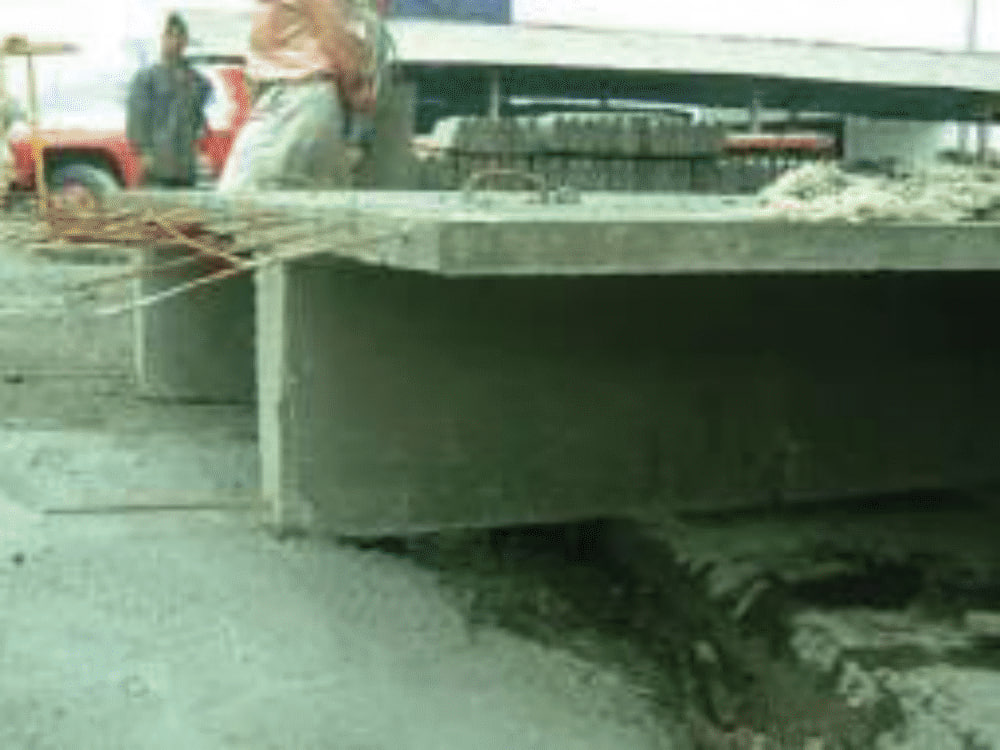
o Las vigas T y doble T se prefabricaron en concreto blanco de 3000 PSI para lo cual fue necesario montar una planta de producción de concretos.
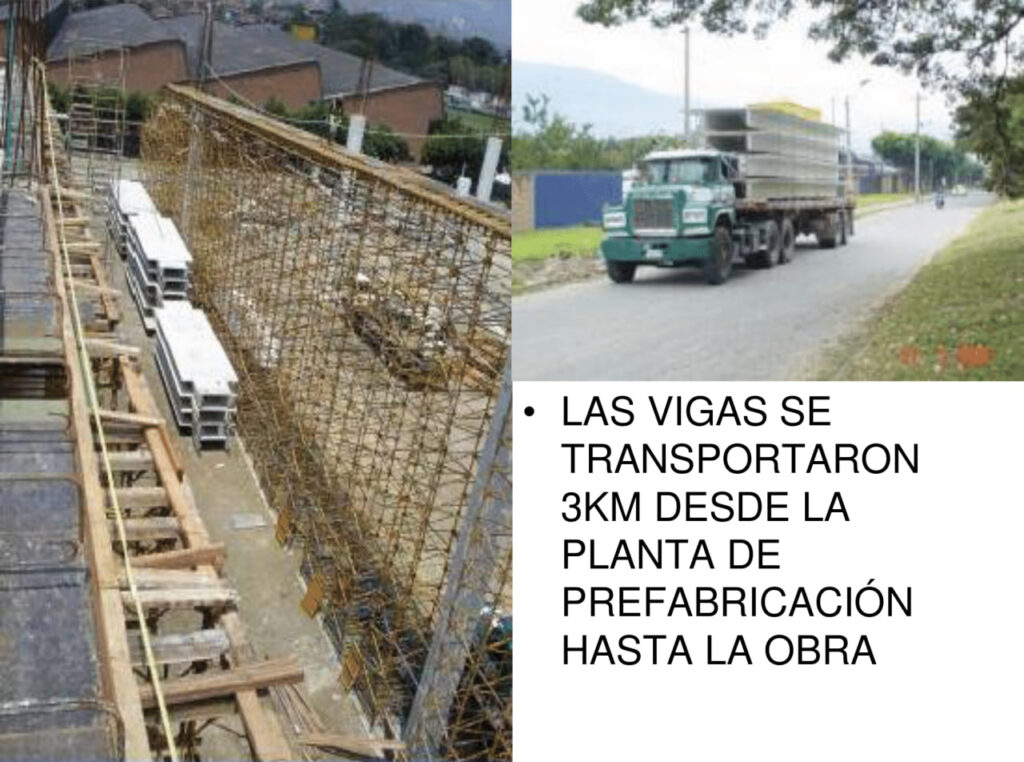
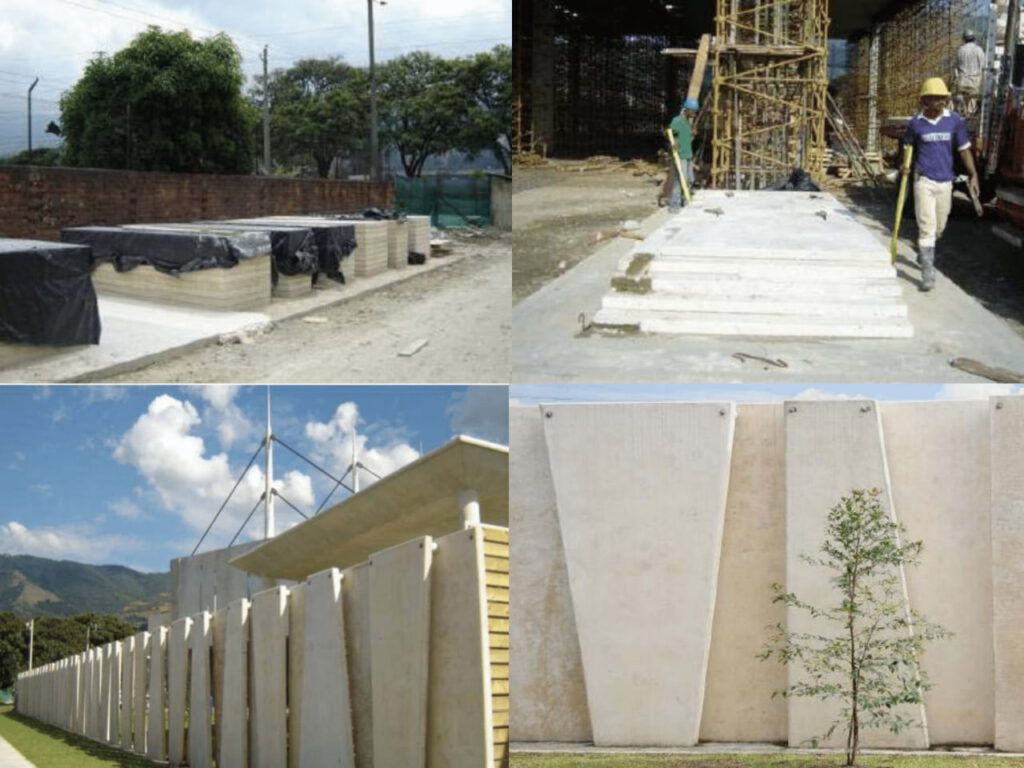
VISTA GENERAL DE LA OBRA FALSA PARA EL MONTAJE DE LOS PREFABRICADOS Y LA FUNDIDA DE LAS VIGAS DE AMARRE
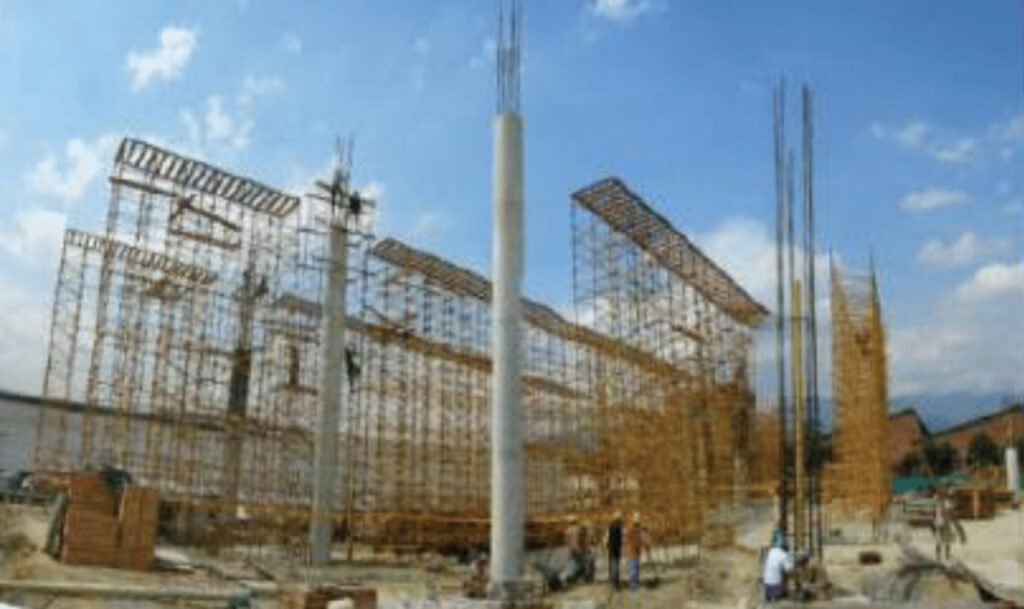
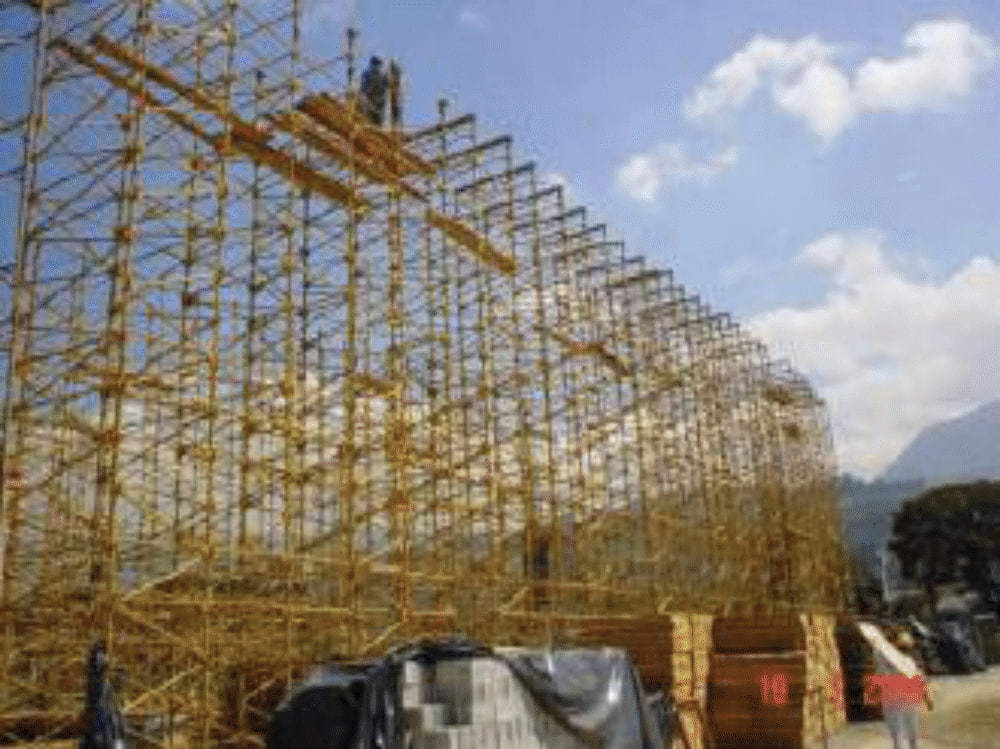
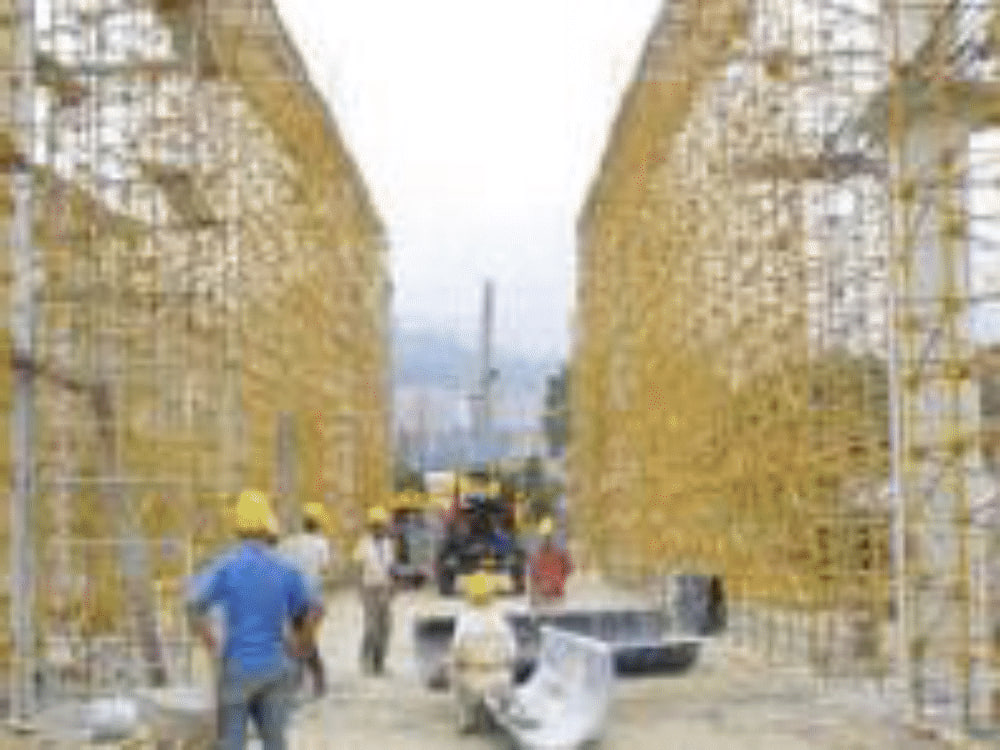
o La obra falsa debe alcanzar 12 M y resistir además de la carga muerta de la viga de amarre, los posibles movimientos de empuje durante el izaje de las vigas.
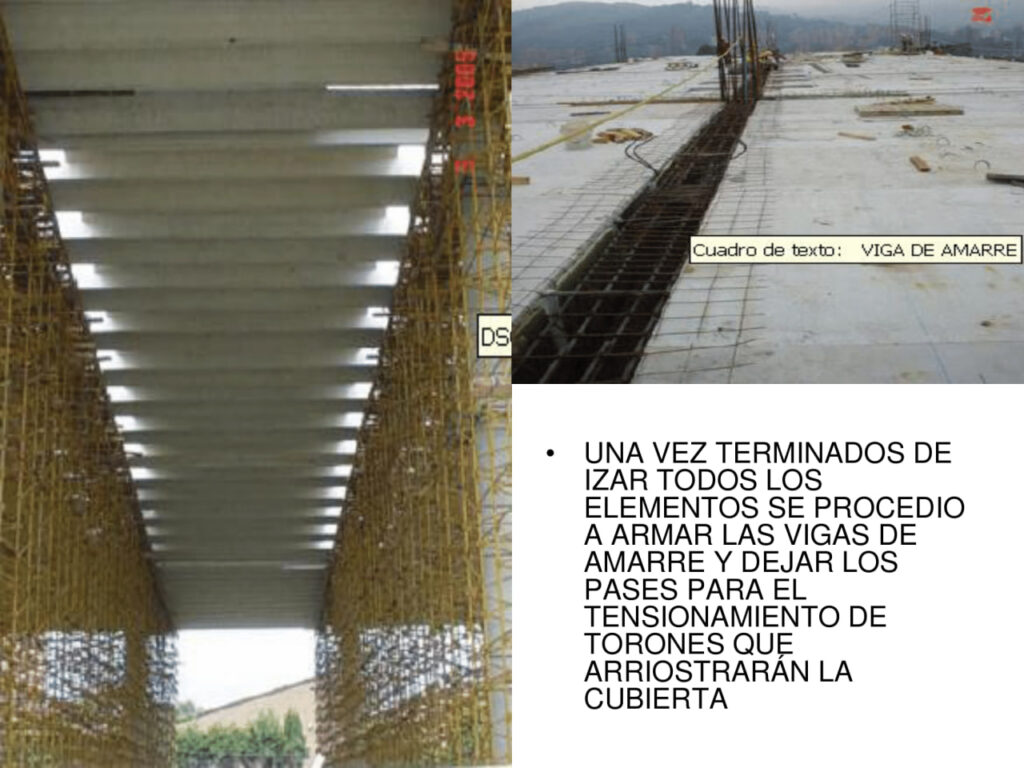
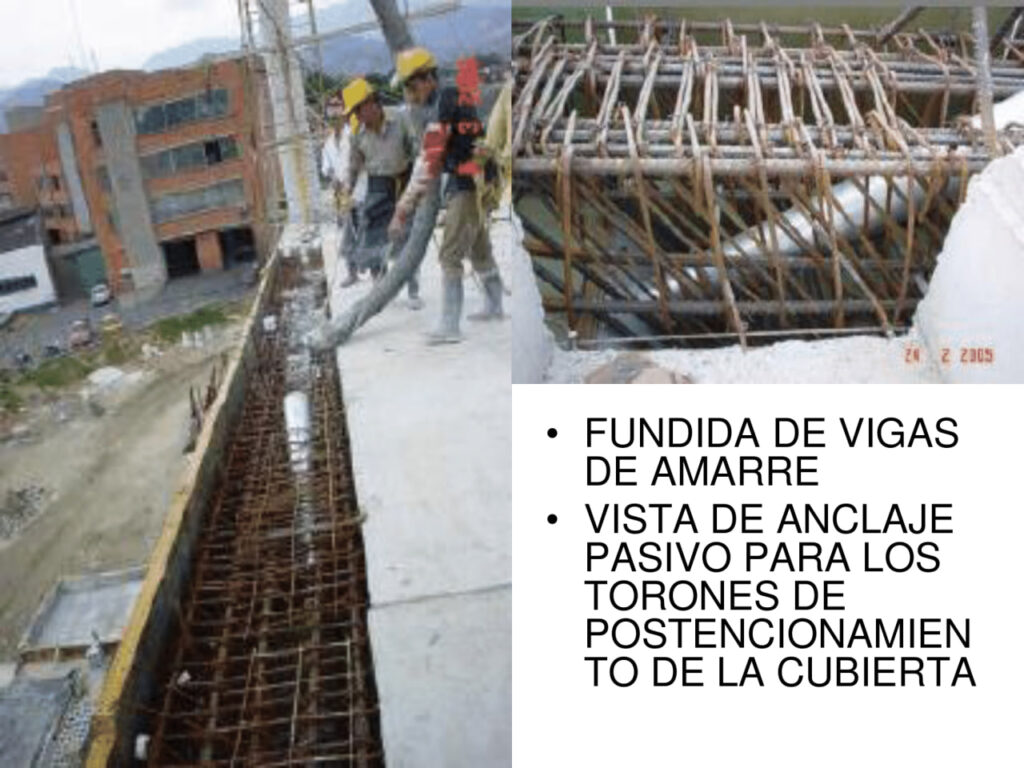
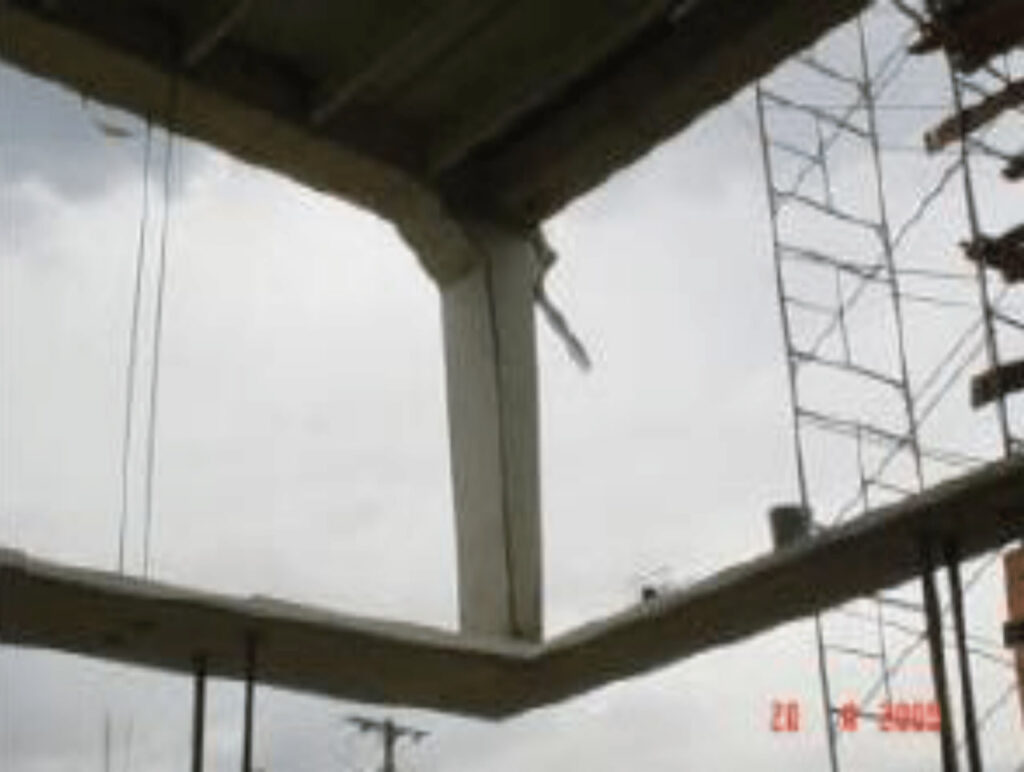
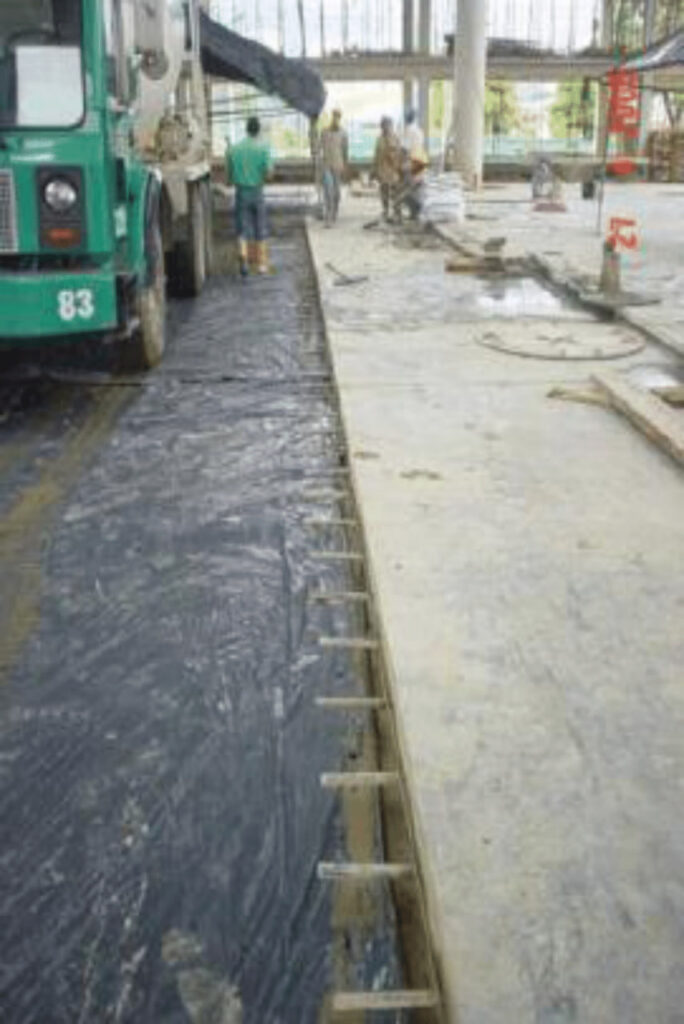
PISOS EN CONCRETO
o La superficie del proyecto consta de 12500 m2 aproximadamente, todos en piso de concreto.
o 2500 m3 de concreto gris
o Concreto con cemento tipo I, agregado de 11/2 y modulo de rotura 43 en bodega y 39 en sótano
o Pisos para tráfico alto con endurecedor
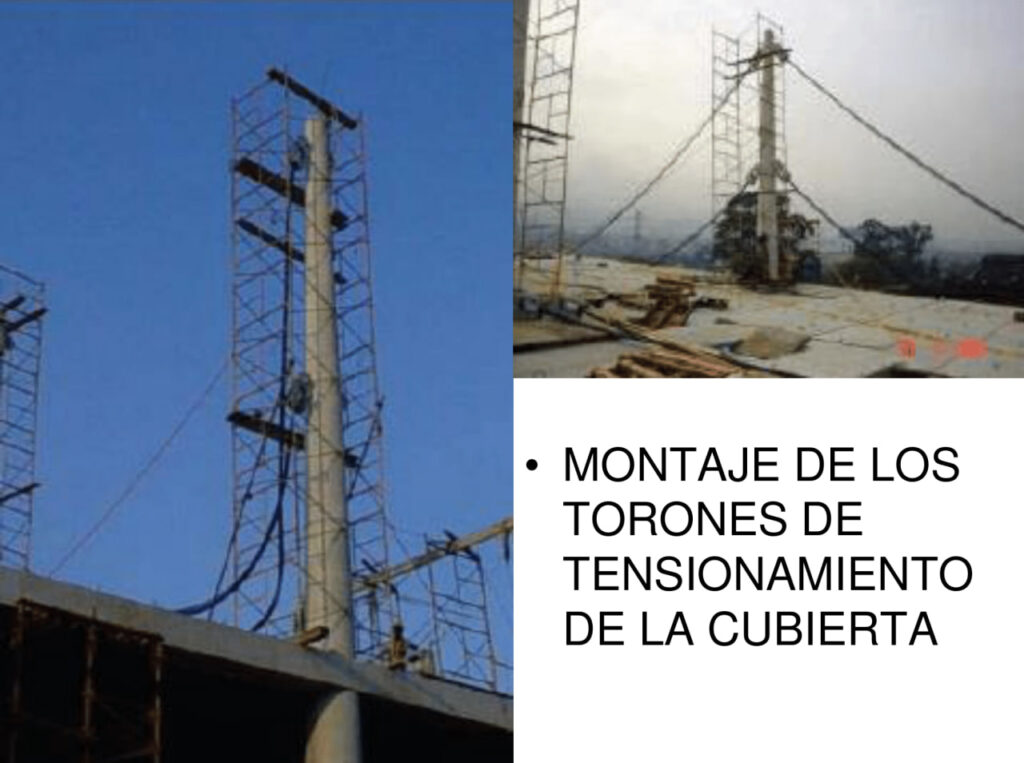
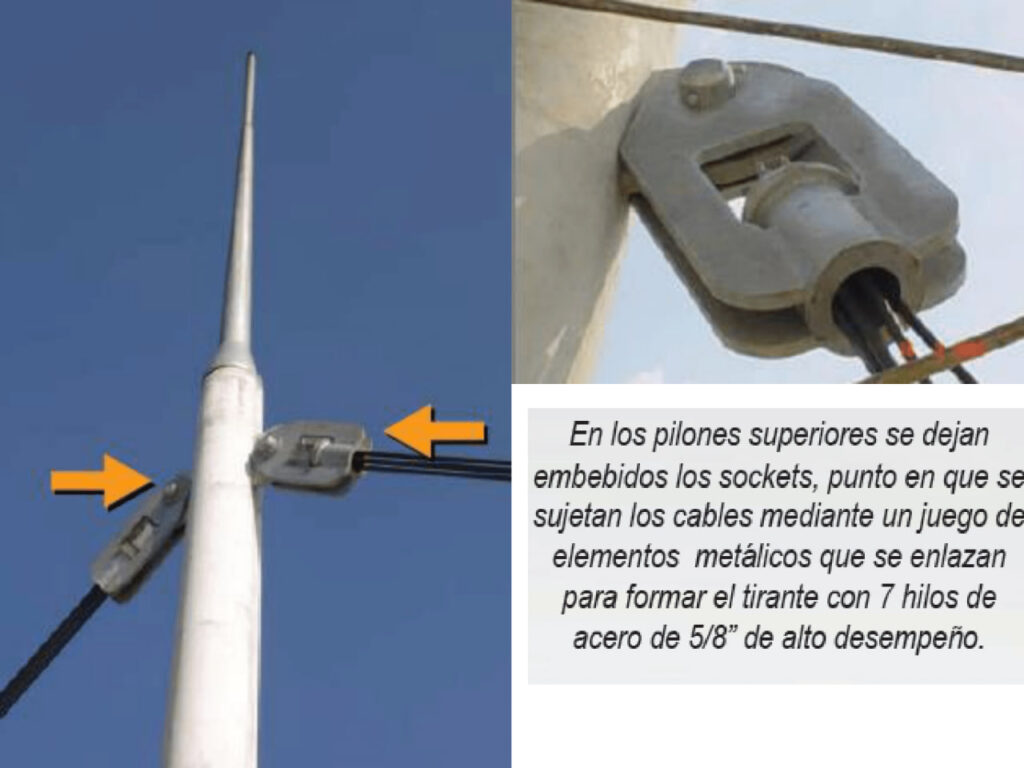
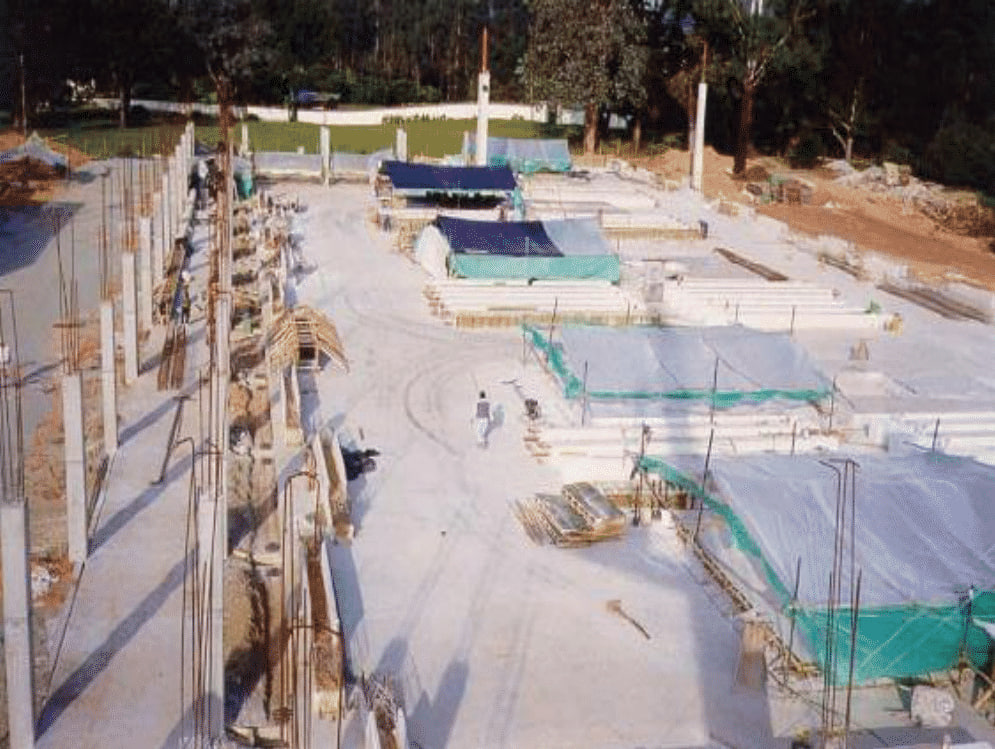
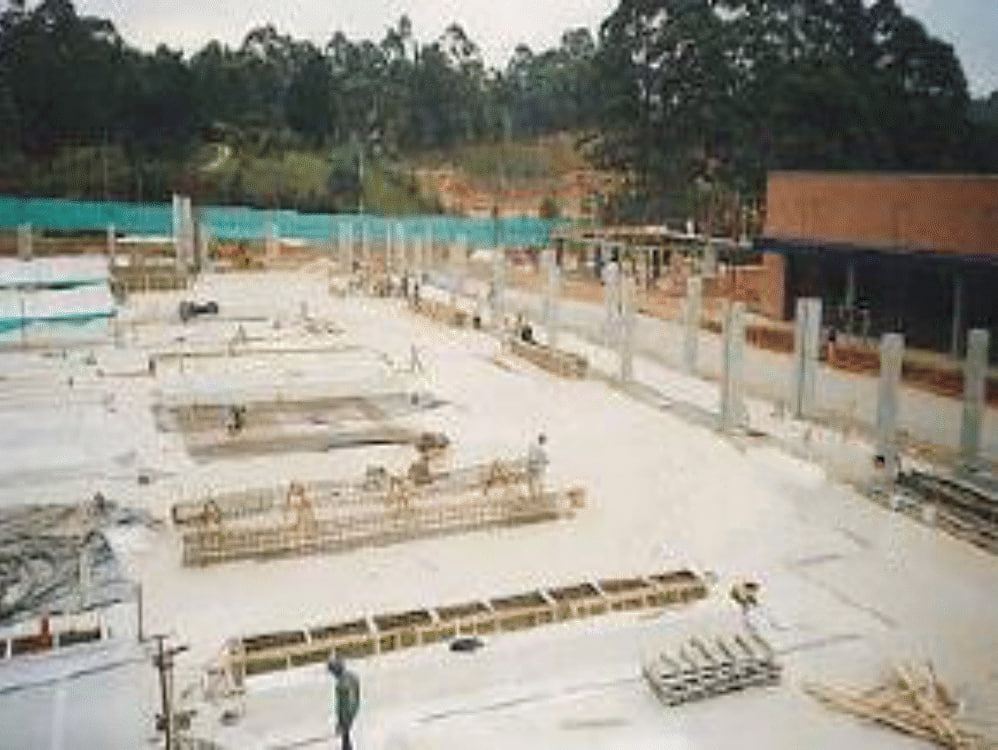
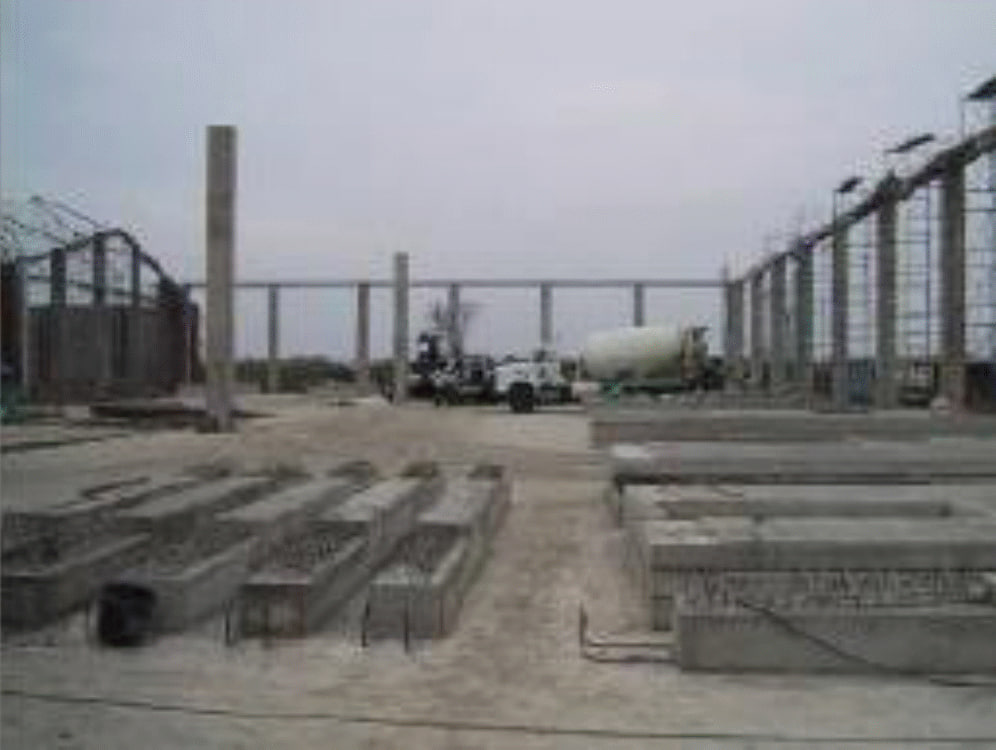
o Durante el proceso de diseño deben tenerse en cuenta los esfuerzos a tracción que se generan en el izado y transporte de los paneles.
o La producción de estos elementos pretensados debe ser realizada con equipos adecuados y diseñados específicamente para este fin, en bancos de pretensado de línea larga, usando para la conformación de la placa máquinas extrusoras o moldeadoras. El ancho nominal estándar es de 1.200 mm y el rango de espesores puede variar entre 80 y 300 mm, siendo posible la fabricación de hasta 500 mm. Los aligeramientos o alvéolos varían en forma, tamaño y número dependiendo del equipo usado en su manufactura.
o Los bancos de prefabricación varían entre 100 y 200 m de longitud. Los fondos de las camas pueden ser de diversos materiales, aunque se recomienda que sean de acero para mejorar el acabado de la parte inferior de la placa e incorporar sistemas de curado con calor que aceleren el proceso de endurecimiento del concreto. Posteriormente las placas son cortadas de acuerdo con la modulación especifica de cada proyecto.
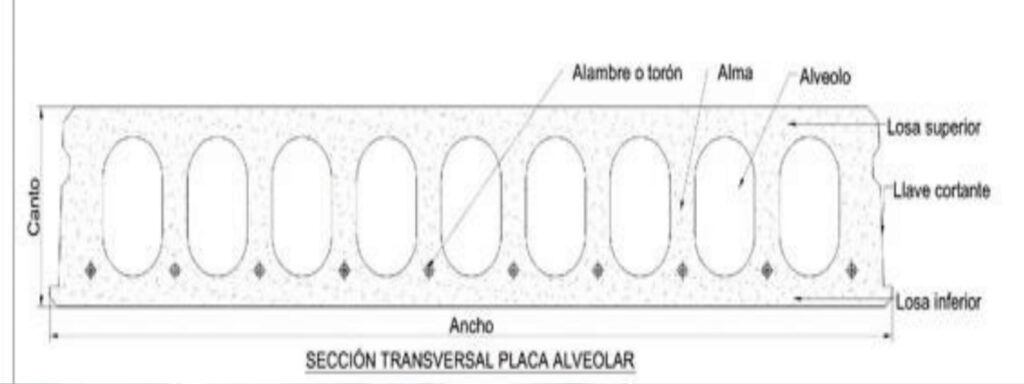
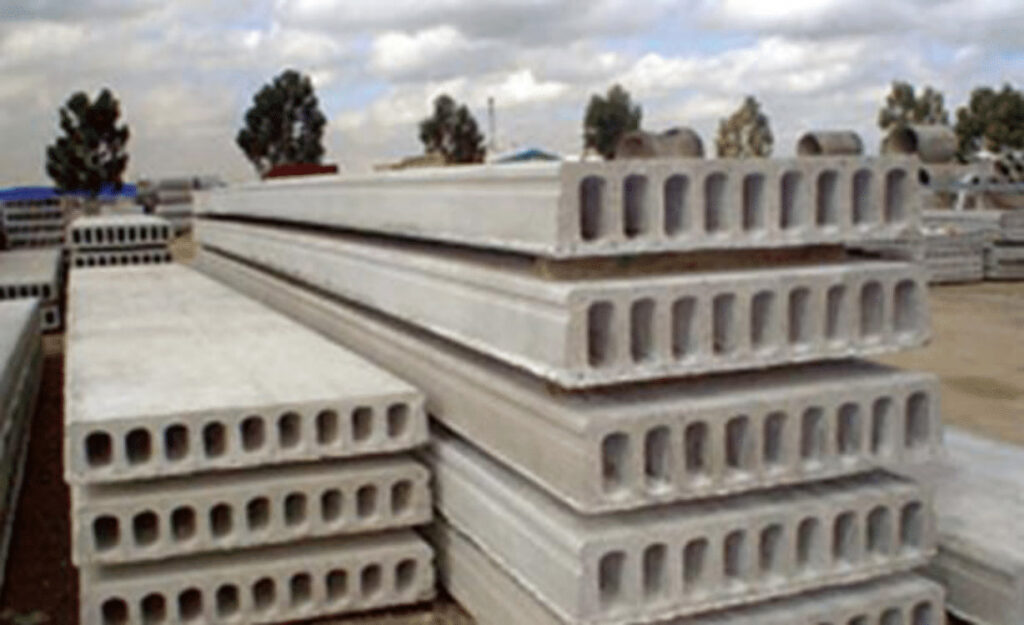
SECCIÓN TRANSVERSAL
FABRICACIÓN
o El proceso productivo de las placas alveolares inicia con la preparación de la pista (línea de producción sobre la cual se funden las placas). Esta se limpia y se le aplica un desencofrante que evita que se le adhiera el concreto; luego se procede a la extensión de los alambres o torones definidos en diseño entre bancadas (extremos de la pista) donde son anclados pasivamente mediante piezas especiales con cuñas; se cortan los alambres o torones y se sujetan al gato hidráulico que tira de ellos traccionándolos hasta la tensión de diseño y se acuñan en la cabeza de anclaje activo, que forma parte de la bancada correspondiente. La bancada desde la cual se traccionan las armaduras recibe el nombre de “activa”, mientras que la opuesta es la “bancada pasiva”, ambas vinculadas a través de la losa de compresión que completa la infraestructura resistente de cada pista de producción.
o Una vez que las armaduras se encuentran pretensadas entre ambas bancadas, se sitúa la máquina moldeadora sobre los carriles de la pista. Al tiempo que la máquina avanza, asegura la posición de la armadura mediante el “guía – hilos” situado en su parte delantera, y va depositando el concreto con la forma y dimensiones que corresponda a la placa alveolar que se esté fabricando.
o La mezcla de concreto debe tener una consistencia muy seca, de modo que mantenga la forma y dimensiones definidas, por lo que debe ser enérgicamente vibrado por la máquina para que envuelva perfectamente los refuerzos y rellene totalmente los moldes deslizantes.
o Terminada esta fase, se cubre la pista con una lona para retener la humedad y evitar cambios bruscos de temperatura durante el proceso de curado del concreto. Una vez se alcanza la resistencia requerida (entre 10 y 12 horas para pistas con calefacción y entre 36 y 48 horas a temperatura ambiente), se procede a distensionar los alambres o torones de refuerzo.
o Posteriormente, las placas alveolares son cortadas a la medida – de acuerdo con la modulación particular de cada proyecto – mediante máquinas cortadoras equipadas con un disco diamantado.
o Finalizado el corte y la marca, las placas se extraen y se trasladan al patio para almacenamiento y posterior despacho.
o Para asegurar la calidad del producto debe elaborarse un plan de ensayos sobre los materiales utilizados en el concreto y acero de refuerzo. Igualmente, a las placas alveolares terminadas se les debe hacer pruebas de resistencia a flexión, cortante y deformación bajo carga.
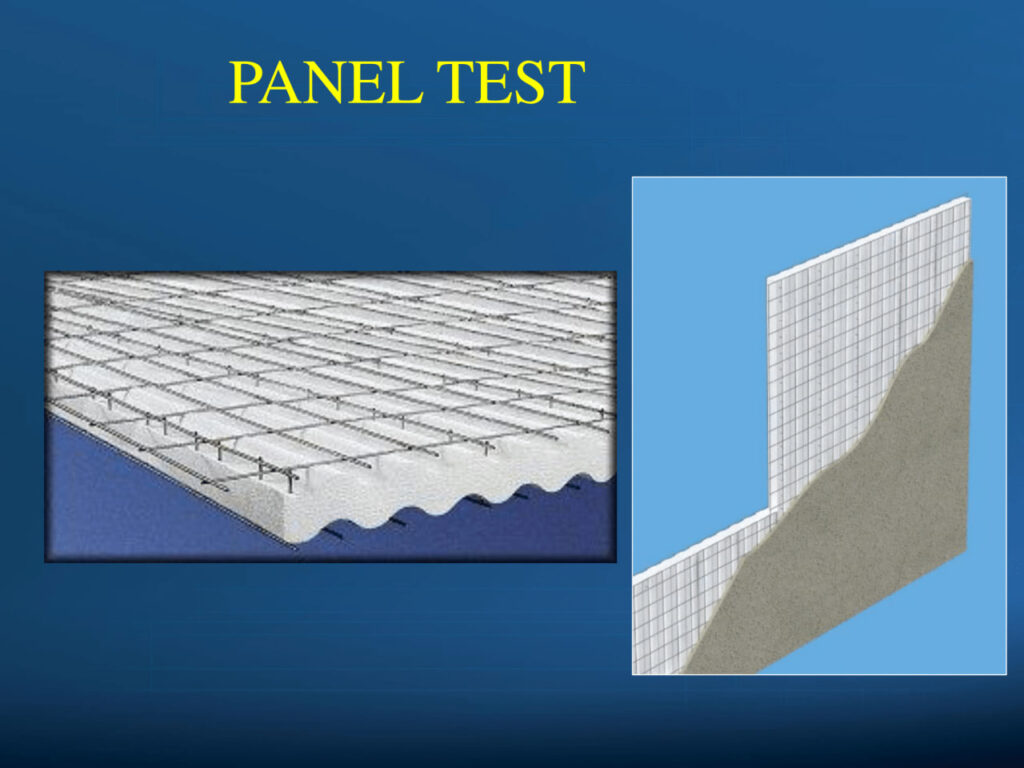
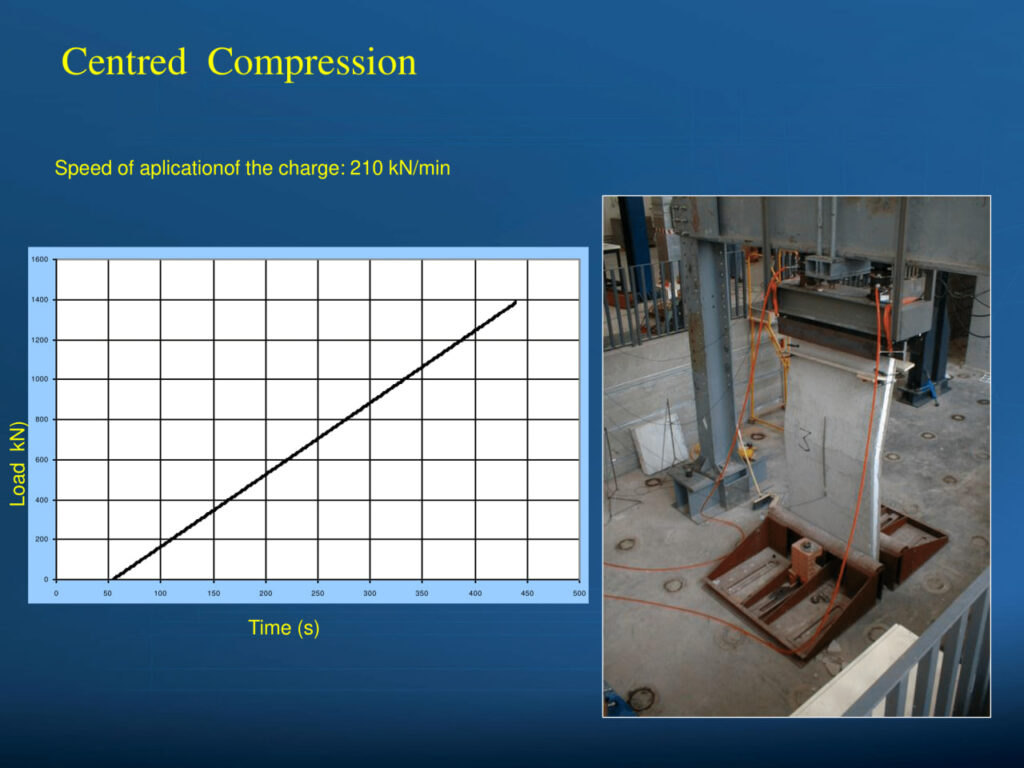
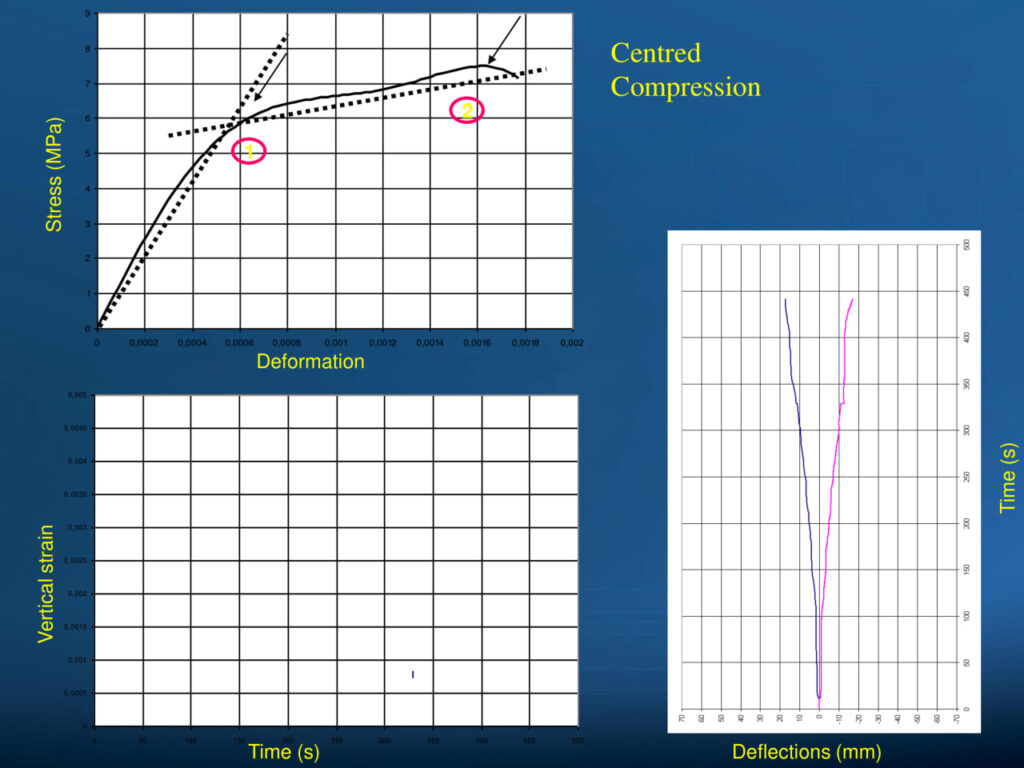
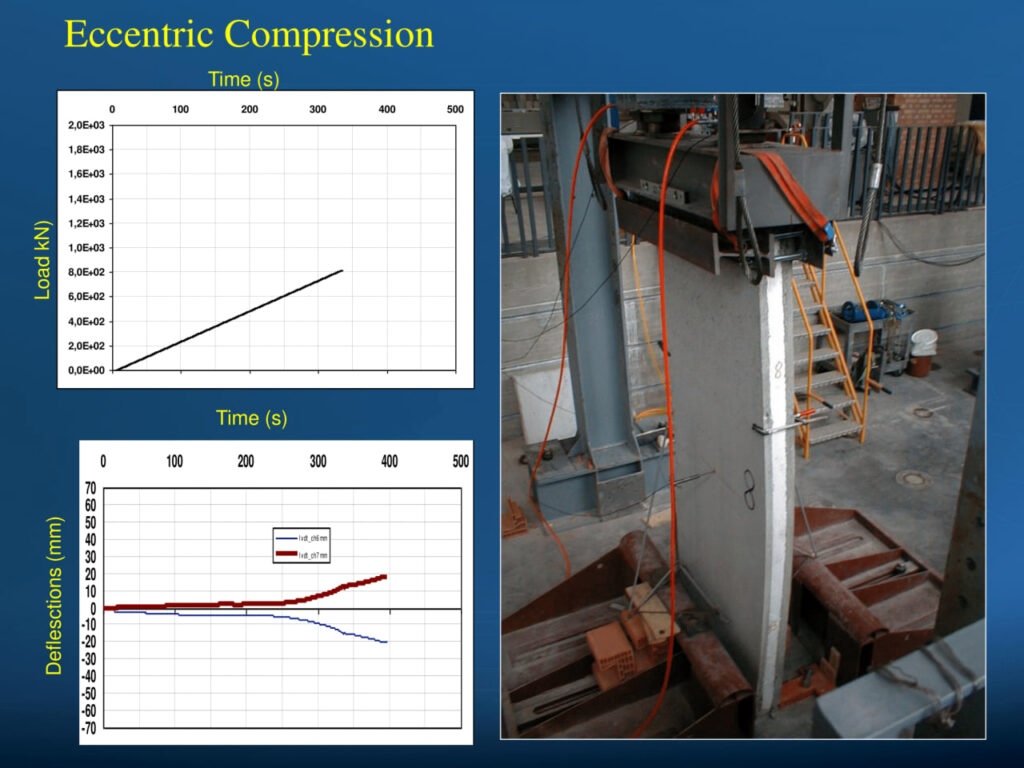
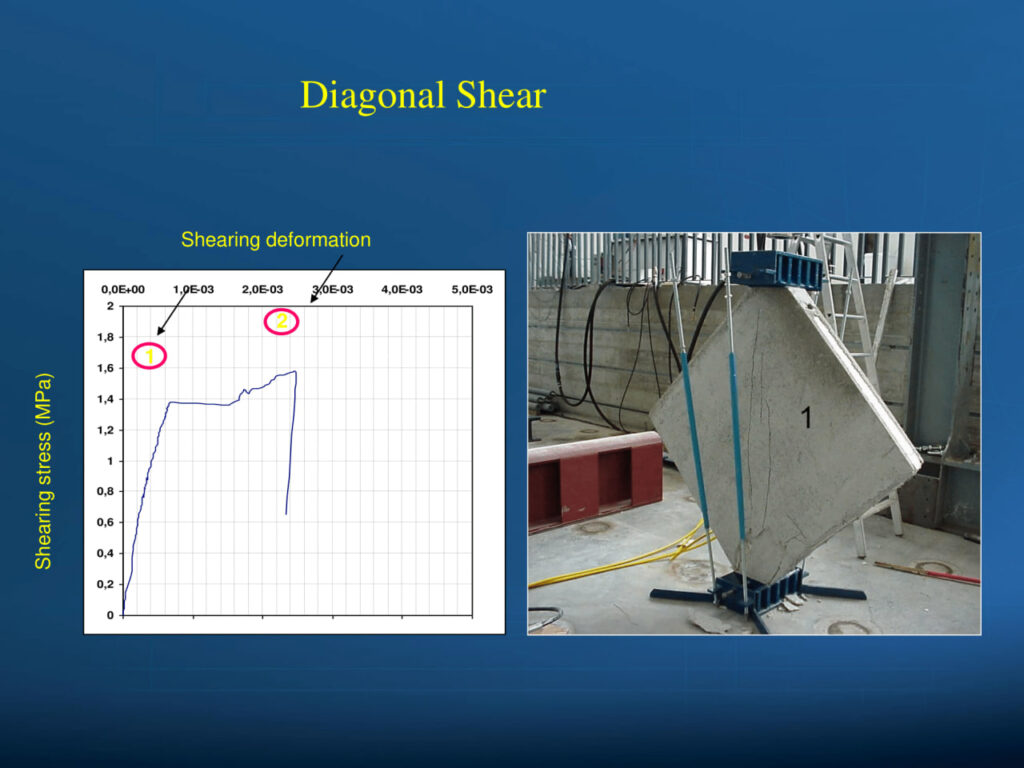
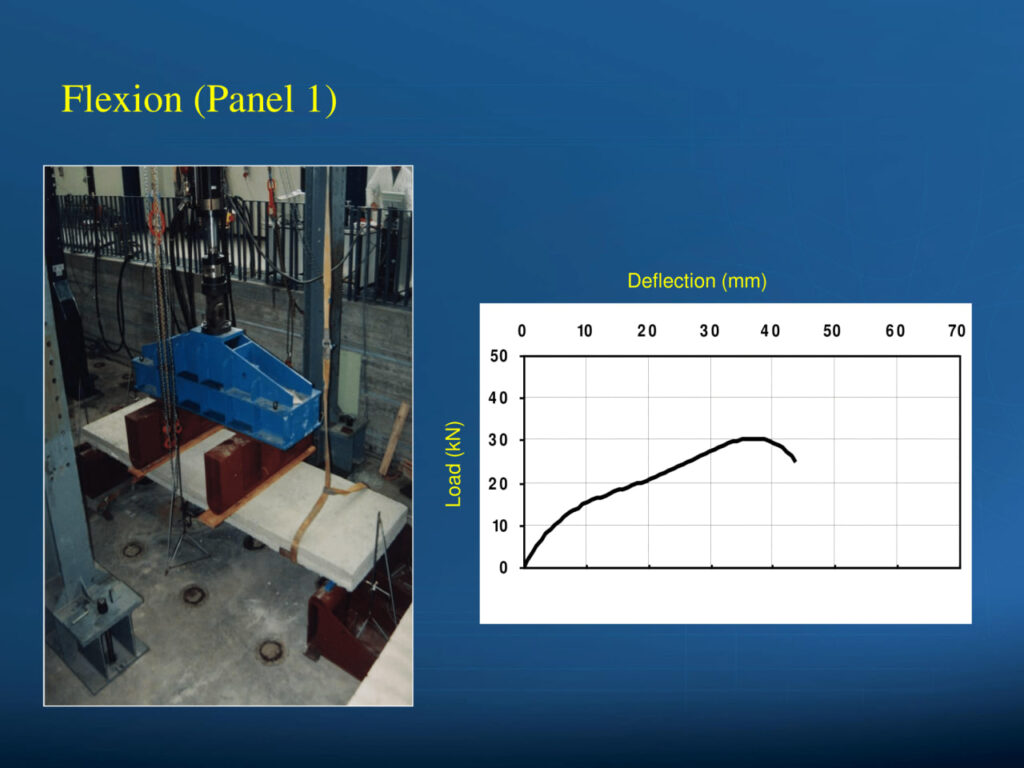
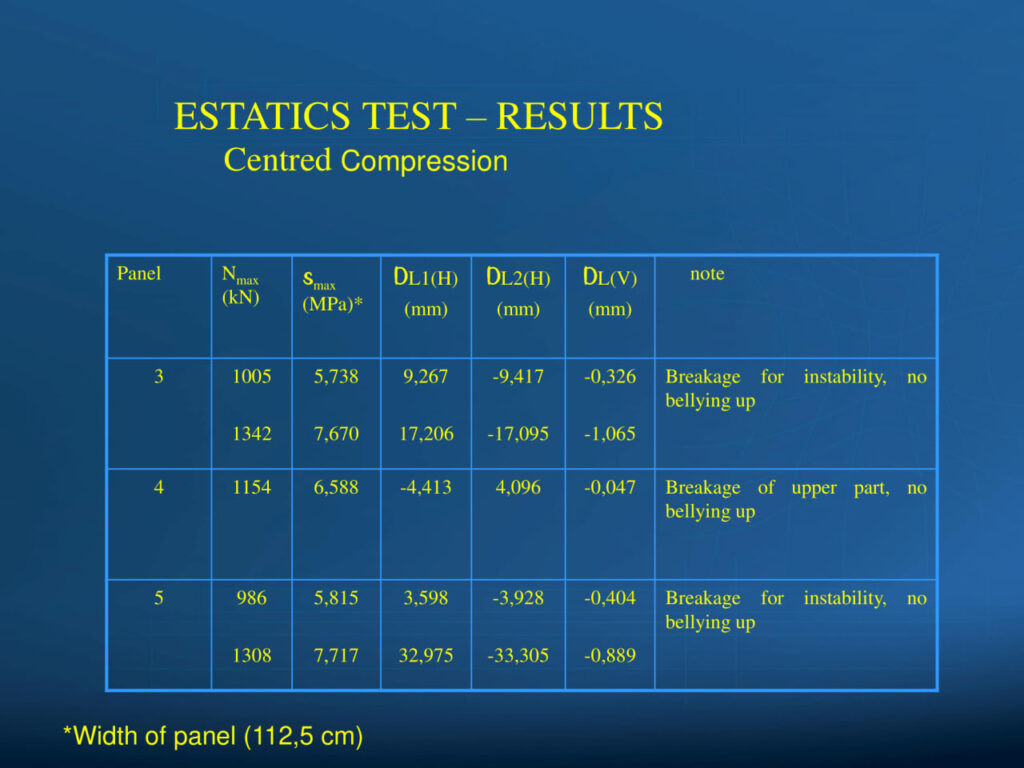
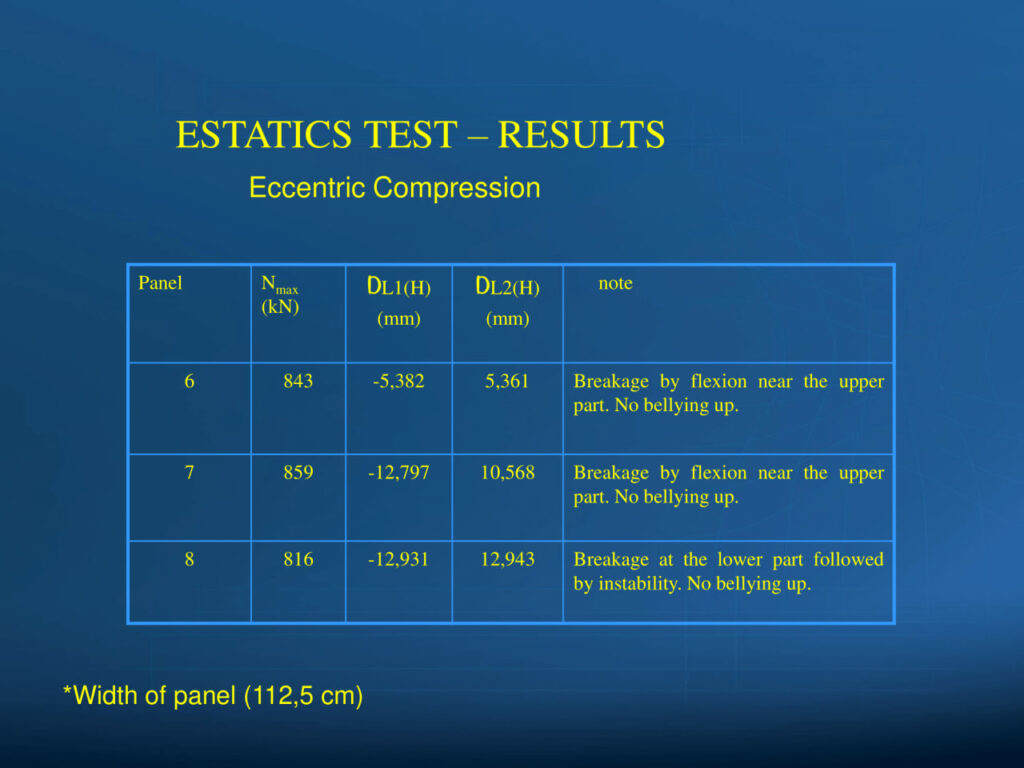
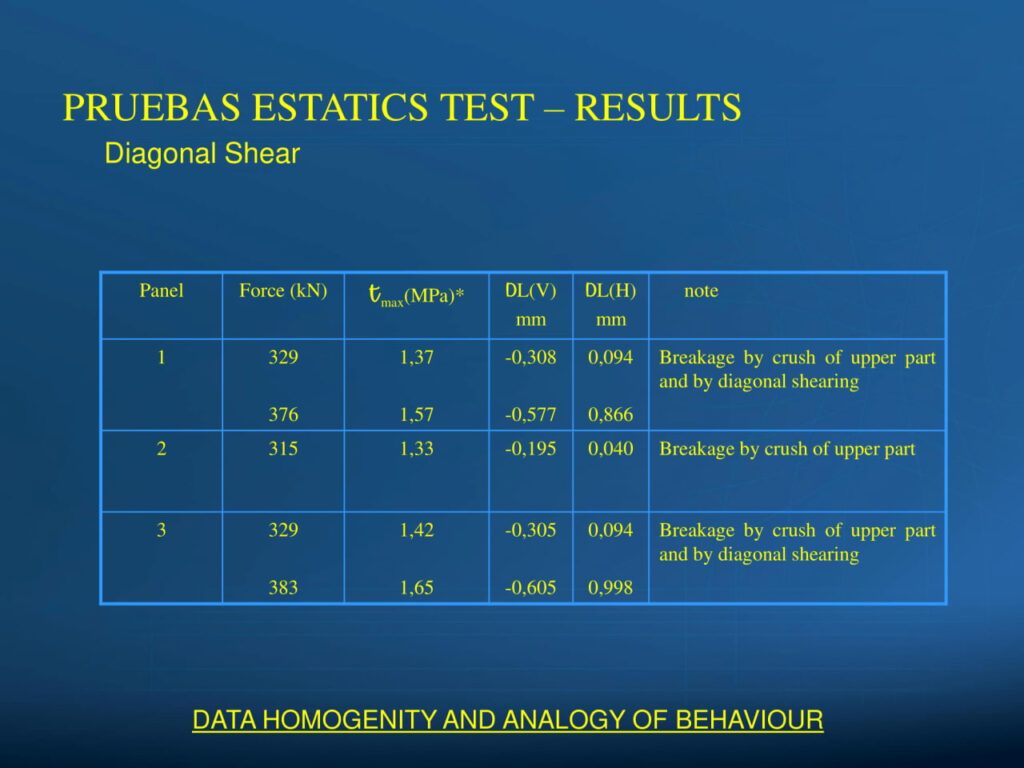
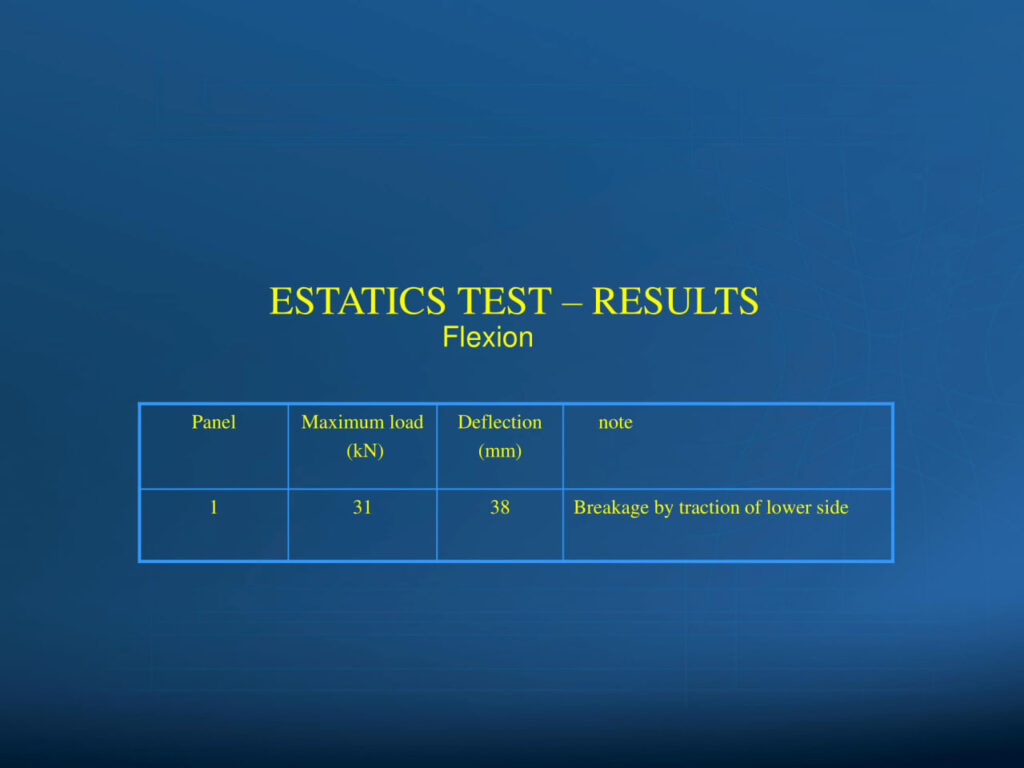
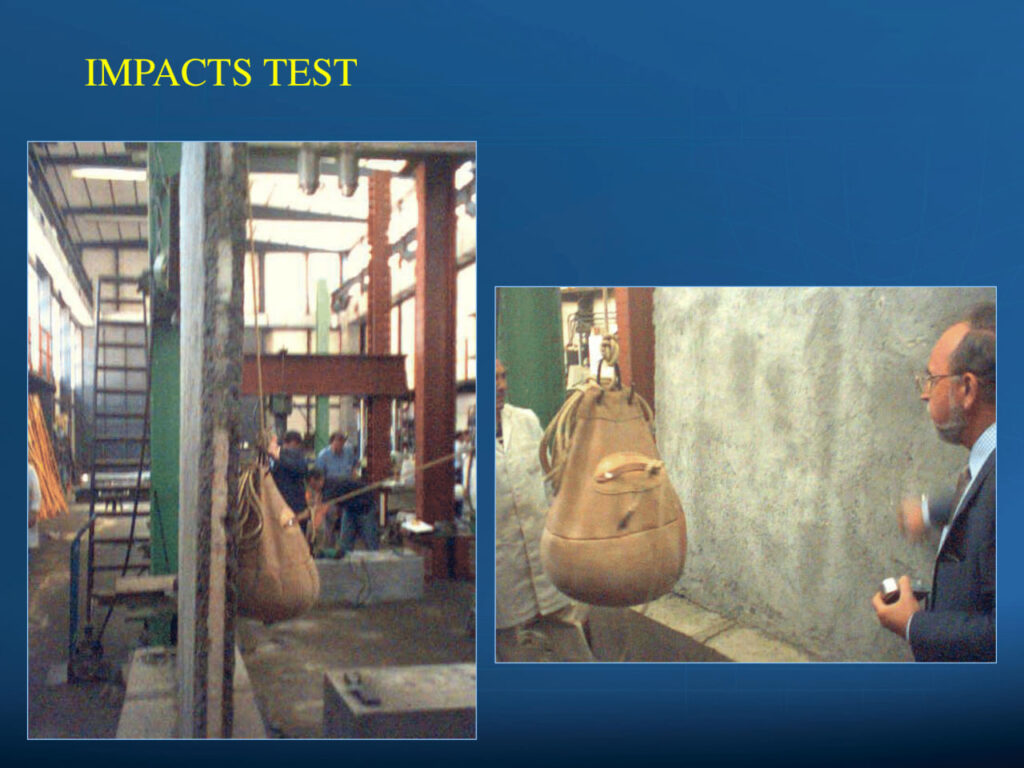
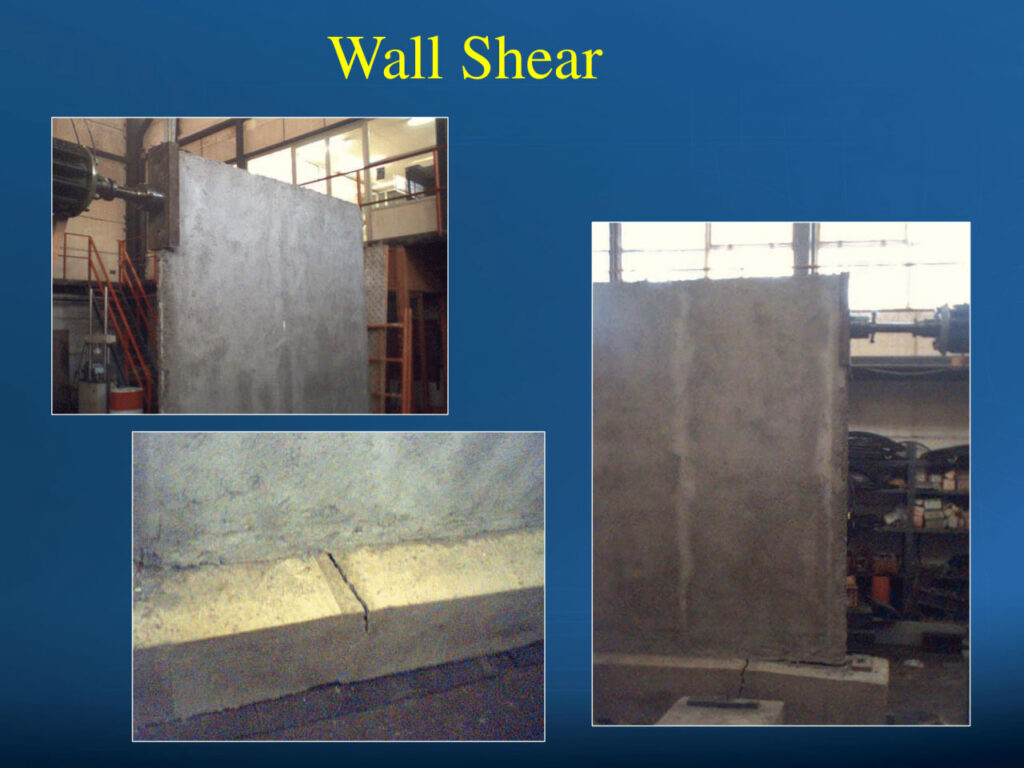
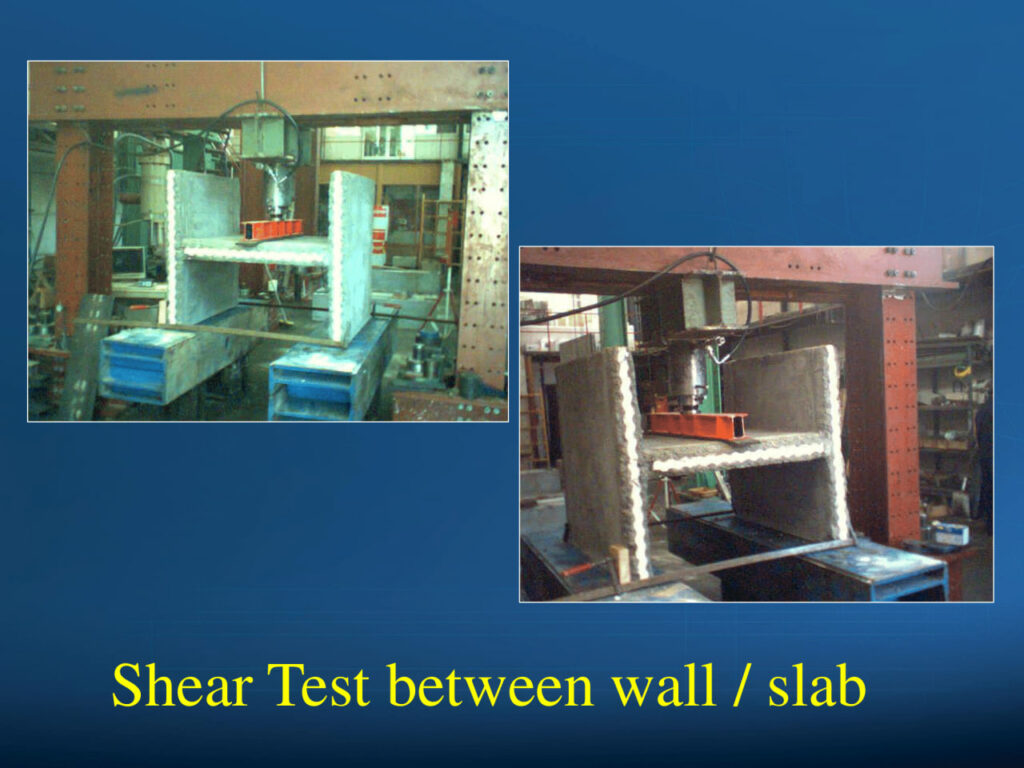
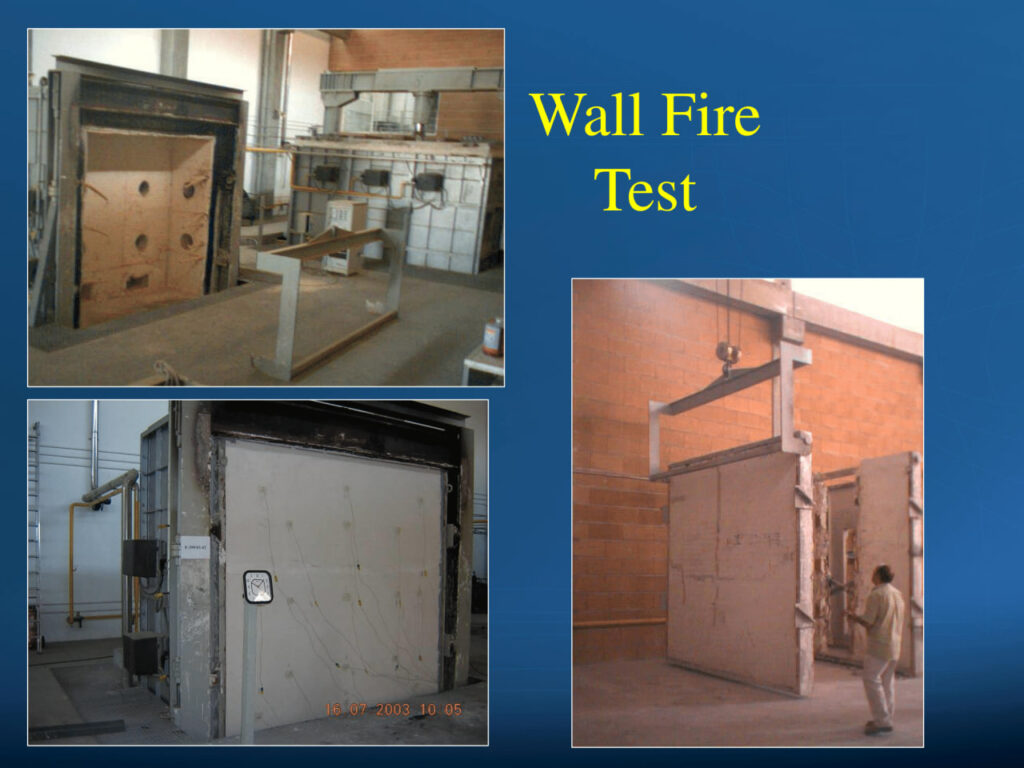
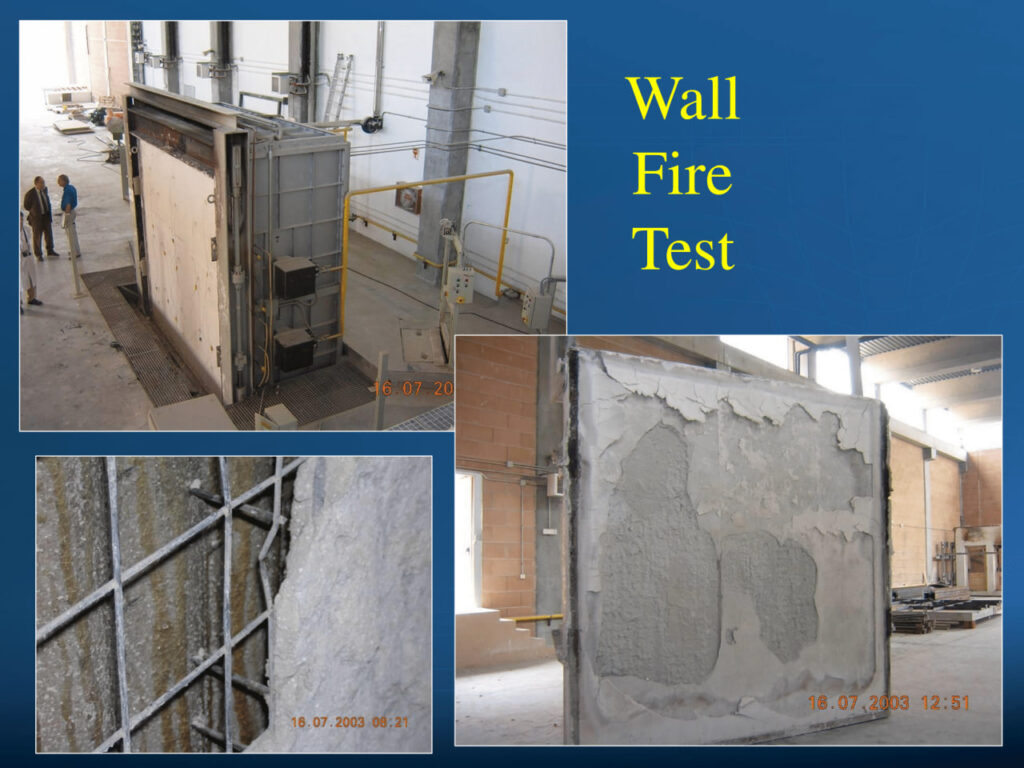
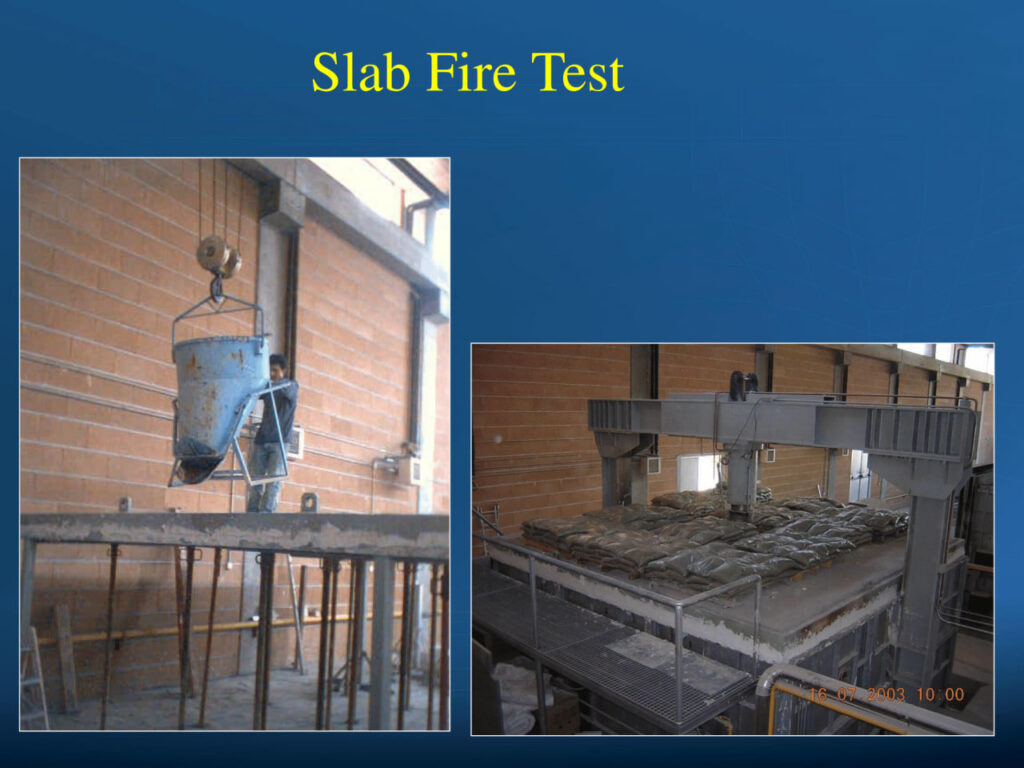
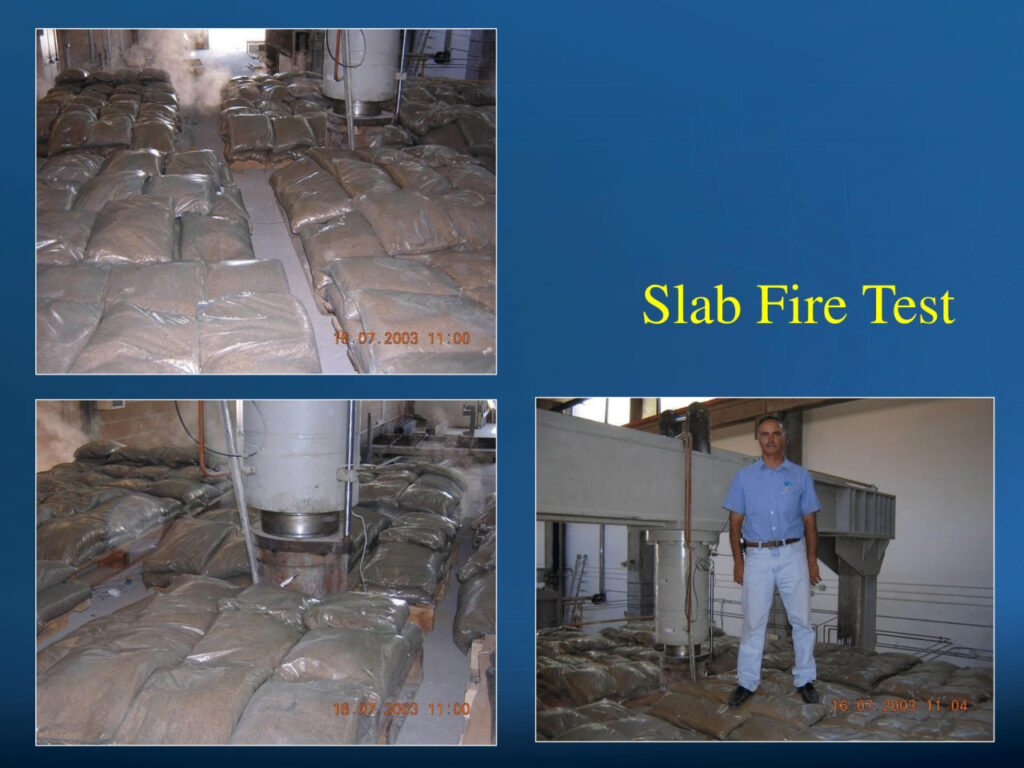
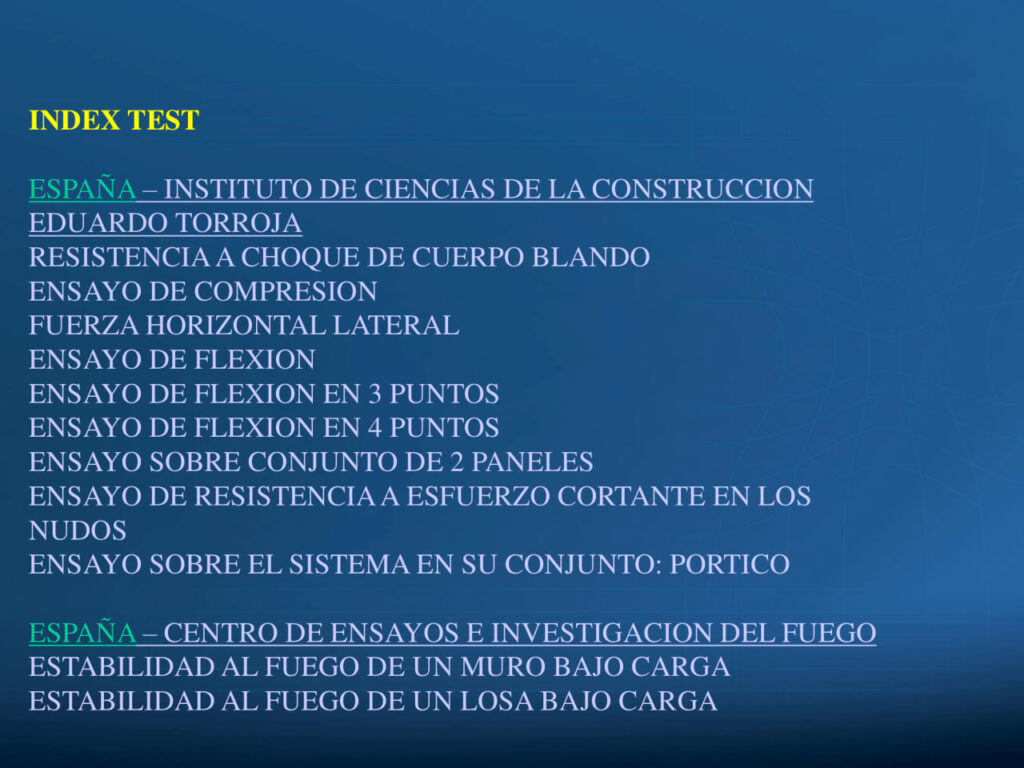
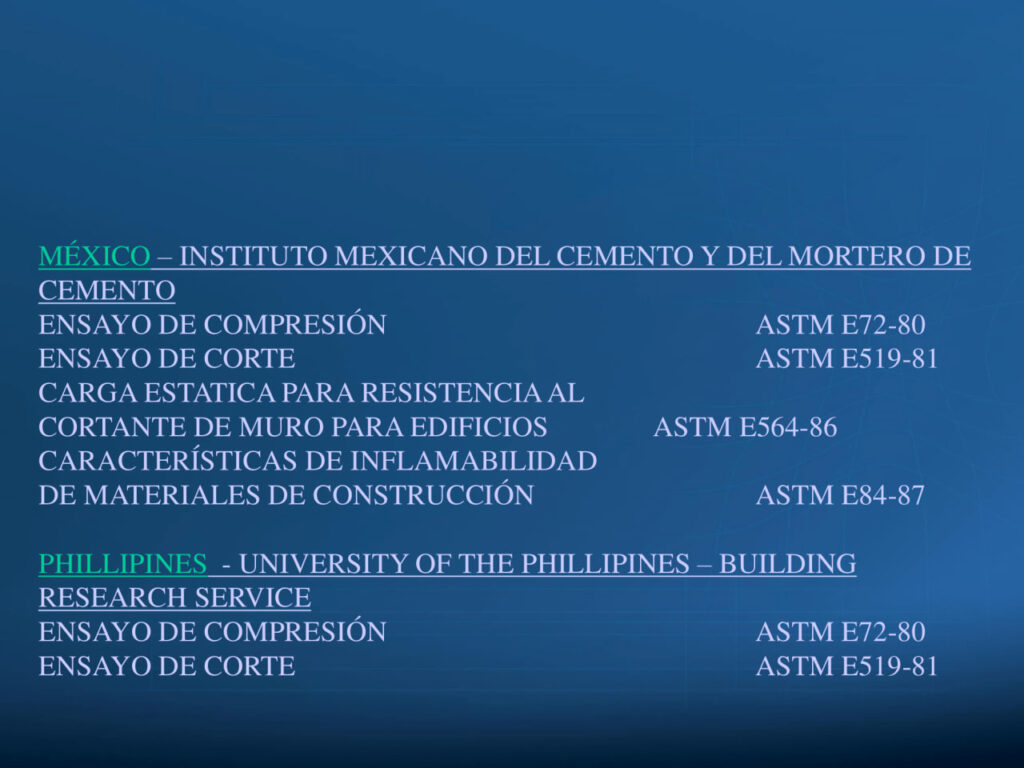
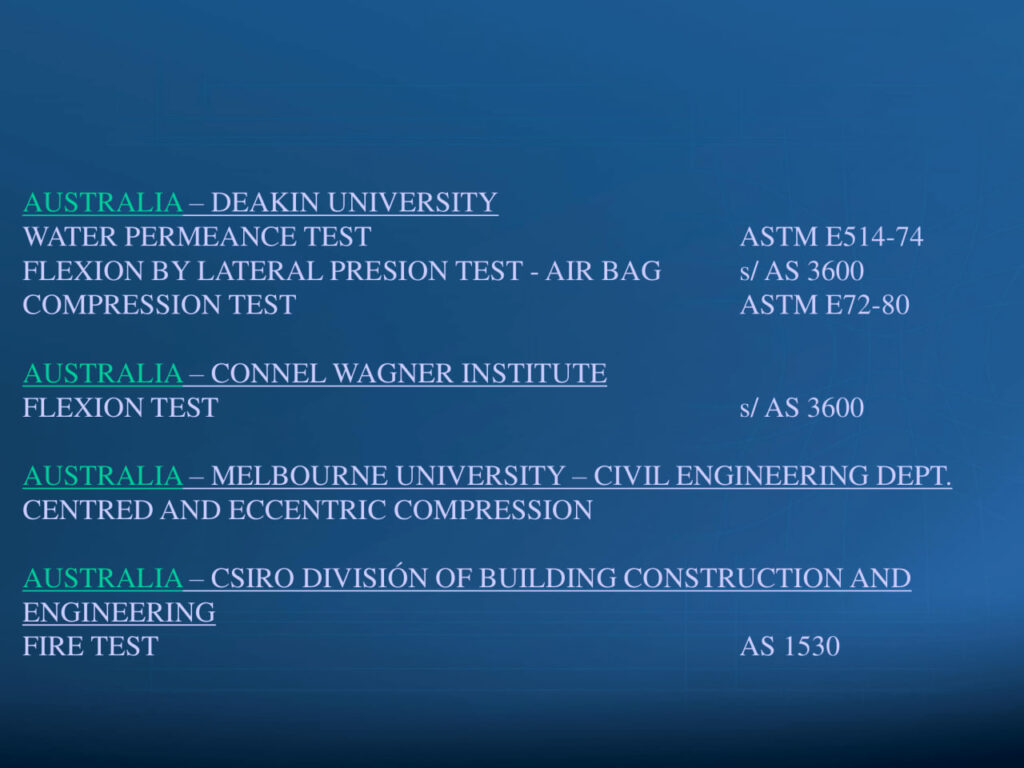
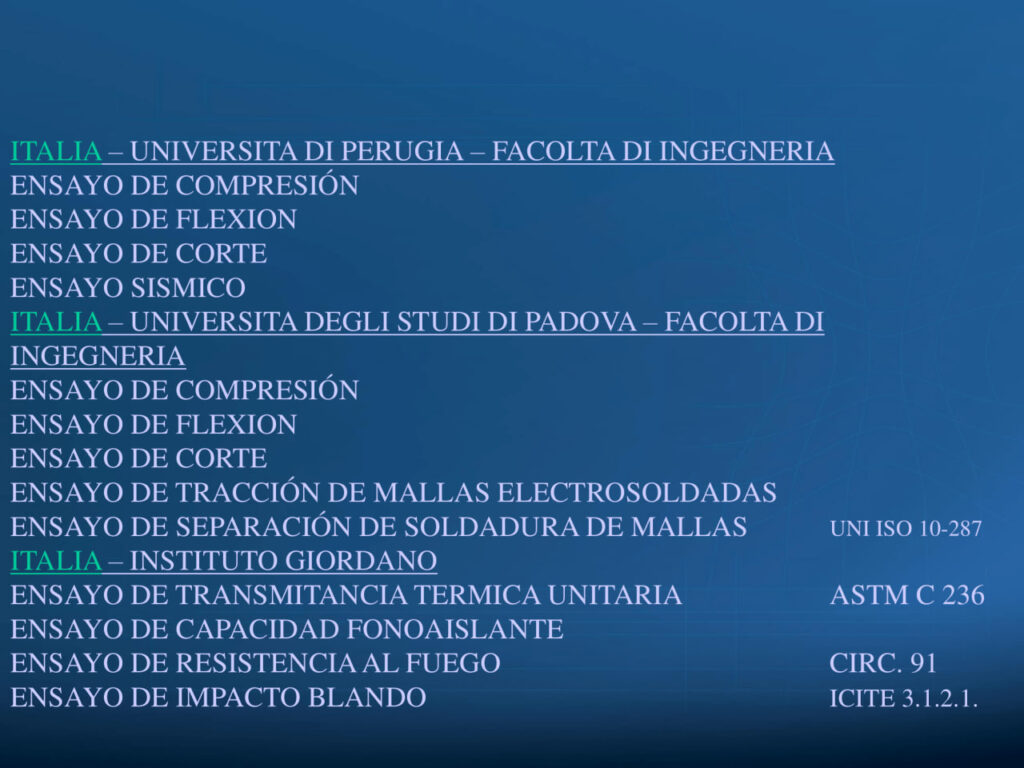
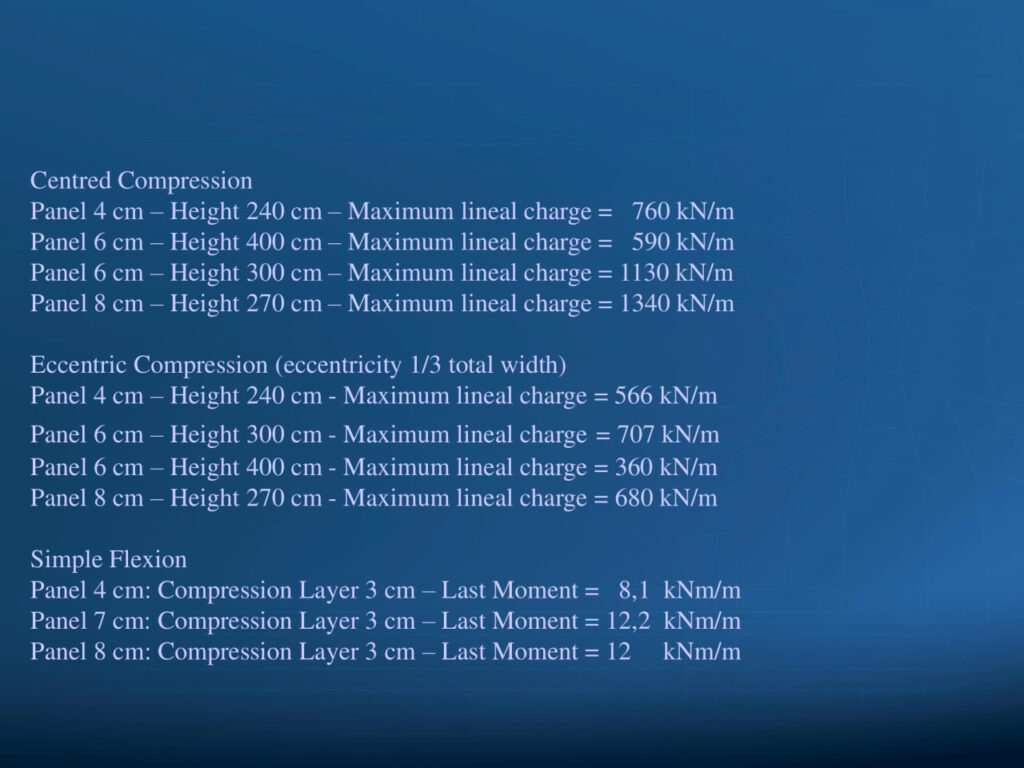
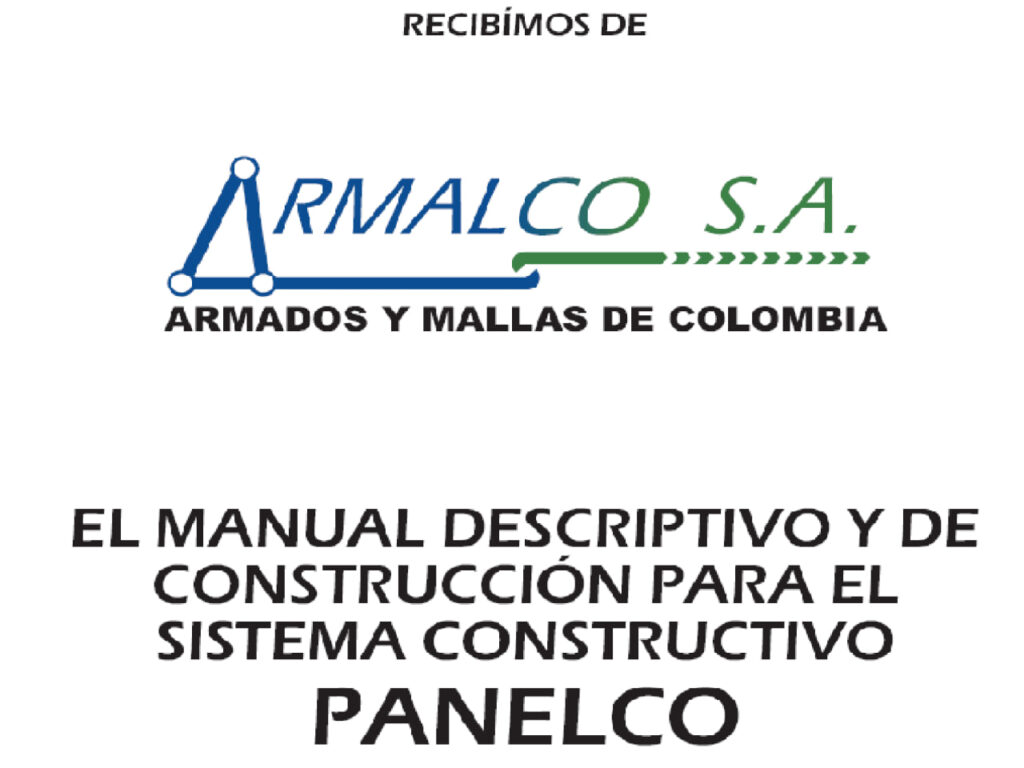
SISTEMA PANELCO
CASAS DE 1 PISO Y CUBIERTA PANELCO
SISTEMA PANELCO
CASAS DE 2 PISOS Y CUBIERTA EN TEJA FIBROCEMENTO
SISTEMA PANELCO
USADO COMO MUROS DIVISORIOS Y DE FACHADA EN OTROS SISTEMAS ESTRUCTURALES
POSIBILIDADES ARQUITECTÓNICAS

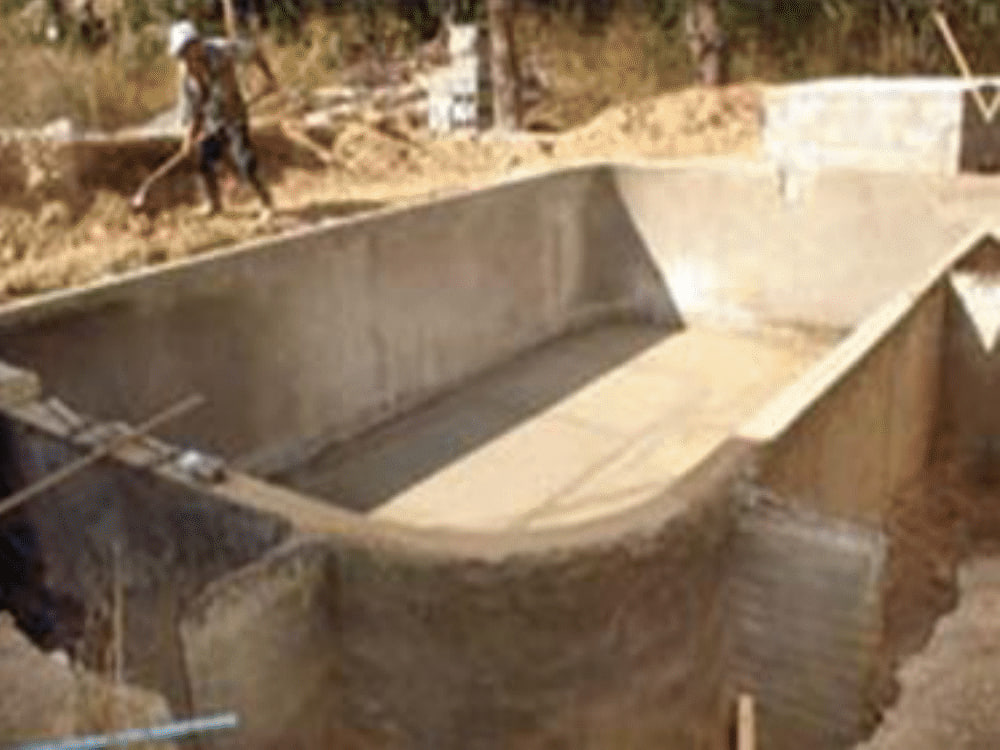
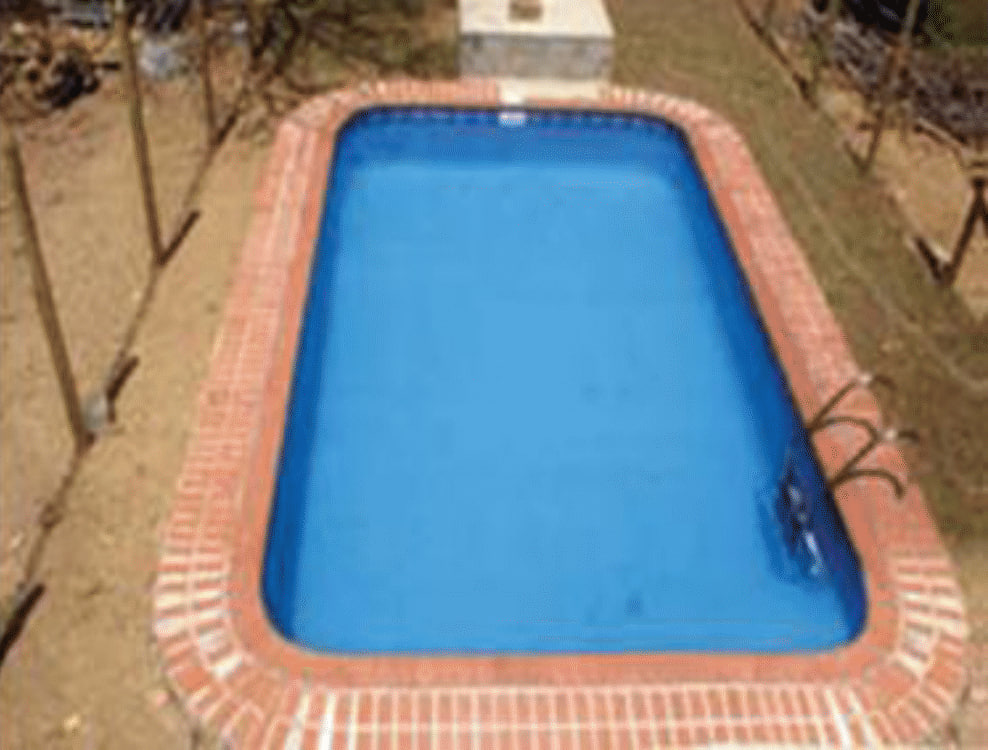
Instalación
Estructura Metálica Cubierta
Descripción del proceso
- Material en obra
- Pintura
- Selección de elementos a izar
- Izado columnas
- Instalación de columnas
- Verificación de verticalidad y ubicación columnas
- Anclaje columnas
- Verificación de alineamiento y verticalidad de las columnas
- Planeación movimientos
- Izado cerchas
- Giro del elemento
- Colocación cercha sobre columna
- Verificar posición de la cercha sobre la columna
- Soldadura cercha columna
- Correr líneas de alta tensión para instalar las cerchas de cubierta
- ¡Ojo! con el arco eléctrico, ¿seguridad?
- Anclado de la cercha
- Avance de instalación
- Tensado y alineamiento de cerchas
- Instalación de correas metálicas
- Planeación de movimientos
- Dificultad de movimiento
- Velocidad movimientos = costo de instalación
- Coordinación izado cercha
- Una hora después final instalación cerchas
- Instalación correas y tensores
- Cubierta en teja metálica fabricada en obra.
Descripción
- Coordinación modular
- Despiece de refuerzos
- Especificaciones
- Detalle de conectores entre muros
- Detalle de conectores muro – placa
- Detalle de viga intermedia
- Detalle refuerzo horizontal
- Normas técnicas
Descripción
- Base en afirmado e instalaciones hidráulicas
- Instalación de acero de refuerzo, cimentación y dovelas
- Placa fundida y curado con riego de agua
- Trazado y forme mampostería estructural
- Modulación horizontal dovelas
- Modulación horizontal redes
- Modulación vertical plomado boquilleras
- Colocación de unidades de mampostería usando boquilleras
- Modulación vertical plomado de hilos
- Refuerzo vertical, conectores entre muros
- Colocación de unidades de mampostería usando “Madrino o Punto”
- Detalle templado de hilo
- Corte con pulidora
- Cortadora industrial
- Emboquillado
- Estriado y emboquillado
- Limpieza de celdas para fundir dovelas
- Fundida de dovelas
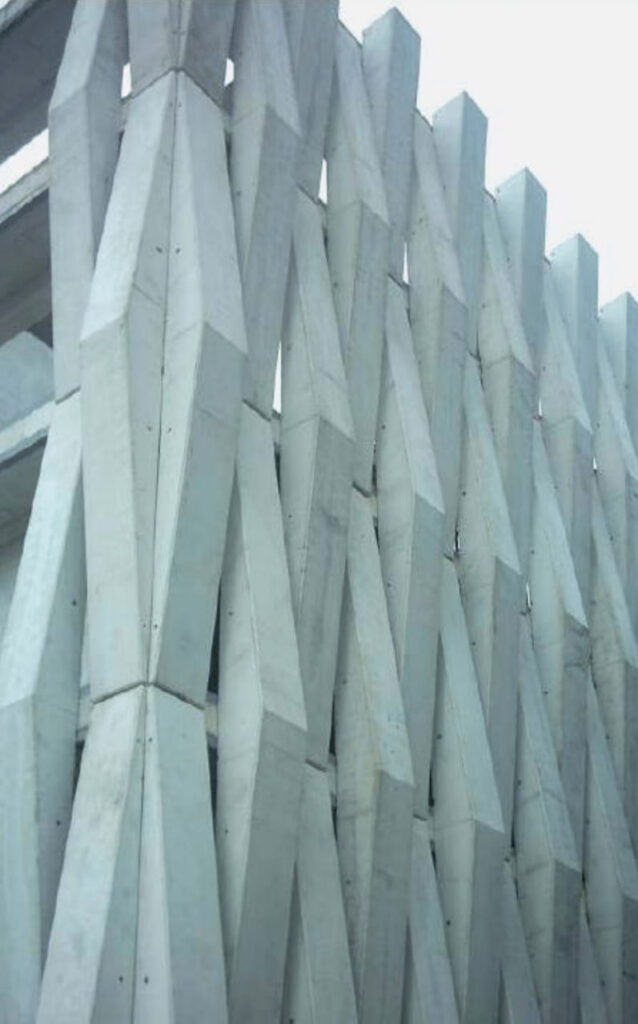
“Fachada prefabricada”
En concreto liviano
o Dado que los elementos prefabricados no tienen funciones estructurales, se requirió el diseño de anclajes metálicos soldados, que mostrarán buen comportamiento ante solicitaciones sísmicas.
o En el proceso de diseño se tienen en cuenta los requerimientos de carga por desencofre izado y montaje de los elementos prefabricados, encontrando que la condición crítica corresponde al izaje.
o Para el diseño y construcción de los elementos de fachada se uso concreto liviano (aligerado con poliestireno expandido y con el uso de aditivos que permiten una distribución uniforme en la mezcla) el peso se reduce entre un 25 y un 50% del peso normal, además se uso concreto de alta resistencia inicial, lo que permitió reducir la resistencia de diseño de 28 a 21 mpa.
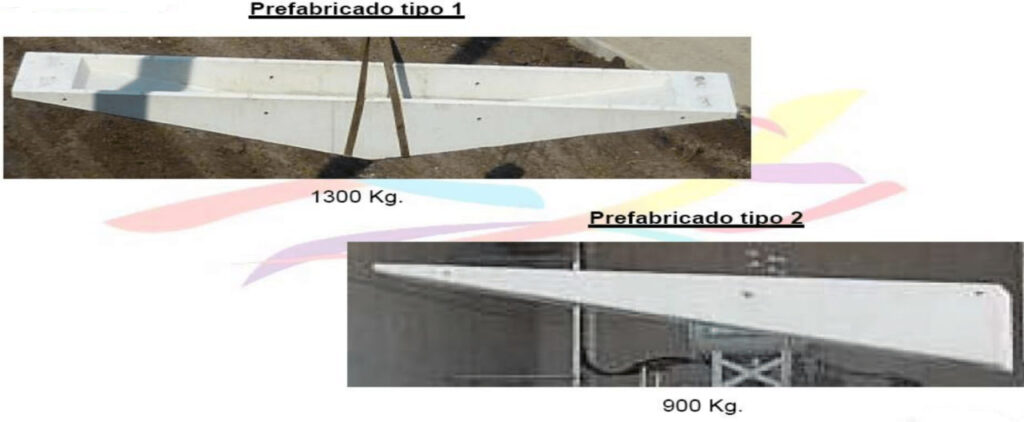
Para obtener excelentes resultados estéticos se tuvo en cuenta:
o Formaletas con ángulos adecuados para el desencofrado.
o Diseño de elementos de izado que evitaron el uso de ganchos metálicos embebidos en el elemento.
o Diseño de elementos para manipular, transportar e izar los elementos, evitando daños por golpes y roces.
Refuerzo en Acero
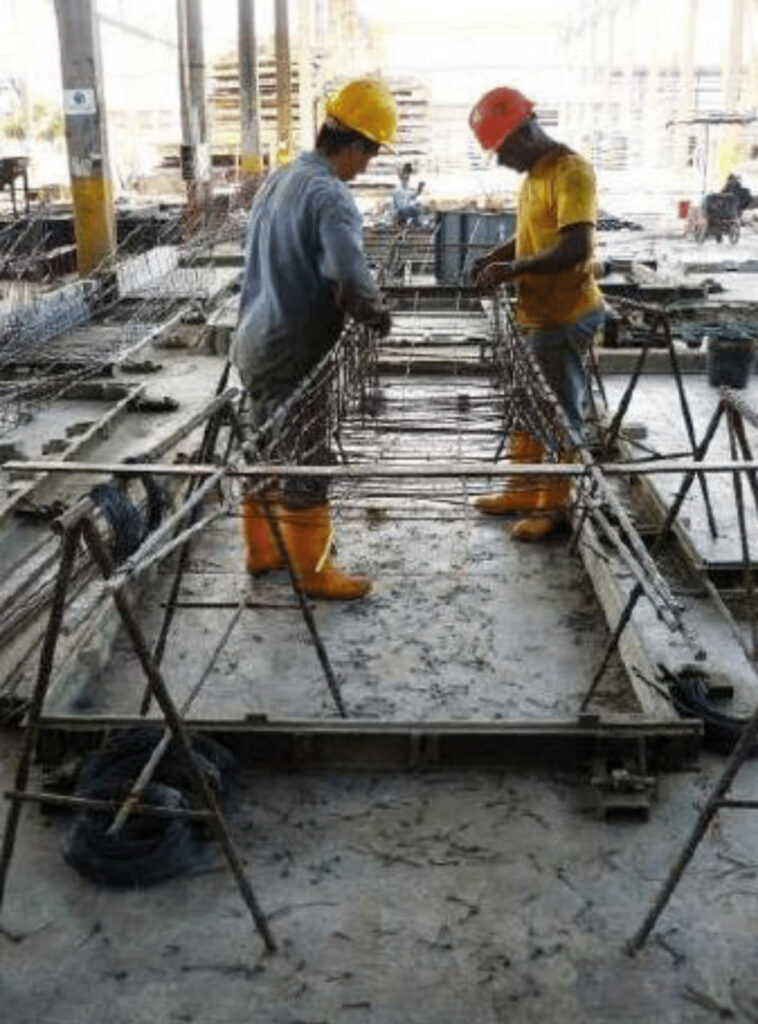
Patio de Almacenamiento
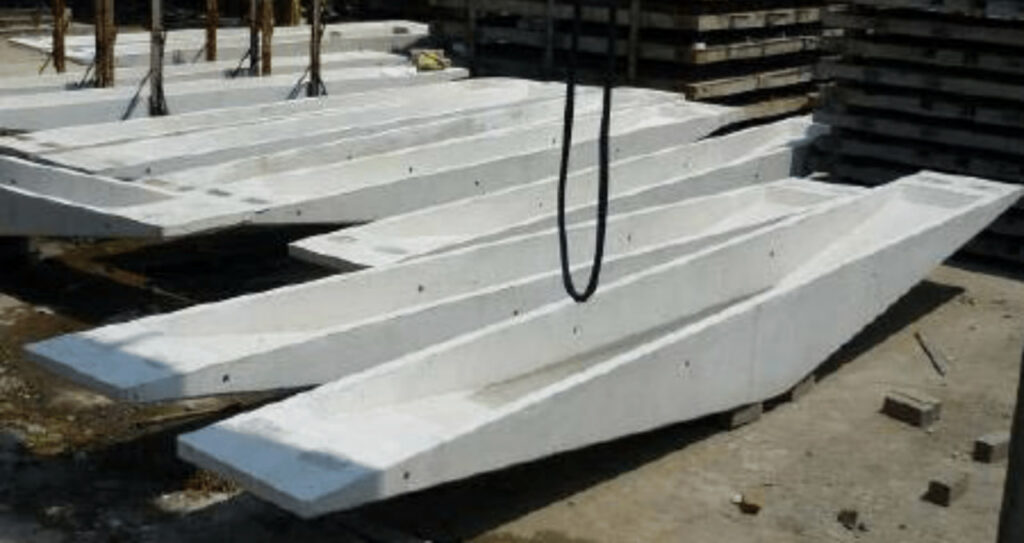
USO DE CONCRETOS CLAROS
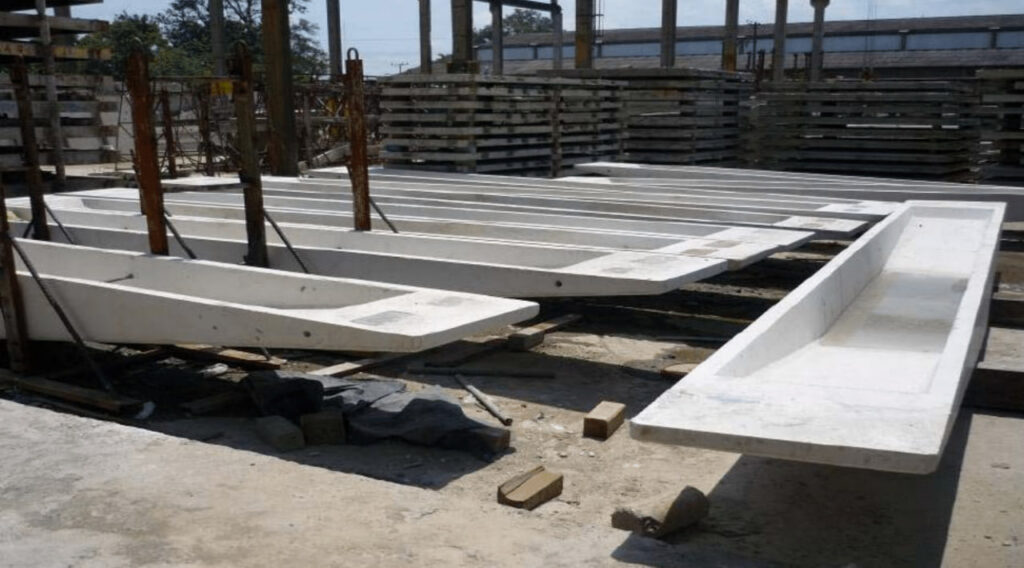
IZAJE DE ELEMENTOS
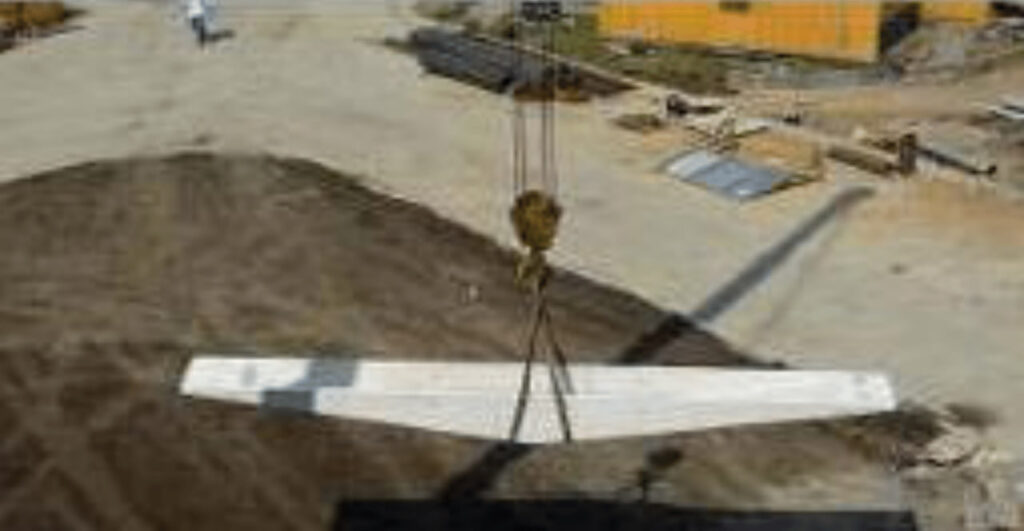
Descripción del proceso
- Tipos de casetón
- Placas aligeradas con casetón
- Organización en planta
- Instalación de la armadura
- Encofrado
- Encuellar columnas
- Enconfrado en planta
- Trazado de redes y estructura
- Instalación de concremalla para la torta
- Revisar encofrado y amarre de acero
- Revisar amarre de acero
- Prolongar redes
- Instalar testeros de borde
- Revisar desniveles en desagües
- Medir casetón
- Adecuar casetón
- Apilar caseton para colocar la torta
- Colocar concreto de la torta con bomba estacionaria
- Colocar concreto de la torta con torre grúa
- Colocar concreto de la torta con autobomba
- Instalar el casetón definitivamente
- Instalar acero de refuerzo recubrimiento
- Emplazamiento de equipos de bombeo
- Autobomba
- Armado de tubería bomba estacionaria
- Purga de la tubería
- Bombeo del concreto
- Colocación del concreto con torre grúa
- Vibrado del concreto
- Fundir viguetas, vigas y recubrimiento
- Puntear y tallar el recubrimiento
- Acabado
- Curado con riego de agua
Placa con vigas prefabricadas y aligerada con bovedillas de concreto
Descripción del proceso
- Viguetas prefabricadas
- Bovedillas prefabricadas en concreto
- Nivelación de la mampostería
- Instalación de la armadura e izado de las vigas prefabricadas
- Modulación de vigas y bovedillas
- Nivelación de las vigas prefabricadas
- Chequeo niveles y modulación
- Instalación de bovedillas
- Corte y adecuación de bovedillas
- Amarre estructural y placa mampostería estructural
- Amarre entre viguetas alineadas
- Trazado de las instalaciones entreplaca
- Instalaciones entreplaca
- Preparación de concreto en obra
- Transporte vertical
- Colocación y vibrado del concreto
- Nivelación de la capa de recubrimiento
Placa aligerada con bloque de arcilla y vigas fundidas In Situ
Descripción del proceso
- Materiales en obra
- Encofrado
- Banco de herrería
- Amarre de acero
- Chequeo
- Instalación bloque de arcilla
- Instalaciones entreplaca y alineamiento final bloque
- Mezclado manual del concreto
- Instalación manual del concreto
- Vibrado del concreto
- Fundida ordenada
- Limpieza de elementos
- Fundida del recubrimiento
- Curado con riego de agua durante 7 días
Sistema Panelco casas de 2 pisos y cubierta en teja fibrocemento
Sistema de prelosa
Este tipo de placas de entrepiso es utilizado para luces relativamente cortas (4,00 m o menores) que es donde pueden ser económicamente viables; su espesor estará dado por la luz que se debe vencer, pero por lo general tendrán espesores menores de 20 cm y se encontrarán apoyadas a lo largo en por lo menos dos de sus extremos, en muros más que en columnas.
En algunos casos para este tipo de placas se recurre al sistema conocido como Prelosas, donde se prefabrica alguna porción del espesor de la placa, que se usa como encofrado, y el faltante se vacía sobre esta. A la prelosa se le dejan unos refuerzos salientes hacia arriba conocidos como conectores de cortante y cuya función es integrar la parte prefabricada a la parte vaciada en sitio para que trabajen como un conjunto.
Descripción del proceso
- Construcción de vigas principales
- Instalación viguetas prefabricadas
- Prelosa
- Izado y montaje Prelosa
- Fundida recubrimiento
- Junta viguetas
- Acabado final