o La producción de estos elementos pretensados debe ser realizada con equipos adecuados y diseñados específicamente para este fin, en bancos de pretensado de línea larga, usando para la conformación de la placa máquinas extrusoras o moldeadoras. El ancho nominal estándar es de 1.200 mm y el rango de espesores puede variar entre 80 y 300 mm, siendo posible la fabricación de hasta 500 mm. Los aligeramientos o alvéolos varían en forma, tamaño y número dependiendo del equipo usado en su manufactura.
o Los bancos de prefabricación varían entre 100 y 200 m de longitud. Los fondos de las camas pueden ser de diversos materiales, aunque se recomienda que sean de acero para mejorar el acabado de la parte inferior de la placa e incorporar sistemas de curado con calor que aceleren el proceso de endurecimiento del concreto. Posteriormente las placas son cortadas de acuerdo con la modulación especifica de cada proyecto.
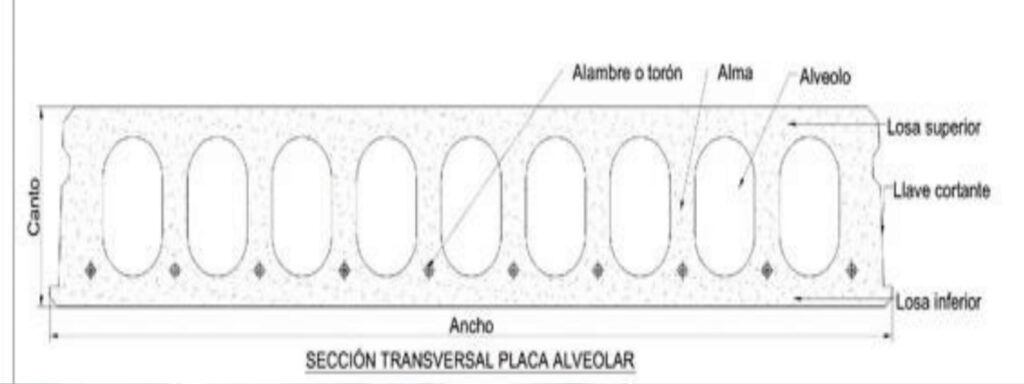
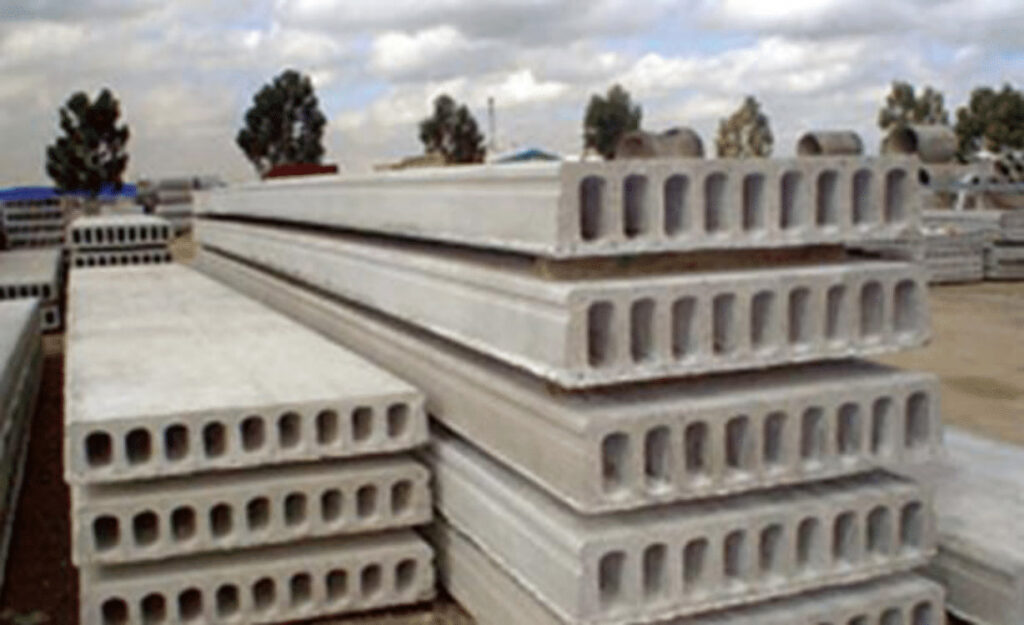
SECCIÓN TRANSVERSAL
FABRICACIÓN
o El proceso productivo de las placas alveolares inicia con la preparación de la pista (línea de producción sobre la cual se funden las placas). Esta se limpia y se le aplica un desencofrante que evita que se le adhiera el concreto; luego se procede a la extensión de los alambres o torones definidos en diseño entre bancadas (extremos de la pista) donde son anclados pasivamente mediante piezas especiales con cuñas; se cortan los alambres o torones y se sujetan al gato hidráulico que tira de ellos traccionándolos hasta la tensión de diseño y se acuñan en la cabeza de anclaje activo, que forma parte de la bancada correspondiente. La bancada desde la cual se traccionan las armaduras recibe el nombre de “activa”, mientras que la opuesta es la “bancada pasiva”, ambas vinculadas a través de la losa de compresión que completa la infraestructura resistente de cada pista de producción.
o Una vez que las armaduras se encuentran pretensadas entre ambas bancadas, se sitúa la máquina moldeadora sobre los carriles de la pista. Al tiempo que la máquina avanza, asegura la posición de la armadura mediante el “guía – hilos” situado en su parte delantera, y va depositando el concreto con la forma y dimensiones que corresponda a la placa alveolar que se esté fabricando.
o La mezcla de concreto debe tener una consistencia muy seca, de modo que mantenga la forma y dimensiones definidas, por lo que debe ser enérgicamente vibrado por la máquina para que envuelva perfectamente los refuerzos y rellene totalmente los moldes deslizantes.
o Terminada esta fase, se cubre la pista con una lona para retener la humedad y evitar cambios bruscos de temperatura durante el proceso de curado del concreto. Una vez se alcanza la resistencia requerida (entre 10 y 12 horas para pistas con calefacción y entre 36 y 48 horas a temperatura ambiente), se procede a distensionar los alambres o torones de refuerzo.
o Posteriormente, las placas alveolares son cortadas a la medida – de acuerdo con la modulación particular de cada proyecto – mediante máquinas cortadoras equipadas con un disco diamantado.
o Finalizado el corte y la marca, las placas se extraen y se trasladan al patio para almacenamiento y posterior despacho.
o Para asegurar la calidad del producto debe elaborarse un plan de ensayos sobre los materiales utilizados en el concreto y acero de refuerzo. Igualmente, a las placas alveolares terminadas se les debe hacer pruebas de resistencia a flexión, cortante y deformación bajo carga.